Process Development
What parameters need optimization in the Process Development phase?
Precise temperature regulation
Temperature is one of the physical parameters that impact chemical reactions the most. On the one hand, higher temperatures increase the speed at which molecules vibrate and are transported in the solvent. However, there is a second factor to consider with temperature. For the chemical reaction to occur, the energy of the reaction needs to be higher than the activation energy (Ea).
The Arrhenius equation reflects the relation between the temperature, activation energy, and temperature:
K = rate constant
A = pre-exponential factor
Ea = activation energy
R = universal gas constant
T = absolute temperature
As a result, temperature variation can significantly impact reaction kinetics, product quality, and yield. Employing advanced heating and cooling systems (e.g. temperature-controlled reactions and circulators), temperatures can be maintained within the optimal range throughout the process.
Effective Mixing
One of the first steps in the chemical reaction is the physical contact between the different reagents involved. Diffusion is the process where molecules move following chemical gradients. However, this process is slow. In the absence of stirring, pockets where molecules accumulate occur, reducing the reactivity. Efficient agitation is, therefore, fundamental, and optimization of parameters, such as speed and agitation mechanisms, promote efficient mass transfer and reaction homogeneity.
Comprehensive data recording
In the process development phase, acquiring in-depth knowledge about the chemical reactions and any secondary reactions that might occur is paramount. To achieve this, it is fundamental that robust data is recorded, processed, and analyzed. Closely monitoring critical parameters, including temperature, pH, pressure, reactants, and product concentration, results in robust data acquisition. Real-time analysis tools enable immediate adjustments and informed decision-making.
Reproducibility and standardization are intertwined with the acquisition of high-quality data. Repetition of the same protocol over time ensures that the data obtained is not an anomaly, allowing the prediction of the outcome of the process and understanding of potential risks and hazards. Accurate and representative documentation of each step, including reaction conditions, reagent sources, and equipment calibration, ensures a process that can be consistently replicated.
Safety
Process safety should always be a high priority when developing novel processes. A thorough risk assessment should be performed to identify potential hazards linked to reactants, intermediates, and reaction conditions. This includes the analysis of the compatibility of the reagents used in the process and their store conditions. Safety measures should be implemented, including containment systems, pressure relief mechanisms, and emergency shutdown procedures.
The process development phase combines precision, optimization, knowledge acquisition, and safety consciousness. The meticulous control of parameters such as temperature, recognizing its significant impact on reaction kinetics, is critical. Adequate mixing ensures efficient mass transport, resulting in the homogeneity of the reaction. Comprehensive data recording and analysis are the keystone of informed decision-making, yielding standardized protocol ensuring the reproducibility of the process. Last but most definitely not least, safety consideration through thorough risk assessment and the implementation of safety strategies must never be overlooked. These considerations represent the foundation for effective and successful Process Development.
Solutions
H.E.L PolyBLOCK 4, PolyBLOCK 8, and AutoMATE are designed to reduce the time spent in the process optimization phase. Their capabilities to run different tests in parallel under strictly regulated conditions enables meaningful and reproducible outcomes. The possibility of using over-head stirring can help to ensure homogeneity in the reactor and mimic manufacturing. Additionally, H.E.L’s own software allows for real-time measurements and strict control of the conditions of the experiment, providing optimal conditions while maintaining strict safe conditions.
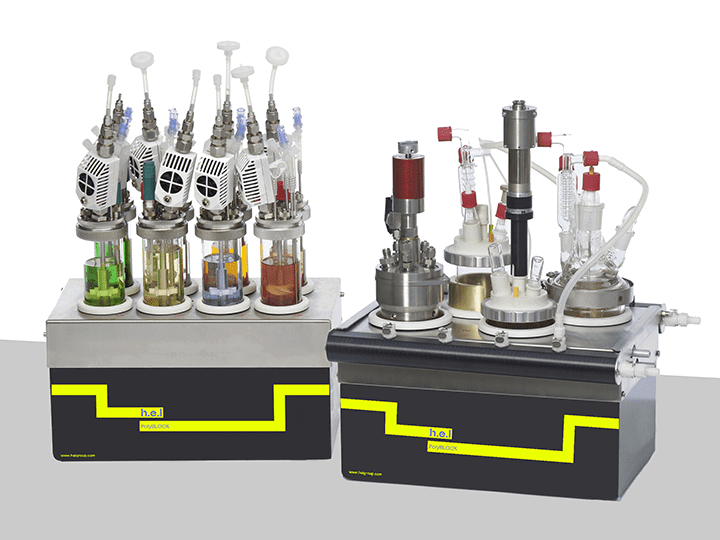
PolyBLOCK | Compact Automated Parallel Synthesis Platform
Key Features 4 or 8 Independent reaction zones Independent temperature control (100 °...
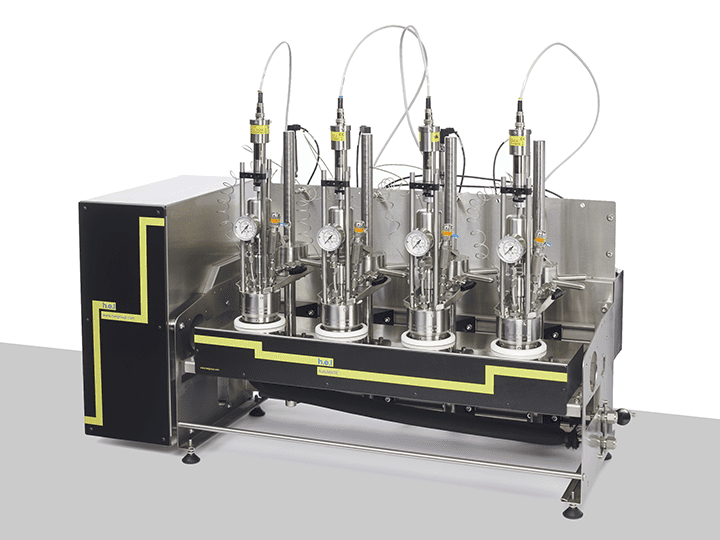
AutoMATE | Linear, Automated Parallel Synthesis Platform
The AutoMATE is a highly versatile, linear, automated parallel synthesis platform, for use...