A future driven by electric vehicles (EVs) was once the stuff of dreams. Now it’s a reality made possible by technology, talent, and careful testing. Always battery curious, we look at this seismic shift away from the combustion engine with the help of Nigel Taylor. He’s been applying his talent to low-carbon electric vehicles for 30 years, first in the automotive industry for companies such as Jaguar Land Rover and the Rover Group. He currently works as a freelance technical specialist and is the founding director of BatteryDesign.net.
Fit for purpose design
Designing a battery is not an easy task, which increases in complexity as more advanced cells are needed. The process of battery design and optimization requires the close collaboration of specialists in a range of topics: from chemistry to mechanical and electrical engineers. This multidisciplinary group of workers will work in all the different steps of the process: cells, module, and finally, battery. Similarly to chains, a battery will be as strong as its weakest cell.
To design effective and reliable batteries, five critical elements need to be evaluated:
- Electrical: batteries can experience issues such as resistance issues that can cause problems such as electrical arching or shorting.
- Thermal: consistent temperature across the battery is needed for it to work appropriately. Large batteries with s electric vehicle designs are immense. We’ve pulled together a quick run-through of them here, and you can listen to Nigel Taylor explain them in full when he joined our Modern Chemistry podcast.
- Mechanical: Vehicles can crash and be involved in accidents. Batteries need to be designed in a way that physical impacts will not result in them catching fire linked to thermal runaways.
- Safety in design: the risks linked to the use of batteries (overheating, short circuits) need to be addressed when being designed in a way that if things go wrong, users are not going to be put in danger, for example, warning users if things go wrong.
- Control: good understanding of the chemistry of the battery allows for the prediction of the behavior during the life cycle, especially when being pushed to its limits.
The scientific challenges of today’s electric vehicle design are immense. We’ve pulled together a quick run-through of them here, and you can listen to Nigel Taylor explain them in full when he joined our Modern Chemistry podcast.
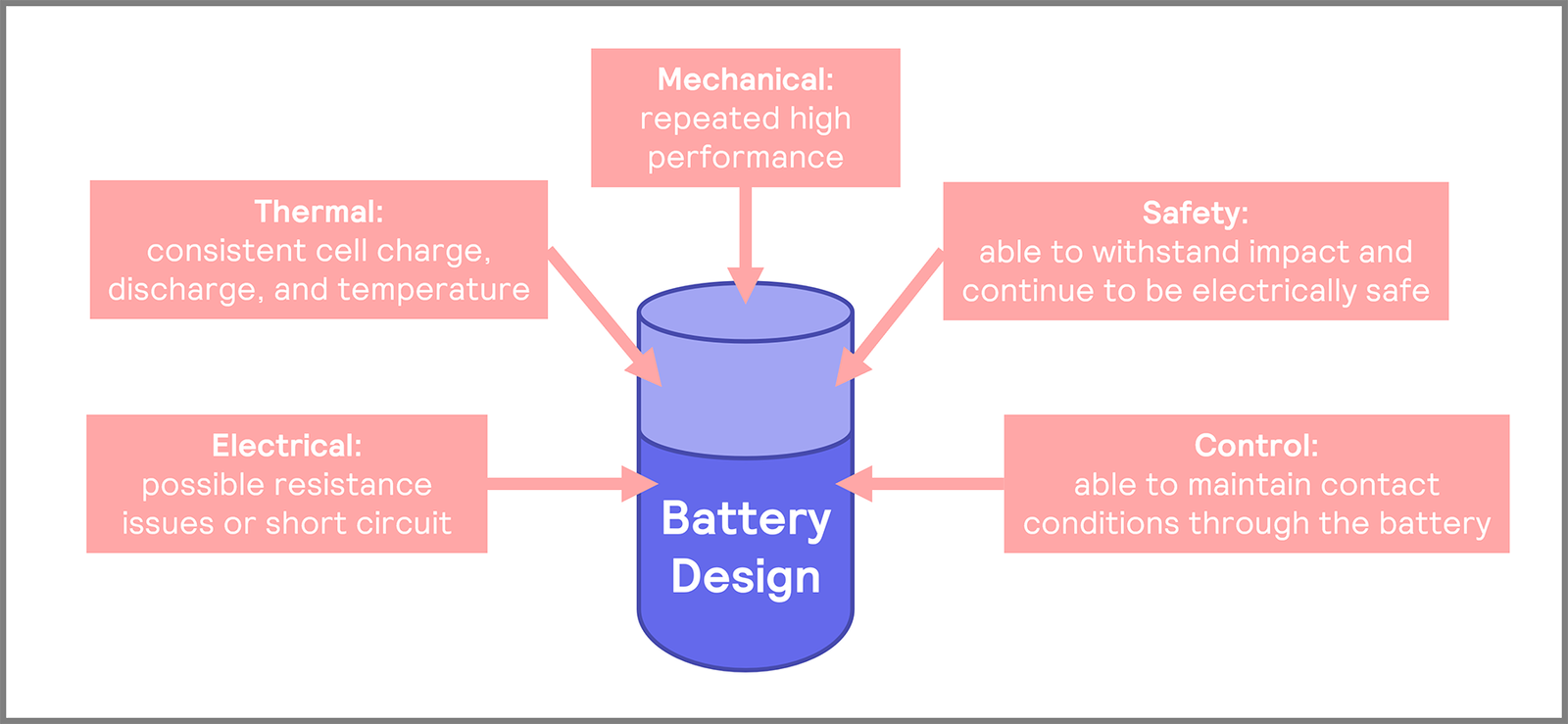
Not all batteries are the same
Don’t be fooled into thinking electric vehicle batteries are just bigger versions of their AA or cell phone power pack cousins. Just think, a cell phone can start to drop recharge performance in around two years, but a big ticket item like a car, one with so few moving parts to go wrong, needs to last far longer. Typically, an electric car will be recharged around 5 to 8 times more than any phone. And, where a phone runs from just one cell, a Tesla car has 6,000 electrically connected cells to power it.
Phones stay with us and typically go indoors when it’s cold, so they are exposed to a broad but not extreme range of temperatures. However, an electric car left outside needs a rechargeable battery able to effectively discharge at anywhere between -20°C to +60°C. It was concerns like this that the initial slow uptake of electric vehicles, and in response, manufacturers now offer extended warranty periods. A move that’s also eased the minds of the second-hand car market. Now, an owner can expect a car’s lifespan to be around 10-15 years and/or 150,000+ miles.
The speed a car battery discharges power is also very different from a cell phone. A cell phone in constant use will discharge in around 10 hours, with a C rate of over 10. Whereas steady motorway driving discharges a car battery in around two hours. Put that car on a racetrack, and it’ll be gone in 20 minutes. This is a C rate of two, and designing a battery to achieve that takes very careful management.
The problems with power
A high-end car can deliver between 150 and 225 kW. So, let’s assume that to match up this value, an EV would need over 200 kilowatts (kW). A single electric lithium cell can produce 3.6V, 4.2V at its peak. Having 100 cells, where each negative pole of the cells will connect to the positive pole of the next one, in the battery would push the voltage to 360-420V. The calculation of power from current and voltage is straightforward:
Power(kWh) = Current(Amp) x Voltage(V) / 1000
In terms of energy, normal batteries have 5Amp, which would mean: 360V x 5Amp = 1.8kWh. That value would be enough just to travel 10km. One solution would be to connect the cells in parallel instead, so positive pole to positive pole and negative pole to negative pole. Having 60 series of 100 cells sequences would ramp up the power 60 times theoretically. 300Amp block of cells with 360V, which means that the capacity of the battery would be 108 kWh. With the engine revved up and ready to go, it’s maintaining that power that’s the next hurdle to overcome. All the 6,000 cells in this EV must function as one: with unified resistance and temperature levels. Any large temperature differences pull in high currents and affect how the cells discharge. The industry’s desire to double what’s currently typical to run the packs at 800V only compounds the risk and difficulty. It would only take just one of the cells to malfunction and produce a conductive gas for there to be arcing across the pack’s 6,000 cells.
Capping off the heat
With that in mind, keeping things cool is equally hard to achieve. Even relatively small batteries are designed with a cooling infrastructure or release included. But EVs have to manage their heat loss in a minimum 400V setting. In an ideal scenario, a cooling system that is electrically insulated but thermally connected would be the objective. Having an electrically conducting cooling system could result in short circuit events, and in the case, it was a fluid, processes of electrolysis may happen. To solve the problem, the coolant is housed in structures similar to what could be seen at the back of all refrigerators. The cooling packs would consist of an external coating that is electrically insulating and a thermally conducting layer between the battery and the cooling plate. The current solution is to have a very thin structure composed of silicate-based coating with a graphite interlayer. These important keep the cell connected, maintaining the series, but leave it electrically isolated to be able to lose heat. This is a highly inventive solution for when it’s essential that any cell stays within two degrees Celsius of the rest.
A big risk when maintaining a healthy thermal condition in the battery of an EV is ensuring that the cooling mechanism is kept in place. However smooth the drive, an EV will vibrate, causing cooling packs to dislodge. Get uneven temperatures across the cells, and they age inconsistently. That’s a major issue, as the whole cell pack is only as good as its worst part. If one cell of the 6,000 were to weaken, the energy of all the other cells can’t be exploited. And, as most EV battery packs at the moment are unreplaceable and intended to last the lifetime of the car, premature aging gives much cause for concern.
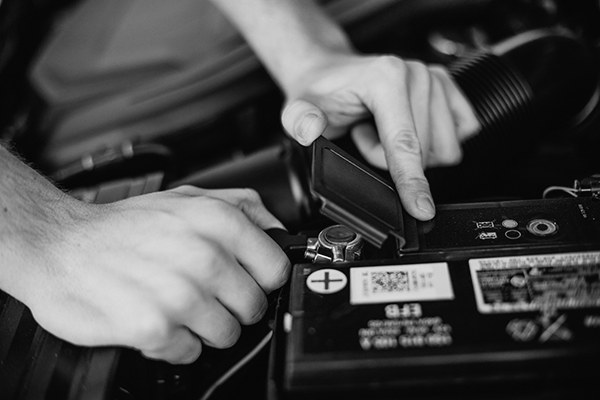
EV wins to date
With all that said, it’s time to have more confidence in the safety of EV cars, says Nigel. “We don’t worry about the battery in our remote control, so need not worry about the safety of the battery in a car. Trace elements, like niobium, are being put into some cells to make them more robust, and the latest battery packs in Formula E are making a step change in energy density too. [The cars will] feel like early 1970s Formula One in terms of performance. That [should] boost consumer confidence in the lifespan of electric cars to the point that they [become] the norm.”
As a whole, he feels the journey of EVs into the mainstream has gone well. With recent technology uplifts, it’s now possible to monitor battery health via a phone app. Plus, access to quality data has already put some pack control system management into the cloud, where battery performance is tailored to individual usage or optimum experience, whatever the driving conditions.
And, looking to the future?
There’s much chatter about the possible reuse of EV batteries. This may help a once throw-away obsessed society feel better but will only prove possible in cars if shown to be commercially viable. Currently, the costs to disassemble a pack and ensure its safe reconfiguration are just too high. And there are concerns about the validity of even carrying out the process on packs that have already had a hard-working life.
If pack reuse within cars isn’t a viable option, the possibility of vehicle-to-grid innovations could be. So too, could be using repurposed batteries in the home, charged by solar panels during the day to power the home at night. Other thinking is looking to put repurposed batteries together to create multi-car, fast-charging points that could protect the grid from brownouts and boost local communities.
EV cars may be passed their infancy but still have plenty of growing up to do. We could be looking to an awkward adolescence bringing with it important benefits to motorists and the planet. What’s for sure is that there’s plenty of change to come.