Discovery
How can we improve the discovery of novel products?
Productivity
Due to its iterative nature, the discovery phase sometimes takes a long time, in which each one of the different parameters needs to be evaluated. Often, finding the optimal for the process requires slightly modifying the conditions of the experiment. There are specific ways in which the productivity of this phase can be improved.
The ability to run separate reactions individually allows for the testing of different conditions simultaneously and enables the testing of different parameters in the search for optimal conditions. These parameters can include physical parameters – e.g. temperature, agitation, pressure – or chemical – e.g. pH, ionic concentrations, and different reagents. On the other hand, repetition and replicability are intrinsic to science. Having multi-reactor systems enables experiment replication, diminishing potential variability within the tests and increasing the statistical robustness of the data.
Space
The space that instrumentation occupies can be detrimental to the productivity of laboratories and industrial processes, especially when there is space limitation. The miniaturization of vessels reduces the amount of reagents and materials required for each reaction, optimizing space and reducing waste without losing the control capabilities of larger systems. Additionally, multi-reactor systems can be operated using a single computer instead of having one per, further reducing the amount of space required.
Safety
In the discovery phase, different conditions must be tested to find the ideal conditions for the reaction. The product yield and the reduction of costs to run the process are fundamental parameters in finding the perfect process. However, safety cannot be ignored.
In order to design safer processes, different conditions need to be tested. For example, other reagents can produce the same product. It could also be that byproducts can be hazardous (e.g. toxic, or gases that can accumulate, increasing the pressure to dangerous levels). Testing different reagents is costly and time-consuming, but multi-reactor approaches can significantly reduce the time this stage takes.
Heat accumulation can be an issue at the industrial scale when the heat does not dissipate at a high enough rate. In this case, testing for different conditions, such as semi-batch fed systems, can help to mitigate issues. Adiabatic calorimetry is a powerful tool to test the safety of chemical processes. An in-depth characterization of the process can help detect potential exotherms – the temperature at which the heat produced by the reaction becomes high enough to accelerate the reaction, entering a potentially dangerous positive feedback loop. Adiabatic calorimetry can help determine crucial safety parameters like the maximum temperature of the synthesis reaction or the time to maximum rate.
In conclusion, the discovery phase is a meticulous and iterative process that relies on hypothesis testing through controlled experiments. To enhance productivity at this stage, multi-reactors operating individually can evaluate diverse conditions simultaneously, ensuring data robustness through replication. Miniaturization of reactor systems can also help reduce the spaces taken by instrumentation, allowing for smaller volumes and consequently reducing reagent consumption and waste generation. Optimization should always include a safety evaluation of the process and the reduction of potentially hazardous conditions, such as the production of dangerous byproducts and heat accumulation.
Solutions
H.E.L’s PolyBLOCK and AutoMATE are designed as individually controlled reactors, enabling the simultaneous analysis of different synthetic routes and identifying the optimal conditions. Parameters such as conversion efficiency, economic viability, and challenges in the scale-up process can be identified using these solutions. Additionally, the compact design of these platforms reduces the space required for the testing. The flexible nature of these systems and the strict control using H.E.L’s own software help increase the efficiency of the discovery phase. Simular operates as an isothermal calorimeter, enabling in-depth characterization of the thermodynamics and kinetics of the reactions. This allows for the detection of potential hazardous reactions, increasing the safety of the process.
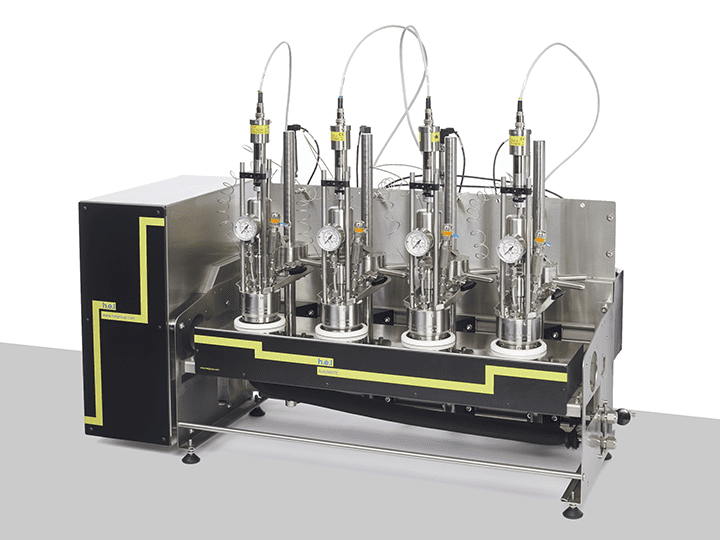
AutoMATE | Linear, Automated Parallel Synthesis Platform
The AutoMATE is a highly versatile, linear, automated parallel synthesis platform, for use...
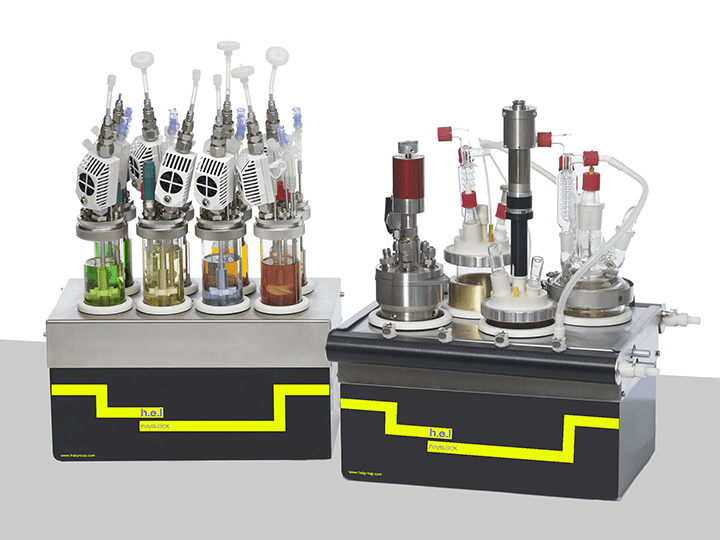
PolyBLOCK | Compact Automated Parallel Synthesis Platform
Key Features – 4 or 8 Independent reaction zones –Independent temperature control (1...
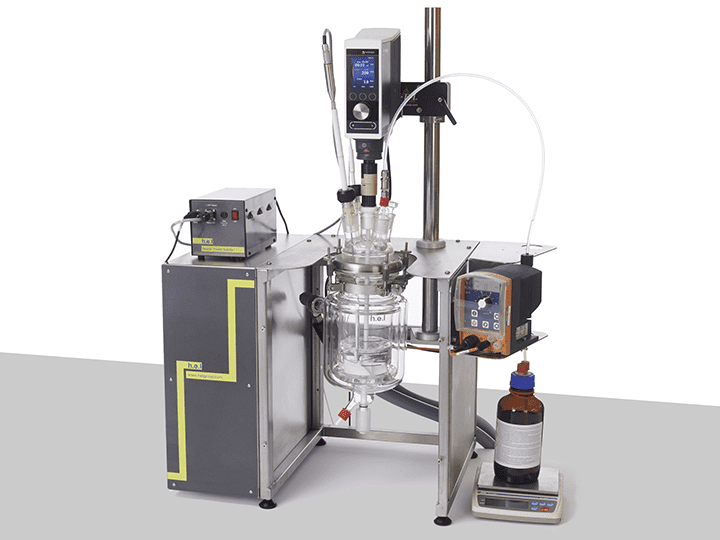
Simular | Process Development Reaction Calorimeter
This highly configurable system from the H.E.L product family excels in optimizing process...