Why is Process Safety Important?
From synthesizing a new API to developing a novel polymer, chemical reactions and the products they form are front and center in the world in which we live. One of the biggest challenges facing those trying to bring these products to market is scale-up: taking small, lab-based synthesis through pilot plant to full-scale manufacture.
It is well-recognized that there are numerous safety risks involved in scaling up chemical processes. Central to these are the changes in heat-loss behavior, which differ with scale:
- Many reactions are exothermic. Due to the small scale, this heat can quickly dissipate to the surrounding environment in a lab-based environment. However, the reaction may require additional active temperature management on scale-up to ensure safe reaction conditions.
- Components in the reaction may become unstable under certain operating conditions, including storing large volumes, which can cause additional hazards that require management.
The risks associated with scale-up have potentially hazardous, even fatal, consequences if not addressed. Thus, thermal and pressure hazards must be considered, identified, assessed, and mitigated at each stage of product development. To achieve these objectives, a number of questions need to be answered, which will depend on the step of the scale-up process (Figure 1). By designing safety into the product development from the earliest stages – a Safety by Design, if you like – one can feel confident that the hazards associated with scale-up to manufacturing can be successfully addressed.
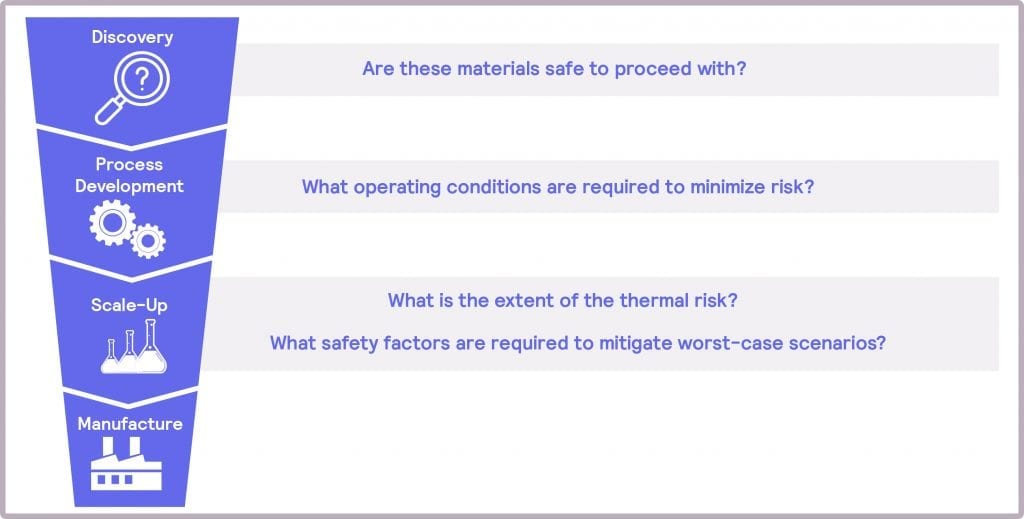
How to apply Process Safety into the Development Workflow?
Applying a safety-by-design approach within the development workflow has safety and cost benefits.
- Broadly speaking, process safety scale-up follows four main stages:
- Screening for potential hazards
- Evaluation of the main reactions, including possible unintended side reactions
- Evaluation of “what if” worst case scenarios and subsequently implementing mitigation and control strategies.
These steps naturally map onto the product development funnel. At the top of the funnel, the tests need to be simple and quick to address the number of samples. At this stage, the information provided can be quite limited. At the bottom of the funnel, poor candidates have been eliminated from consideration, and more information is required. Tests at this stage will be longer, and the experimental complexity will be greater than in discovery.
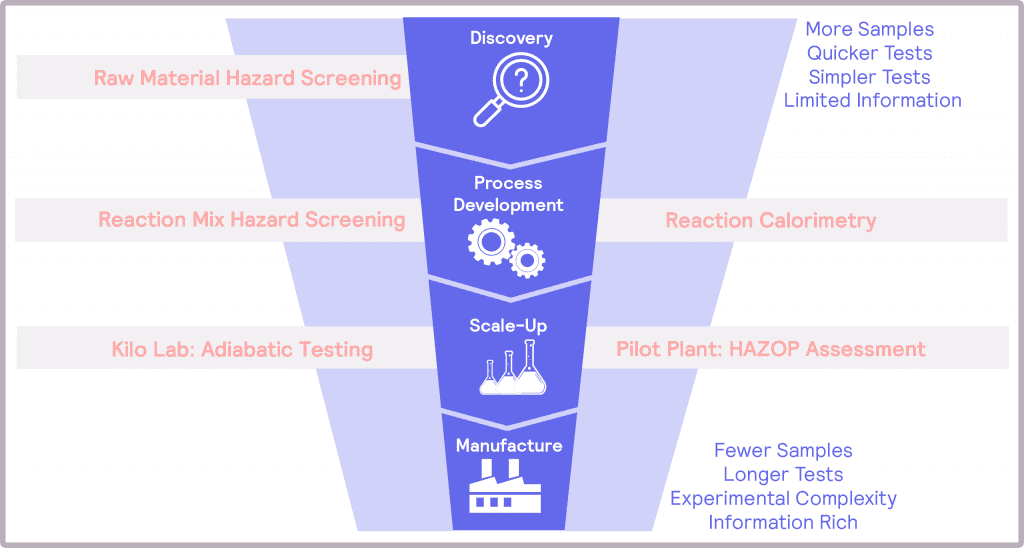
At the process development stage, the target molecule has been identified, and its synthetic route has been determined. The work at this stage is to develop and optimize the process with a view to manufacturing at scale. In terms of safety, the desired main reaction needs to be assessed and understood, alongside identifying potential additional thermal and pressure hazards as a result of the operating conditions. An example of these hazards could be undesired side products that are more unstable than the desired product.
During scale-up, the different operating conditions are evaluated to assess their impact on the hazards. This information is used to optimize the conditions for safety. Finally, with the operating conditions optimized and the potential hazards identified, it is time to assess the magnitude of these hazards prior to full scale-up.
H.E.L’s Process Safety Solutions
Consideration of process safety throughout the product development pipeline from discovery to scale-up is essential to ensure the safe scale-up of chemical processes.
In Process Development, it is vital to understand how hazardous the selected synthesis reaction is and whether the plant cooling capacity is sufficient to mitigate these potential hazards. Hazard screening and reaction calorimetry both have a role to play when understanding a reaction itself. The move to scale-up is characterized by an increasing focus on the true extent of identified hazards, so plant safety design can be optimized accordingly. Adiabatic testing and HAZOP (hazard and operability) assessments come to the fore here. These considerations are summarized in the product development funnel in Figure 3.
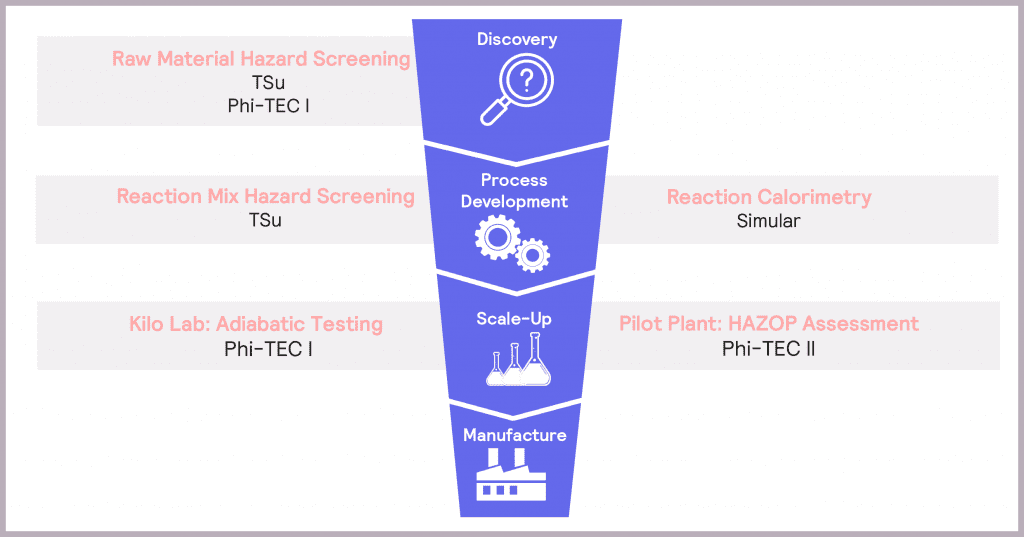
Making safety an integral component of product development – by using a variety of tools to identify, assess and then mitigate the potential hazards at each stage of the process – ensures confidence in delivering a successful and efficient route to market.
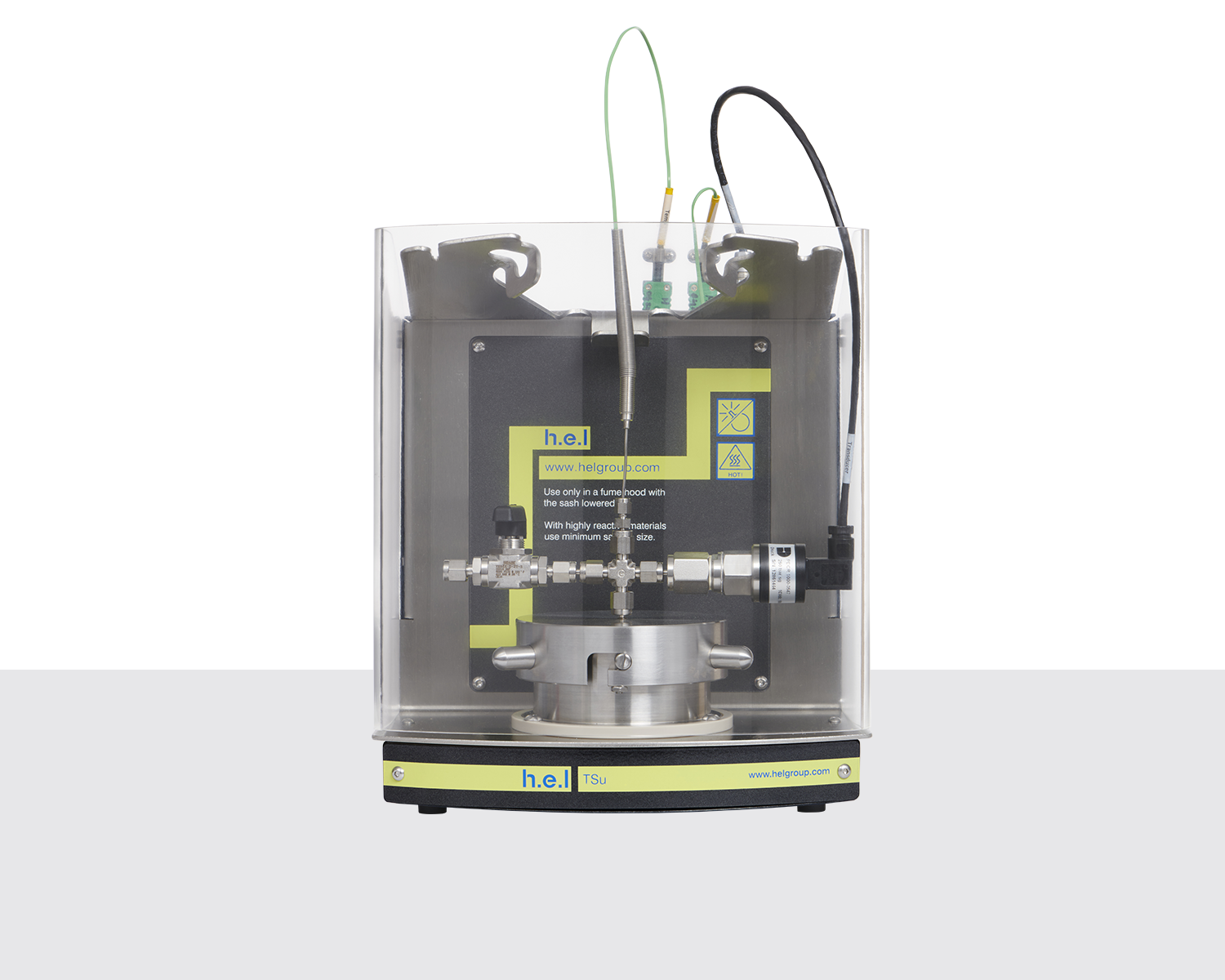
TSu | Thermal and Pressure Hazard Screening Platform
The fast screening of thermal and pressure hazards can be performed with the Thermal Scree...
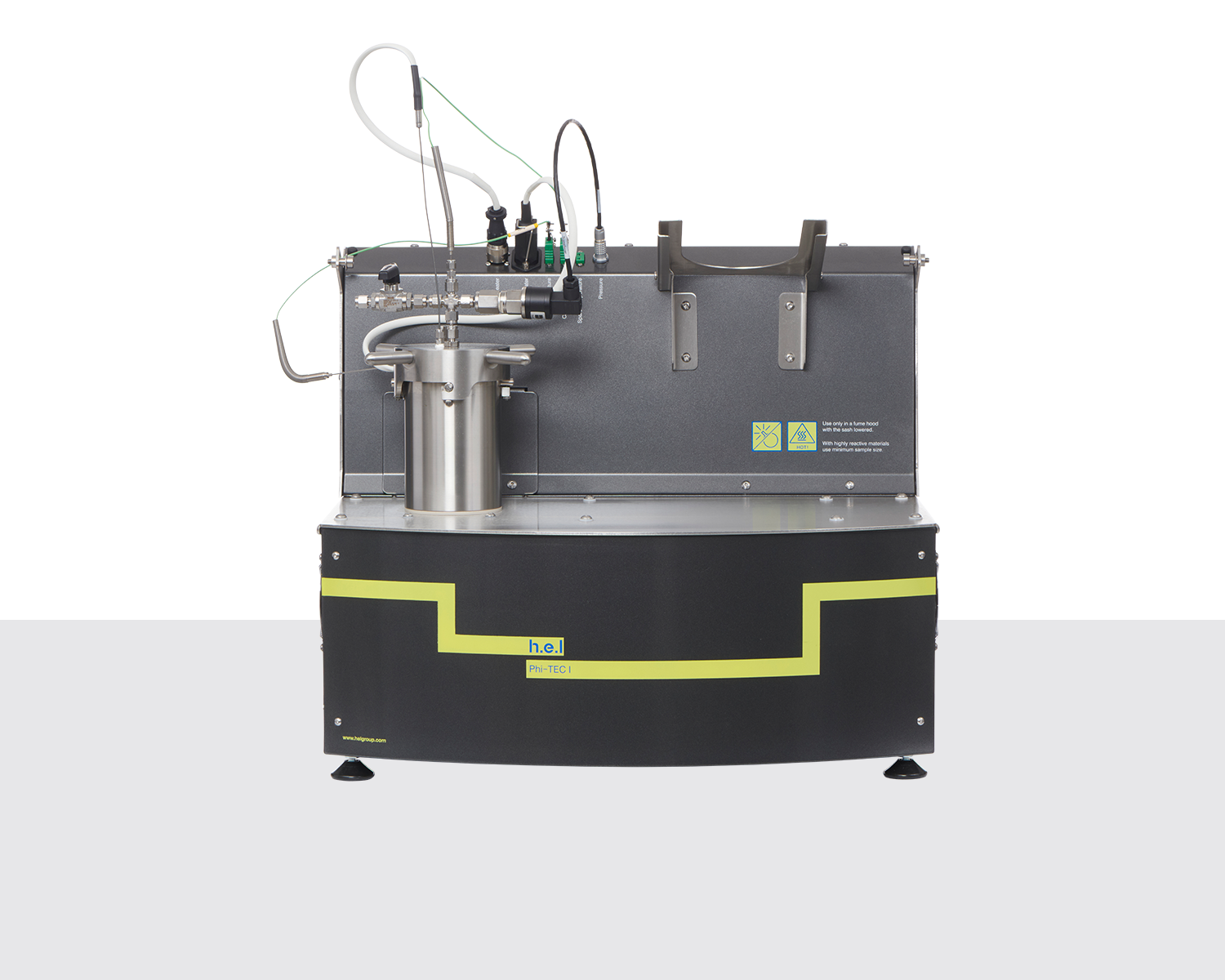
Phi-TEC I | Bench-top, adiabatic calorimeter
The Phi-TEC I is an adiabatic calorimeter that enables the characterization of thermal run...
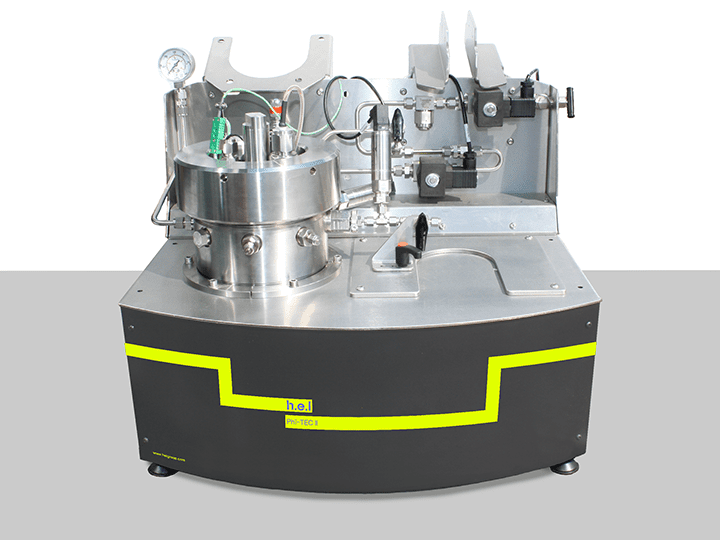
Phi-TEC II | Bench-top, low phi-factor, adiabatic calorimeter
The Phi-TEC II is an adiabatic calorimeter, which supports the use of low Phi-factor test ...
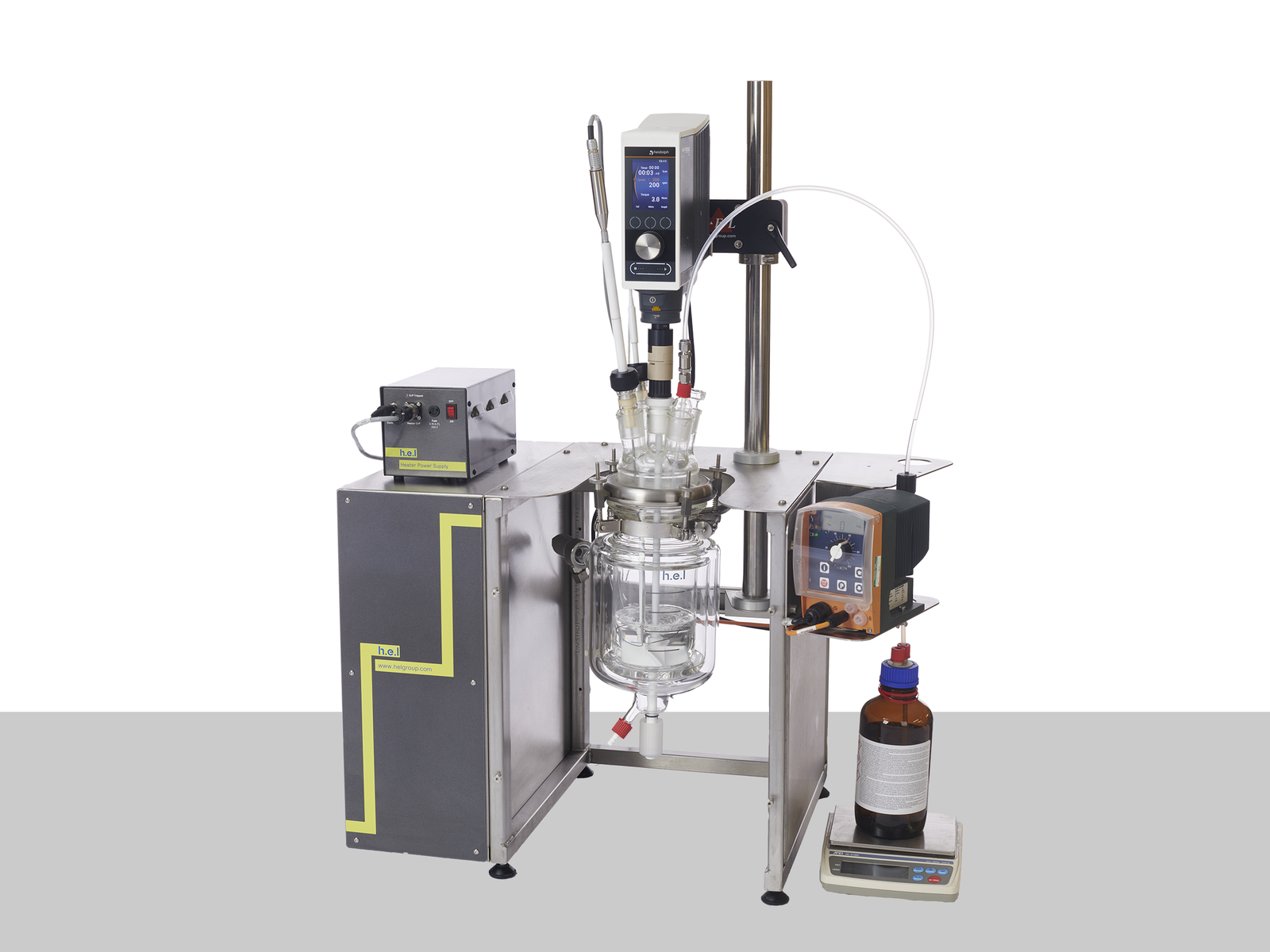
Simular | Process Development Reaction Calorimeter
This highly configurable system from the H.E.L product family excels in optimizing process...