Process Development
What are the optimal conditions?
Chemical reactions, regardless of the presence of catalysts, are constrained by several physical and chemical parameters. This phase aims to identify the range of values at which the chemical reaction has the highest yield and/or productivity. Still, in the case of catalysts, it also aims to determine the conditions under which the catalyst’s life is the longest.
In the previous section, we mentioned that catalysts can undergo processes that undermine their capabilities. For example, catalysts can experience poisoning, fouling, structural degradation, or leaching processes. In the Process Development phase, these potential undesirable effects need to be identified, and ways to mitigate them must be found. Depending on the type of substance used to accelerate the chemical reaction, these strategies can take different forms:
- Catalyst coating and active site stabilization: some of the catalyst’s active sites can be susceptible to reacting with other molecules, resulting in irreversible chemical bonds. This reduces the effectivity of the catalysts. Chemical modification of the surface of the catalysts can prevent non-specific reactions by limiting the access of molecules to the active sites and preventing this process.
- Development of regeneration methods: although one of the characteristics of the catalysts is the recovery of the molecule after the reaction, the reality is that over time, they become less and less effective. Certain processes need to be developed for them to become fully active again. The regeneration reaction will depend on the chemical nature of the catalysts and the modification they have suffered during their active life.
- Conditioning of the reagents: in many cases, especially in industrial settings, the source material for the reaction is of low purity. The result of this can be the occurrence of side reactions with unpredictable side effects (e.g., fouling and poisoning). Pretreatment of these materials can prove highly effective, reducing potential reduction in the catalyst activity.
How can processes be optimized?
The basic parameters in which the chemical reaction operates are defined during the process discovery phase. However, during the process development phase, these values are modified to study their impact on the productivity and efficiency of the reactions. Temperature provides kinetic energy to the atoms, favoring the re-arrangement of chemical bonds. On the other hand, specific catalysts can be susceptible at high temperatures (primarily biological), and as a result, they can undergo denaturation processes that render them useless. High pressure displaces the gas-liquid equilibrium towards the liquid phase, increasing the gas solubility and yield.
Stirring is a fundamental parameter required when liquid phases are involved in the reaction. Ensuring homogenous conditions is vital, preventing the formation of high-concentration pockets of reagents or products, which can result in precipitation.
What is the environmental impact of the process?
Evaluating the ecological effects of chemical processes has become the norm. More and more governmental bodies are putting in place guidelines to ensure that processes are as environmentally friendly as possible. The use of catalysts results in processes less prone to generating by-products. Nevertheless, this does not mean that side reactions can occur, and some of these products can be potentially polluting. It is for that that extensive characterization of the process is required at this stage. There are many variables to evaluate at this point; it is fundamental to understand the accumulation of potential by-products, as well as the stability and recyclability of the catalyst.
Solutions
H.E.L provides a wide range of products that aim to increase the efficiency of the process development phase. The ChemSCAN’s automated parallel catalyst screening capability enables the simultaneous exploration of up to 8 reactions, streamlining the path from discovery optimization. This setting is particularly relevant when different catalysts or their modifications function to identify the most stable variants. Parallelization allows the rapid evaluation of various catalysts, reagents, and reaction conditions up to a pressure of 200 bar. The adaptability of this benchtop system to different volumes, pressures, and temperatures controlled independently by H.E.L’s software makes the ChemSCAN a vital tool for researchers. On the other hand, the FlowCAT is designed to empower the development of continuous flow processes, both homogenous and heterogeneous, catering to a wide range of applications. The automation and software control permit dynamic adjustments of process parameters, facilitating faster screening and optimization studies.
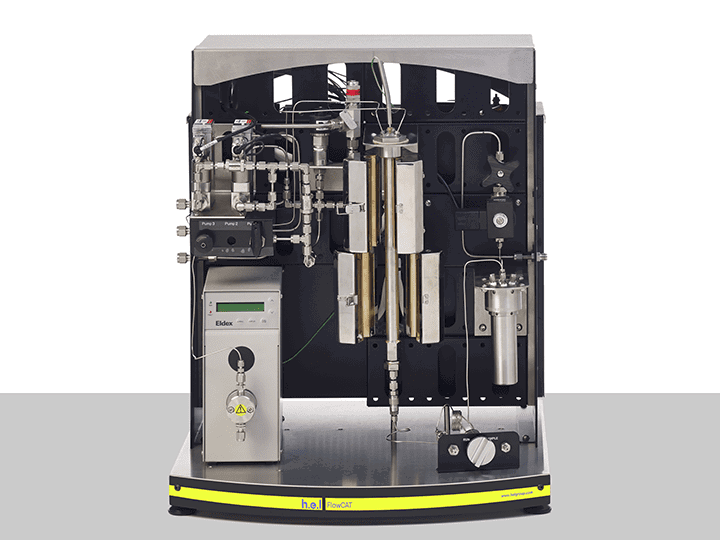
FlowCAT | A Bench-Top, High Pressure Flow Catalysis Platform
The FlowCAT is an automated high-pressure flow catalysis bench-top platform, designed fo...
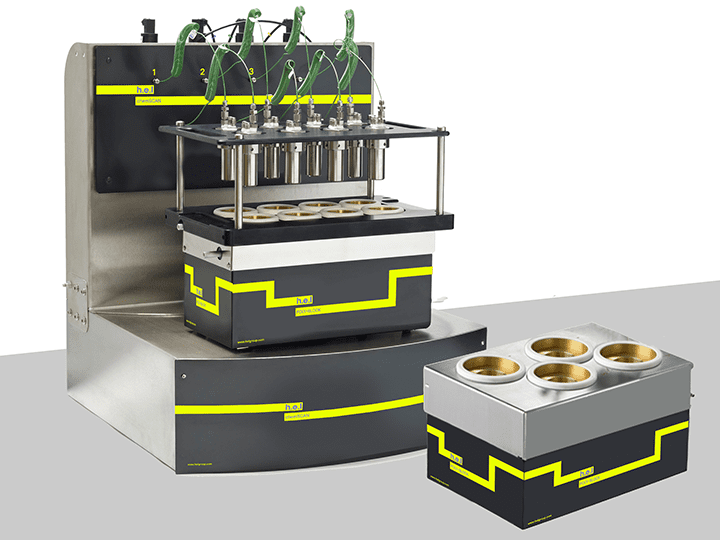
ChemSCAN | Parallel Catalyst Screening and Development Platform
ChemSCAN brings efficiency and flexibility to catalytic research by enabling up to 8 high-...