Scale-Up
What challenges need addressing during scale-up?
The scale-up phase involves several technical challenges that need overcoming to deliver an efficient industrial-scale process. This includes optimizing reaction conditions for larger volumes, including temperature, agitation, concentration of reactants, and dosing regimen. The final goal is to ensure consistent product quality and address potential safety concerns that might have been overlooked in the first phases of development. It is critical to overcome these issues to understand the process deeply, including reaction kinetics and thermodynamics, which may vary significantly when moving from benchtop to large scale.
How can scalable systems help in scale-up?
Using scalable systems is fundamental to overcoming the challenges that this last step can present. The flexibility of these systems allows for the testing and evaluation of different process parameters and conditions. The results obtained in this process enable researchers and engineers to identify the most efficient and cost-effective methods for large-scale production. Moreover, such systems can help to significantly reduce the time and resources necessary to achieve the goals in the scale-up phase, facilitating a smooth transition from laboratory to commercialization.
How do economic considerations impact scale-up?
As mentioned previously, the final goal of scaling up is creating a viable process in real-world manufacturing. This means that economic viability is paramount in this last step. An analysis of costs, including capital investment, operational expenses, and the potential for new or more efficient catalysts, must be factored in to achieve this goal. Apart from optimizing the chemical process to obtain optimal yield, evaluating the market demand for the end product and the competitive landscape is fundamental.
Solutions
The AutoLAB is a fully customizable reactor that can be tailored for the chemical reaction of interest. It is controlled by H.E.L’s own software and is intended to be fully automated with live data acquisition for temperature, pH, turbidity, and conductivity. With a maximum volume of 20 L, it is ideal in the first stages of the scale-up. Similarly, on the other hand, it can provide thermodynamic and kinetics data that are fundamental to understanding the reaction at higher volumes and identifying potential risks, like a thermal runaway. Additionally, its capabilities as an isothermal calorimeter make it an ideal instrument to characterize critical values such as the maximum temperature of reaction synthesis and maximum time to reaction, which are critical to designing safer processes.
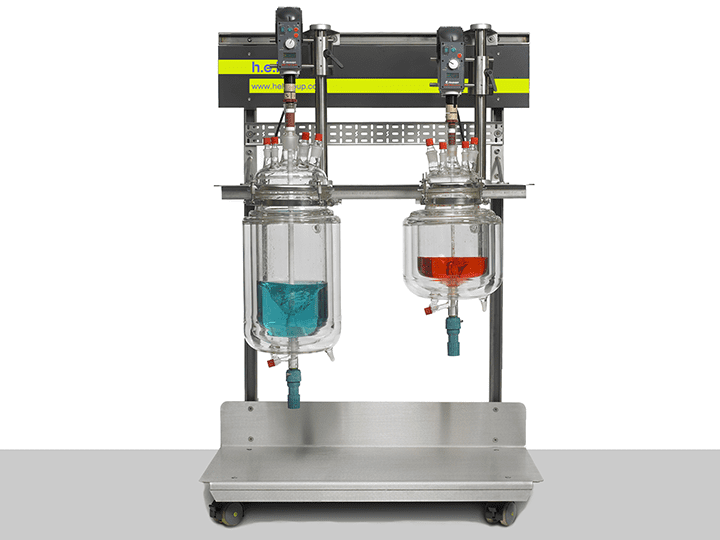
AutoLAB | Bench-Top Automated Reactor System
H.E.L’s fully customizable AutoLAB reactor platforms are designed, configured, and tailo...