Scale-Up
What challenges are encountered at a large scale?
In scaling up crystallization to commercial production, the push to maximize efficiency and reduce costs often can lead to variability that can significantly affect the quality and safety of the final product. Large-scale operations may struggle to maintain the precise and controlled conditions required to obtain optimal products, resulting in variations in the physical properties of the crystals. Such alterations not only impact the effectiveness of the products but also result in safety risks – especially when dealing with hazardous or explosive substances 6.
Companies must address these challenges by performing accurate and realistic risk assessments, utilizing robust quality systems, and using advanced monitoring techniques. This proactive approach helps to maintain consistency across batches without compromising health and safety. It is fundamental that the reactors and crystallizers are manufactured with durable and appropriate materials, mitigating the introduction of impurities and preventing equipment degradation. By integrating these strategies, manufacturers can safeguard both the integrity of their products and the health and safety of their operations, ensuring they meet both commercial demands and regulatory standards.
Solutions
In scaling up crystallization to commercial production, the push to maximize efficiency and reduce costs often can lead to variability that can significantly affect the quality and safety of the final product. Large-scale operations may struggle to maintain the precise and controlled conditions required to obtain optimal products, resulting in variations in the physical properties of the crystals. Such alterations not only impact the effectiveness of the products but also result in safety risks – especially when dealing with hazardous or explosive substances 6.
Companies must address these challenges by performing accurate and realistic risk assessments, utilizing robust quality systems, and using advanced monitoring techniques. This proactive approach helps to maintain consistency across batches without compromising health and safety. It is fundamental that the reactors and crystallizers are manufactured with durable and appropriate materials, mitigating the introduction of impurities and preventing equipment degradation. By integrating these strategies, manufacturers can safeguard both the integrity of their products and the health and safety of their operations, ensuring they meet both commercial demands and regulatory standards.
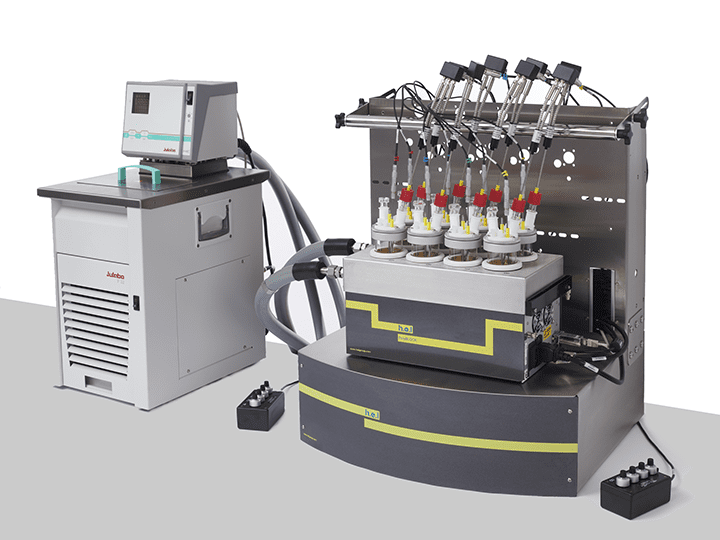
CrystalSCAN | Parallel Crystallization Monitoring Platform
The CrystalSCAN is a bench-top, automated, parallel crystallization monitoring platform, f...