Why does chemical synthesis matter?
The importance of chemical synthesis is undeniable. Learning from processes that occur in nature to recreate them in the laboratory and creating new ones has brought significant advances to society. In the pharmaceutical industry, it has brought and keeps bringing new drugs. In material sciences, the applications are countless, from aerospace to green technology. It also plays a vital role in addressing current global changes, such as sustainable agriculture, clean energy, and the protection of the environment.
In the following sections, we will discuss the main phases in the chemical synthesis pipeline – Discovery, Process Development, and Scale-up – their importance, their main challenges, and how we can address them.
Discovery
How can we improve the discovery of novel products?
Productivity
Due to its iterative nature, the discovery phase sometimes takes a long time, in which each one of the different parameters needs to be evaluated. Often, finding the optimal for the process requires slightly modifying the conditions of the experiment. There are specific ways in which the productivity of this phase can be improved.
The ability to run separate reactions individually allows for the testing of different conditions simultaneously and enables the testing of different parameters in the search for optimal conditions. These parameters can include physical parameters – e.g. temperature, agitation, pressure – or chemical – e.g. pH, ionic concentrations, and different reagents. On the other hand, repetition and replicability are intrinsic to science. Having multi-reactor systems enables experiment replication, diminishing potential variability within the tests and increasing the statistical robustness of the data.
Space
The space that instrumentation occupies can be detrimental to the productivity of laboratories and industrial processes, especially when there is space limitation. The miniaturization of vessels reduces the amount of reagents and materials required for each reaction, optimizing space and reducing waste without losing the control capabilities of larger systems. Additionally, multi-reactor systems can be operated using a single computer instead of having one per, further reducing the amount of space required.
Safety
In the discovery phase, different conditions must be tested to find the ideal conditions for the reaction. The product yield and the reduction of costs to run the process are fundamental parameters in finding the perfect process. However, safety cannot be ignored.
In order to design safer processes, different conditions need to be tested. For example, other reagents can produce the same product. It could also be that byproducts can be hazardous (e.g. toxic, or gases that can accumulate, increasing the pressure to dangerous levels). Testing different reagents is costly and time-consuming, but multi-reactor approaches can significantly reduce the time this stage takes.
Heat accumulation can be an issue at the industrial scale when the heat does not dissipate at a high enough rate. In this case, testing for different conditions, such as semi-batch fed systems, can help to mitigate issues. Adiabatic calorimetry is a powerful tool to test the safety of chemical processes. An in-depth characterization of the process can help detect potential exotherms – the temperature at which the heat produced by the reaction becomes high enough to accelerate the reaction, entering a potentially dangerous positive feedback loop. Adiabatic calorimetry can help determine crucial safety parameters like the maximum temperature of the synthesis reaction or the time to maximum rate.
In conclusion, the discovery phase is a meticulous and iterative process that relies on hypothesis testing through controlled experiments. To enhance productivity at this stage, multi-reactors operating individually can evaluate diverse conditions simultaneously, ensuring data robustness through replication. Miniaturization of reactor systems can also help reduce the spaces taken by instrumentation, allowing for smaller volumes and consequently reducing reagent consumption and waste generation. Optimization should always include a safety evaluation of the process and the reduction of potentially hazardous conditions, such as the production of dangerous byproducts and heat accumulation.
Solutions
H.E.L’s PolyBLOCK and AutoMATE are designed as individually controlled reactors, enabling the simultaneous analysis of different synthetic routes and identifying the optimal conditions. Parameters such as conversion efficiency, economic viability, and challenges in the scale-up process can be identified using these solutions. Additionally, the compact design of these platforms reduces the space required for the testing. The flexible nature of these systems and the strict control using H.E.L’s own software help increase the efficiency of the discovery phase. Simular operates as an isothermal calorimeter, enabling in-depth characterization of the thermodynamics and kinetics of the reactions. This allows for the detection of potential hazardous reactions, increasing the safety of the process.
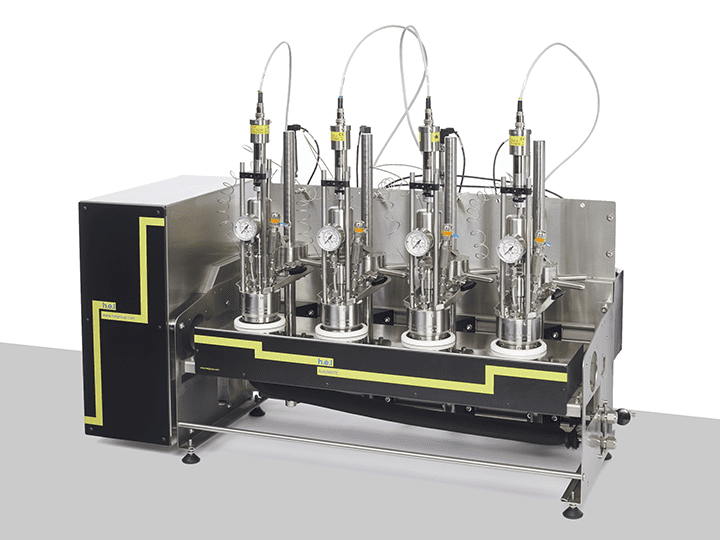
AutoMATE | Linear, Automated Parallel Synthesis Platform
The AutoMATE is a highly versatile, linear, automated parallel synthesis platform, for use...
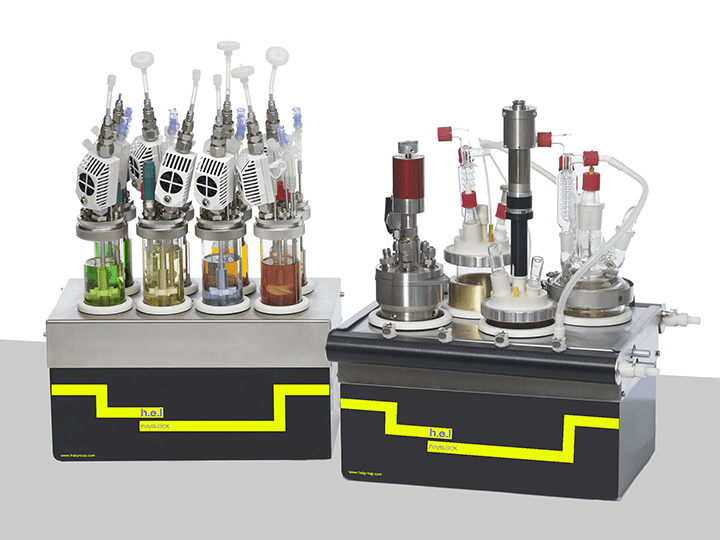
PolyBLOCK | Compact Automated Parallel Synthesis Platform
Key Features – 4 or 8 Independent reaction zones –Independent temperature control (1...
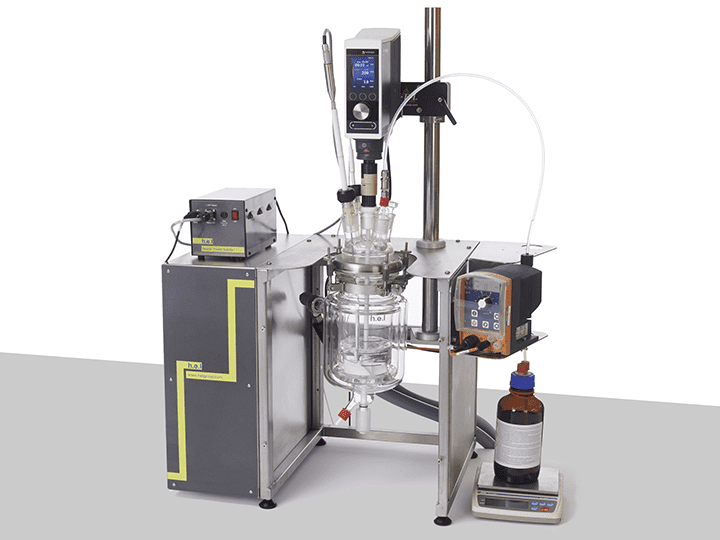
Simular | Process Development Reaction Calorimeter
This highly configurable system from the H.E.L product family excels in optimizing process...
Process Development
What parameters need optimization in the Process Development phase?
Precise temperature regulation
Temperature is one of the physical parameters that impact chemical reactions the most. On the one hand, higher temperatures increase the speed at which molecules vibrate and are transported in the solvent. However, there is a second factor to consider with temperature. For the chemical reaction to occur, the energy of the reaction needs to be higher than the activation energy (Ea).
The Arrhenius equation reflects the relation between the temperature, activation energy, and temperature:
K = rate constant
A = pre-exponential factor
Ea = activation energy
R = universal gas constant
T = absolute temperature
As a result, temperature variation can significantly impact reaction kinetics, product quality, and yield. Employing advanced heating and cooling systems (e.g. temperature-controlled reactions and circulators), temperatures can be maintained within the optimal range throughout the process.
Effective Mixing
One of the first steps in the chemical reaction is the physical contact between the different reagents involved. Diffusion is the process where molecules move following chemical gradients. However, this process is slow. In the absence of stirring, pockets where molecules accumulate occur, reducing the reactivity. Efficient agitation is, therefore, fundamental, and optimization of parameters, such as speed and agitation mechanisms, promote efficient mass transfer and reaction homogeneity.
Comprehensive data recording
In the process development phase, acquiring in-depth knowledge about the chemical reactions and any secondary reactions that might occur is paramount. To achieve this, it is fundamental that robust data is recorded, processed, and analyzed. Closely monitoring critical parameters, including temperature, pH, pressure, reactants, and product concentration, results in robust data acquisition. Real-time analysis tools enable immediate adjustments and informed decision-making.
Reproducibility and standardization are intertwined with the acquisition of high-quality data. Repetition of the same protocol over time ensures that the data obtained is not an anomaly, allowing the prediction of the outcome of the process and understanding of potential risks and hazards. Accurate and representative documentation of each step, including reaction conditions, reagent sources, and equipment calibration, ensures a process that can be consistently replicated.
Safety
Process safety should always be a high priority when developing novel processes. A thorough risk assessment should be performed to identify potential hazards linked to reactants, intermediates, and reaction conditions. This includes the analysis of the compatibility of the reagents used in the process and their store conditions. Safety measures should be implemented, including containment systems, pressure relief mechanisms, and emergency shutdown procedures.
The process development phase combines precision, optimization, knowledge acquisition, and safety consciousness. The meticulous control of parameters such as temperature, recognizing its significant impact on reaction kinetics, is critical. Adequate mixing ensures efficient mass transport, resulting in the homogeneity of the reaction. Comprehensive data recording and analysis are the keystone of informed decision-making, yielding standardized protocol ensuring the reproducibility of the process. Last but most definitely not least, safety consideration through thorough risk assessment and the implementation of safety strategies must never be overlooked. These considerations represent the foundation for effective and successful Process Development.
Solutions
H.E.L PolyBLOCK 4, PolyBLOCK 8, and AutoMATE are designed to reduce the time spent in the process optimization phase. Their capabilities to run different tests in parallel under strictly regulated conditions enables meaningful and reproducible outcomes. The possibility of using over-head stirring can help to ensure homogeneity in the reactor and mimic manufacturing. Additionally, H.E.L’s own software allows for real-time measurements and strict control of the conditions of the experiment, providing optimal conditions while maintaining strict safe conditions.
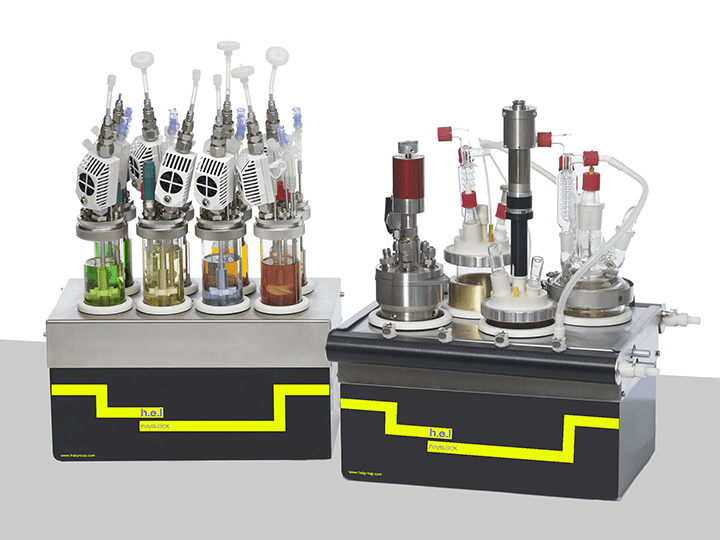
PolyBLOCK | Compact Automated Parallel Synthesis Platform
Key Features – 4 or 8 Independent reaction zones –Independent temperature control (1...
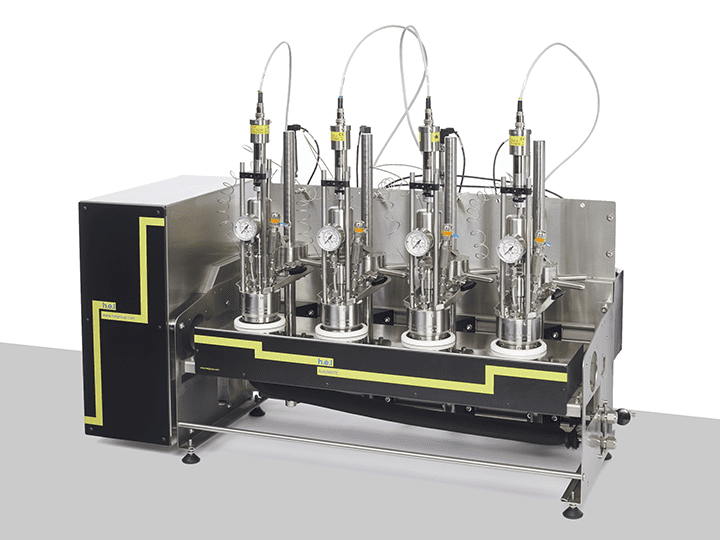
AutoMATE | Linear, Automated Parallel Synthesis Platform
The AutoMATE is a highly versatile, linear, automated parallel synthesis platform, for use...
Scale-Up
Why is the scale-up phase fundamental in process development?
Challenges in the scale-up stage
Scalability for market responsiveness
The primary motivation behind scaling up industrial processes is meeting the market demand for a product. However, the market shows fluctuations, increasing or decreasing the need for the desired product. The scale-up stage allows for considering the demand levels and evaluating the economic feasibility of the process. Developing a scalable strategy allows for agile and resilient responses to these changes, ensuring optimal production levels.
Non-linear scaling implications
Understanding the non-linear nature of specific parameters is crucial. Reactor size changes impact chemical reaction parameters, including kinetics, thermodynamics, and fluid dynamics. The previous stages aimed to identify the optimal conditions for the reaction, but these values often need readjustment. Reagent concentration, temperature, pressure, and stirring needs evaluation. Advanced reactors offer precise capabilities for monitoring and controlling the physical-chemical parameters, aiding in replicating laboratory-scale conditions and enhancing reproducibility in more extensive settings.
Early integration of scalability
Scaling consideration should be implemented in the process development pipeline as early as possible, preferably after the discovery and optimization phases are completed. A proactive approach aids in identifying where the main pitfall could be and addressing potential non-linear scale-up parameters.
Addressing critical questions
This phase can help to understand fundamental questions, such as equipment footprint requirement, allowing for planning early on and avoiding last-minute costly mistakes. Neglecting an appropriate scale-up phase can lead to underestimating plant capacity and suboptimal productivity.
Enhancing producibility and safety
Multi-liter reactors at intermediate scales are valuable for optimization before committing to full industrial scale. Jacketed reactors replicate conditions effectively. Safety concerns can be addressed through accurate data acquisition. Understanding the evaluation of temperature and pressure during the reaction is fundamental and should be closely monitored using accurate data acquisition systems. The results of this phase can help assess the process’s risks and put mitigation measures in place.
In summary, process scale-up is the fundamental bridge between laboratory-sale experiments and large-scale industrial production, aiming to ensure efficient and safe manufacturing. The key challenges are understanding the non-linear aspects of critical parameters, addressing market responsiveness, and integrating scalability early in the development pipeline. Furthermore, this phase enables the assessment of equipment requirements, enhancing reproducibility and safety through precise monitoring, ensuring optimal productivity in industrial settings.
Solutions
Jacketed reactors are a potent tool when aiming for the replication of large-scale processes. They enable efficiency studies of the desired reaction under representative conditions. Reaction rate, yield, and selectivity remain fundamental values to be optimized in this stage.
Closely mimicking the conditions likely to be encountered at the industrial scale, it is possible to improve these parameters. AutoLAB, as a highly configurable automated laboratory reaction system (including high pressures), enables users interested in unlocking the potential of their processes. AutoLAB supports optimizing parameters such as stirring, addition rate, and stirrer design. Operated by H.E.L’s own software, AutoLAB minimizes the likelihood of human error, increasing the reproducibility.
The safety of the process can be evaluated using members of the Process Safety family manufactured by H.E.L, especially Simular, operated as an isothermal calorimeter.
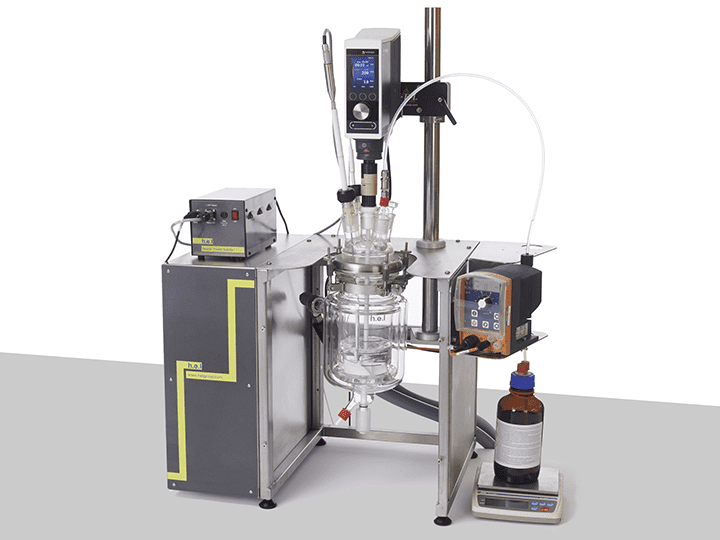
Simular | Process Development Reaction Calorimeter
This highly configurable system from the H.E.L product family excels in optimizing process...
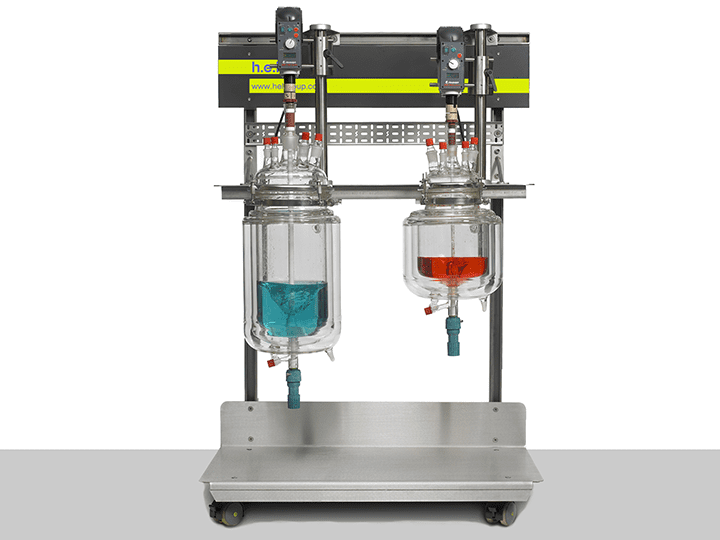
AutoLAB | Bench-Top Automated Reactor System
H.E.L’s fully customizable AutoLAB reactor platforms are designed, configured, and tailo...