Scale-Up
What issues arise during scale-up?
The scale-up process often faces challenges rooted in mixing and resultant complications, such as heat transfer, among others. As production moves from bench top towards industrial scale, the homogeneity achieved through mixing becomes more challenging to maintain. This can lead to uneven temperature and solute concentration distribution, which can be detrimental to the nucleation and crystal growth phases. This variability can result in non-uniform particle size distribution and shape anomalies, compromising quality and yield. The change in scale also typically affects heat transfer efficiency, as large volumes add an extra layer of difficulty for how the heat needs to be distributed or removed, complicating the maintenance of the precise temperature required for optimal crystallization.
Other factors impacted by scale-up include fluid dynamics and suspension behavior. This can affect, for example, the frequency at which fresh superheated solution is delivered to critical zones. This can drastically affect the supersaturation levels. These changes require meticulous testing to recalibrate these factors and be able to replicate the conditions achieved on smaller scales. Without careful adjustment and optimization of these factors, scale-up efforts can lead to increased production costs, extended development times, and even failure to meet regulatory and quality standards, posing substantial risks to commercial viability.
What challenges are encountered at a large scale?
In scaling up crystallization to commercial production, the push to maximize efficiency and reduce costs often can lead to variability that can significantly affect the quality and safety of the final product. Large-scale operations may struggle to maintain the precise and controlled conditions required to obtain optimal products, resulting in variations in the physical properties of the crystals. Such alterations not only impact the effectiveness of the products but also result in safety risks – especially when dealing with hazardous or explosive substances 6.
Companies must address these challenges by performing accurate and realistic risk assessments, utilizing robust quality systems, and using advanced monitoring techniques. This proactive approach helps to maintain consistency across batches without compromising health and safety. It is fundamental that the reactors and crystallizers are manufactured with durable and appropriate materials, mitigating the introduction of impurities and preventing equipment degradation. By integrating these strategies, manufacturers can safeguard both the integrity of their products and the health and safety of their operations, ensuring they meet both commercial demands and regulatory standards.
Solutions
In scaling up crystallization to commercial production, the push to maximize efficiency and reduce costs often can lead to variability that can significantly affect the quality and safety of the final product. Large-scale operations may struggle to maintain the precise and controlled conditions required to obtain optimal products, resulting in variations in the physical properties of the crystals. Such alterations not only impact the effectiveness of the products but also result in safety risks – especially when dealing with hazardous or explosive substances 6.
Companies must address these challenges by performing accurate and realistic risk assessments, utilizing robust quality systems, and using advanced monitoring techniques. This proactive approach helps to maintain consistency across batches without compromising health and safety. It is fundamental that the reactors and crystallizers are manufactured with durable and appropriate materials, mitigating the introduction of impurities and preventing equipment degradation. By integrating these strategies, manufacturers can safeguard both the integrity of their products and the health and safety of their operations, ensuring they meet both commercial demands and regulatory standards.
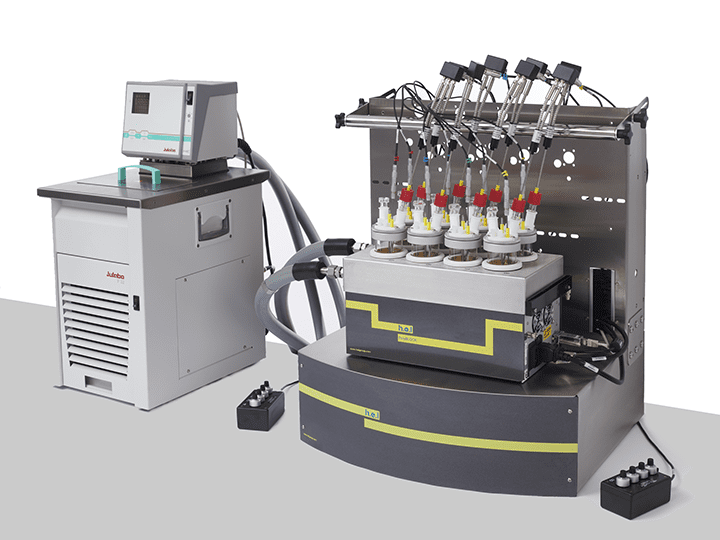
CrystalSCAN | Parallel Crystallization Monitoring Platform
The CrystalSCAN is a bench-top, automated, parallel crystallization monitoring platform, f...