What kind of catalysts are there?
- Homogeneous catalysts: These catalysts share the same phase as the reactants, promoting enhanced interaction and reactivity under mild conditions.
- Heterogeneous catalysts: Operating in a different phase than the reactants, these catalysts are prevalent in industry due to their ease of product separation and catalyst recovery.
- Biocatalysts: Certain biological molecules, such as enzymes or nucleic acids, can accelerate biochemical reactions.
How do catalysts provide a secondary pathway?
The interaction between the catalyst and the reactant molecules results in the formation of an intermediary known as an activated complex, also known as a transition state. While chemical bonds form within this complex, they require less energy to break, thus enhancing the likelihood of the reaction occurring. Once the catalyzed reactions have occurred, the products detach from the catalyst, regenerating it for further use in accelerating subsequent reactions.
Discovery
What characteristics are tested in the screening phase?
Screening is an essential component in the process of novel substances of interest. Recyclability, or the capacity to recover the molecule of interest once the reaction has finished, is fundamental. The products of the reactions are detached or desorbed from the catalyst, and it is ready for subsequent processes. This is linked to the second characteristic of interest: stability. Ideally, our chemical of interest would be able to maintain its capabilities to accelerate the chemical reactions at the same level as long as possible during its active life, regardless of the number of times it has been regenerated.
Last but not least, it is fundamental that the catalysts are selective, which means they will overwhelmingly catalyze the reaction, avoiding side reactions and by-products as much as possible. Ultimately, catalysis aims to increase the quality of the chemical reaction, increasing the yield and efficiency. These are both related to the amount of the final product. Whereas the efficiency indicates the amount of reactant necessary to generate a unit of product, the yield also accounts for other variables such as time.
What are the potential challenges in hydrogenation and catalysis processes?
Optimizing chemical reactions, especially those involving hydrogenation and catalysis, requires addressing various physical and chemical factors. Challenges such as maintaining ideal catalyst conditions, preventing hazardous situations, and managing catalyst deactivation and by-product formation must be carefully considered and addressed.
Additionally, extra challenges need to be addressed because of the nature of catalysis. These include the ideal conditions for catalysts. For example, in the case of homogeneous catalysis, the physical conditions need to be such that all the reactants remain in the same physical state, avoiding precipitation processes.
What key features should considered in catalysis and hydrogenation studies?
The discovery phase is a long phase in which different catalysis, substrates, and products must be tested. Parallelization can increase the throughput of this process, enabling researchers to test different substances under the same conditions to identify potential candidates. Alternatively, the same candidate reaction can be tested under different conditions, decreasing the number of tests needed. High-resolution techniques and automation are crucial in characterizing reaction kinetics efficiently, enabling accurate and timely data collection while minimizing human error.
Solutions
H.E.L provides highly customizable and flexible instruments designed for catalyst screening and hydrogenation. Parallel systems offer increased throughput, decreasing the time required to optimize processes. Manual screening can be performed using the CAT range, allowing for up to 7, 18, or 24 individual reactors of different volumes. For higher throughput screening, the DigiCAT 96 allows for up to 96 individual tests using a 96-well Zinsser block, ideal for early catalyst development. The ChemSCAN is a fully automated benchtop catalyst screening platform with four reactors with varied volumes. This allows the ChemSCAN for each reactor to operate independently or in parallel, reducing testing times.
High-pressure is particularly interesting for gaseous reactions (such as hydrogenation) as it favors the solubility of gases in liquid phases. H.E.L’s PolyCAT (4 and 8) are benchtop, automated screening platforms specifically designed for this type of reaction. Additionally, using different reactor volumes (from 16 to 500 ml) can help reduce costs associated with using resources.
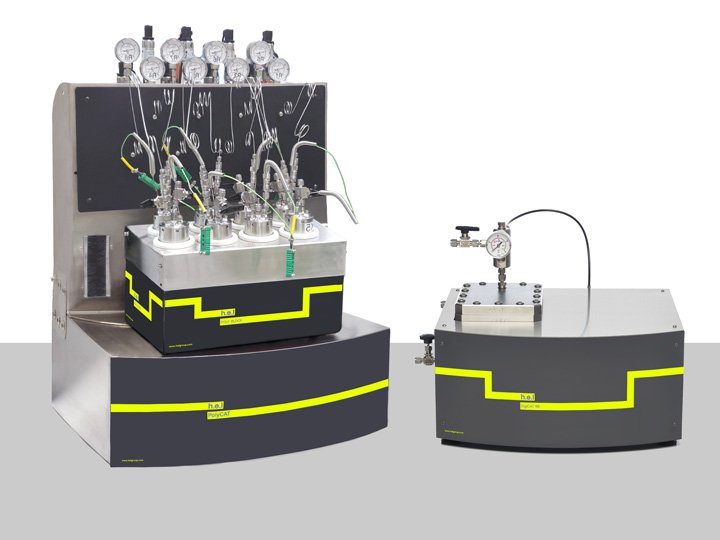
Catalyst Screening Platforms | Manual Systems
Our complete range of multi-sample high throughput catalyst screening vessels has been des...
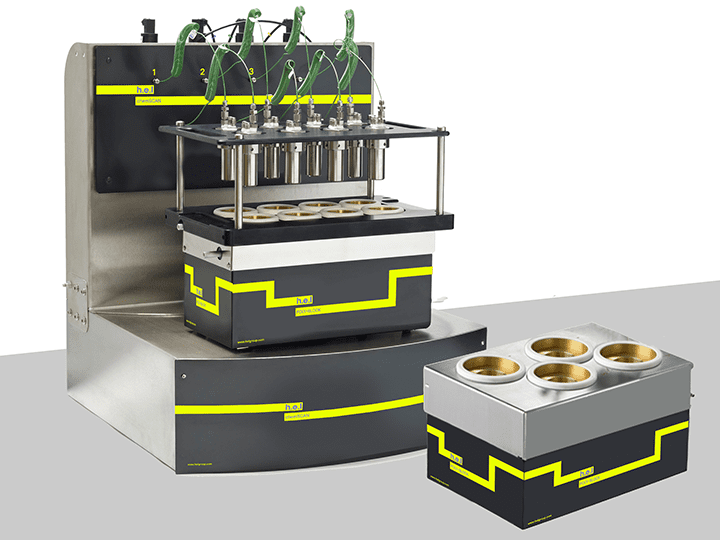
ChemSCAN | Parallel Catalyst Screening and Development Platform
ChemSCAN brings efficiency and flexibility to catalytic research by enabling up to 8 high-...
Process Development
What are the optimal conditions?
Chemical reactions, regardless of the presence of catalysts, are constrained by several physical and chemical parameters. This phase aims to identify the range of values at which the chemical reaction has the highest yield and/or productivity. Still, in the case of catalysts, it also aims to determine the conditions under which the catalyst’s life is the longest.
In the previous section, we mentioned that catalysts can undergo processes that undermine their capabilities. For example, catalysts can experience poisoning, fouling, structural degradation, or leaching processes. In the Process Development phase, these potential undesirable effects need to be identified, and ways to mitigate them must be found. Depending on the type of substance used to accelerate the chemical reaction, these strategies can take different forms:
- Catalyst coating and active site stabilization: some of the catalyst’s active sites can be susceptible to reacting with other molecules, resulting in irreversible chemical bonds. This reduces the effectivity of the catalysts. Chemical modification of the surface of the catalysts can prevent non-specific reactions by limiting the access of molecules to the active sites and preventing this process.
- Development of regeneration methods: although one of the characteristics of the catalysts is the recovery of the molecule after the reaction, the reality is that over time, they become less and less effective. Certain processes need to be developed for them to become fully active again. The regeneration reaction will depend on the chemical nature of the catalysts and the modification they have suffered during their active life.
- Conditioning of the reagents: in many cases, especially in industrial settings, the source material for the reaction is of low purity. The result of this can be the occurrence of side reactions with unpredictable side effects (e.g., fouling and poisoning). Pretreatment of these materials can prove highly effective, reducing potential reduction in the catalyst activity.
How can processes be optimized?
The basic parameters in which the chemical reaction operates are defined during the process discovery phase. However, during the process development phase, these values are modified to study their impact on the productivity and efficiency of the reactions. Temperature provides kinetic energy to the atoms, favoring the re-arrangement of chemical bonds. On the other hand, specific catalysts can be susceptible at high temperatures (primarily biological), and as a result, they can undergo denaturation processes that render them useless. High pressure displaces the gas-liquid equilibrium towards the liquid phase, increasing the gas solubility and yield.
Stirring is a fundamental parameter required when liquid phases are involved in the reaction. Ensuring homogenous conditions is vital, preventing the formation of high-concentration pockets of reagents or products, which can result in precipitation.
What is the environmental impact of the process?
Evaluating the ecological effects of chemical processes has become the norm. More and more governmental bodies are putting in place guidelines to ensure that processes are as environmentally friendly as possible. The use of catalysts results in processes less prone to generating by-products. Nevertheless, this does not mean that side reactions can occur, and some of these products can be potentially polluting. It is for that that extensive characterization of the process is required at this stage. There are many variables to evaluate at this point; it is fundamental to understand the accumulation of potential by-products, as well as the stability and recyclability of the catalyst.
Solutions
H.E.L provides a wide range of products that aim to increase the efficiency of the process development phase. The ChemSCAN’s automated parallel catalyst screening capability enables the simultaneous exploration of up to 8 reactions, streamlining the path from discovery optimization. This setting is particularly relevant when different catalysts or their modifications function to identify the most stable variants. Parallelization allows the rapid evaluation of various catalysts, reagents, and reaction conditions up to a pressure of 200 bar. The adaptability of this benchtop system to different volumes, pressures, and temperatures controlled independently by H.E.L’s software makes the ChemSCAN a vital tool for researchers. On the other hand, the FlowCAT is designed to empower the development of continuous flow processes, both homogenous and heterogeneous, catering to a wide range of applications. The automation and software control permit dynamic adjustments of process parameters, facilitating faster screening and optimization studies.
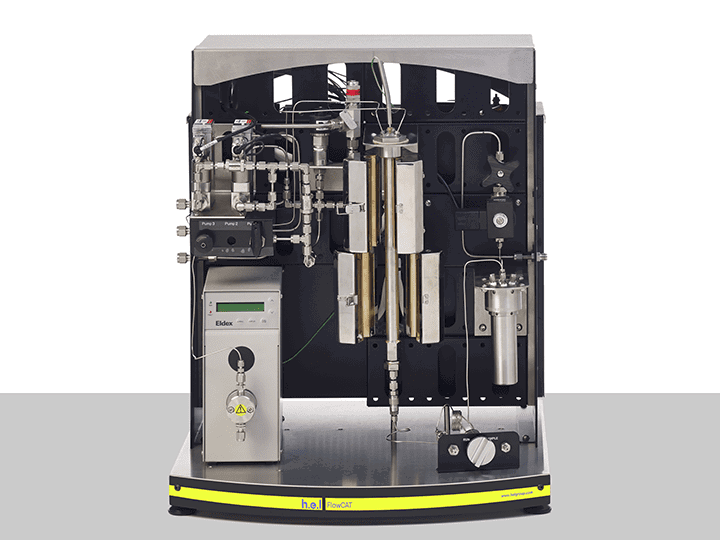
FlowCAT | A Bench-Top, High Pressure Flow Catalysis Platform
The FlowCAT is an automated high-pressure flow catalysis bench-top platform, designed fo...
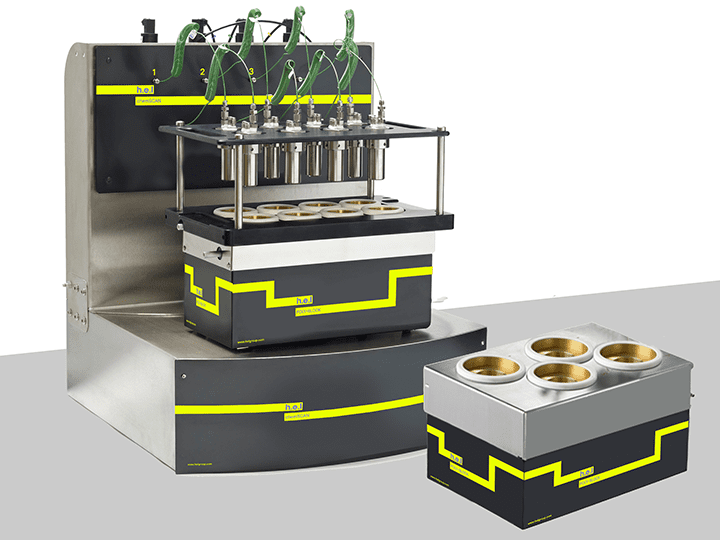
ChemSCAN | Parallel Catalyst Screening and Development Platform
ChemSCAN brings efficiency and flexibility to catalytic research by enabling up to 8 high-...
Scale-Up
What challenges need addressing during scale-up?
The scale-up phase involves several technical challenges that need overcoming to deliver an efficient industrial-scale process. This includes optimizing reaction conditions for larger volumes, including temperature, agitation, concentration of reactants, and dosing regimen. The final goal is to ensure consistent product quality and address potential safety concerns that might have been overlooked in the first phases of development. It is critical to overcome these issues to understand the process deeply, including reaction kinetics and thermodynamics, which may vary significantly when moving from benchtop to large scale.
How can scalable systems help in scale-up?
Using scalable systems is fundamental to overcoming the challenges that this last step can present. The flexibility of these systems allows for the testing and evaluation of different process parameters and conditions. The results obtained in this process enable researchers and engineers to identify the most efficient and cost-effective methods for large-scale production. Moreover, such systems can help to significantly reduce the time and resources necessary to achieve the goals in the scale-up phase, facilitating a smooth transition from laboratory to commercialization.
How do economic considerations impact scale-up?
As mentioned previously, the final goal of scaling up is creating a viable process in real-world manufacturing. This means that economic viability is paramount in this last step. An analysis of costs, including capital investment, operational expenses, and the potential for new or more efficient catalysts, must be factored in to achieve this goal. Apart from optimizing the chemical process to obtain optimal yield, evaluating the market demand for the end product and the competitive landscape is fundamental.
Solutions
The AutoLAB is a fully customizable reactor that can be tailored for the chemical reaction of interest. It is controlled by H.E.L’s own software and is intended to be fully automated with live data acquisition for temperature, pH, turbidity, and conductivity. With a maximum volume of 20 L, it is ideal in the first stages of the scale-up. Similarly, on the other hand, it can provide thermodynamic and kinetics data that are fundamental to understanding the reaction at higher volumes and identifying potential risks, like a thermal runaway. Additionally, its capabilities as an isothermal calorimeter make it an ideal instrument to characterize critical values such as the maximum temperature of reaction synthesis and maximum time to reaction, which are critical to designing safer processes.
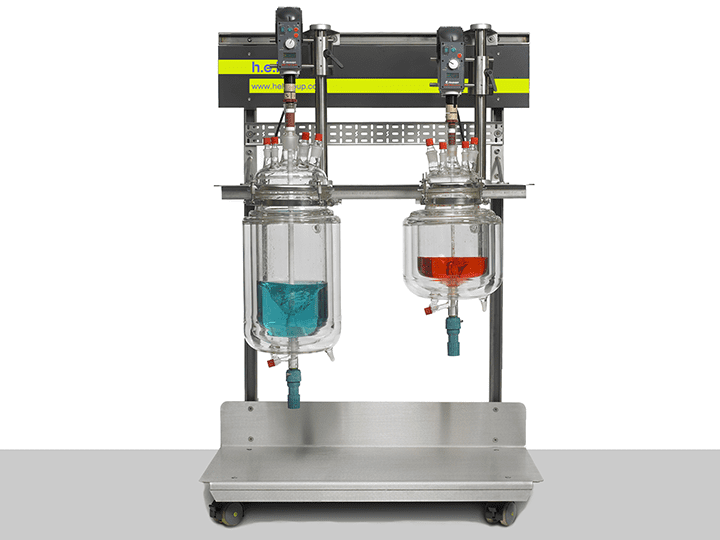
AutoLAB | Bench-Top Automated Reactor System
H.E.L’s fully customizable AutoLAB reactor platforms are designed, configured, and tailo...