Thermal Hazard of Component
What are the thermal hazards of the cell components?
The main components of an electrochemical cell – the basic component of a battery – are the anode, the cathode, and the electrolyte. The main sources of concern in electrical batteries are the electrolyte and the cathode. Organic carbonates are commonly used as electrolytes and are susceptible to decomposition reactions. These reactions involve a molecule breakdown, resulting in two or more chemical compounds. These reactions are typically exothermic, and energy is released in the process, which further fuels the breakdown of chemical compounds, creating a chain reaction called a thermal runaway. In the case of the decomposition of electrolytes, the results of the reactions are typically gases, some of which can be flammable. Decomposition reactions in batteries are normally evidenced by the compromise of the structural integrity of the battery itself.
On the other hand, cathodes are usually composed of a metal oxide, such as LiCoO2. When exposed to high temperatures, like those resulting from a thermal runaway, these metal oxides can undergo decomposition. The result of this decomposition will be the metal plus oxygen.
This is where the main problem of Lithium-ion batteries lies. The combination of flammable gases and oxygen and the extra heat provided can result in fire and battery explosions.
The separator is another component of the cells that can be susceptible to thermal hazards. Separators are designed to act as a physical barrier between the anode and cathode should a malfunction occur in the battery, preventing short-circuit events. However, most separators nowadays are made from polymers, which, in some cases, can melt or shrink at high temperatures. If this event takes place, thermal runaways could happen.
Solutions
Adiabatic calorimeters are designed to prevent heat exchange between the battery and its surroundings. Batteries experience shifting conditions during their lifespan, including heating and cooling. It is fundamental to understand how the cell components behave under a wide range of temperatures and environments and if they are susceptible to thermal runaways. An adiabatic calorimeter simulates a worst-case scenario where the battery is unable to dissipate its heat while under operation. BTC-130 is a bench-top adiabatic calorimeter especially designed for component and cell testing, including thermal, electrical, and mechanical stress. Using the BTC-130, you can assess the safety performance of the battery cell, the safe operating limit, and the consequences of the thermal runaway.
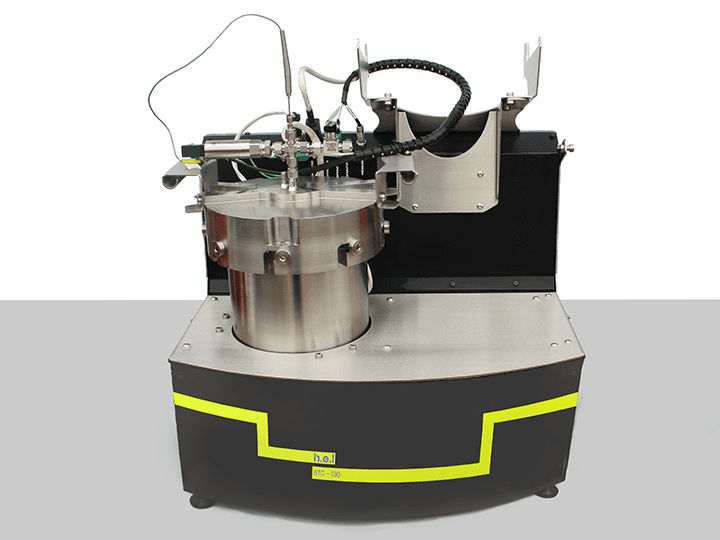
BTC-130 | Bench-Top, Battery Safety Testing, Adiabatic Calorimeter
The BTC-130 (Battery Testing Calorimeter) is a bench-scale adiabatic calorimeter designed ...
Batteries with superior attributes
How can we develop batteries with superior attributes?
Calorimetry is a fundamental tool to help build better batteries, including thermally stable batteries, higher energy density, shorter charging times, and longer operational times. In the previous section, we described how different components of a battery are susceptible to failures due to thermal hazard. However, a battery is much more than its basic components or sub-components, and the interaction between them can amplify problems such as thermal runaways, but also help to mitigate their consequences.
Understanding Thermal Behaviour
The electrolyte and cathode in Lithium-ion batteries are the most susceptible parts to damage due to thermal hazards. We can use calorimetry to predict the temperatures at which thermal runaways might happen, evidenced by sudden temperature increases. Processes such as charge/discharge can increase the cell temperature and, as a result, trigger decomposition reactions. The accumulation of energy from the decomposition of the electrolyte can increase the temperature, initiating the decomposition temperature of the cathode. The result of such decomposition is oxygen, which, reacting to the flammable gases accumulated in the battery, can result in fire and explosions.
Additionally, when developing cells, extra elements can be put in place to prevent thermal runaways, e.g., separators. Separators are usually composed of polymers with pores through the structure, allowing ions to transfer. Separators are designed to close those pores at high temperatures, stopping the chemical reaction. However, separators can also fail and, at high temperatures, may shrink, therefore allowing the ionic movement, resulting in a short-circuit. Calorimetry can help to understand how much energy can be released from the decomposition reactions, what temperature is needed to initiate the secondary runaway reaction and the consequences of such a process. The result of this analysis will determine the safe values at which the battery can operate.
Designing Thermal Management Systems
Calorimetry data can guide in the design of thermal management systems for batteries. Elements such as heat sinks, cooling fans, and other heat dissipation strategies are fundamental for maintaining optimal operating temperatures, enhancing performance, extending lifespans, and preventing hazardous scenarios.
Solid-electrolyte Interface (SEI)
The SEI plays a vital role in the safety of Lithium-ion batteries, performance, and operation. The SEI is a thin layer that forms on the surface of the anode during the initial charging cycles of the battery. It is the result of the interaction between the electrolyte and the anode, and it is composed of lithium salts dissolved in organic solvents.
The SEI acts as a physical barrier between the anode and the electrolyte, insulating yet ionically conductive. As it blocks further physical contact between the electrolyte and the anode, it prevents further degradation of the latter, allowing lithium movement. However, over long periods of time and successive charge/discharge cycles, its capacity can fade, resulting in the cells losing its capabilities to hold charge. Moreover, it can increase internal resistance, leading to less efficient charging and discharging and an increase in temperature.
Accelerated aging testing
A battery’s performance decreases over time due to a number of processes, e.g., formation and growth of SEI, progressive degradation of the electrolyte, partial dissolution of the electrodes in the electrolyte, and increased internal resistance. Understanding these processes is fundamental in predicting the lifespan of the battery, but also what are the consequences of operating old batteries. Batteries are exposed to harsh conditions when using accelerated aging tests, simulating long-term usage in shorter timeframes. The thermal response of the battery can provide insight into how its performance and safety attributes change.
Battery failure testing
The formation of low-resistance paths for electric current between the electrodes can result in short-circuits, leading to rapid battery discharge, overheating, and potential fires. At a cell level, this process can occur in a number of scenarios, like a breach in the separator or the formation of lithium dendrites. These occur when batteries are charged too rapidly or at low temperatures. The lithium ions can deposit, forming spikey structures that can grow through the separation, creating a conductive path between the anode and the cathode. Destructive testing allows for the irreversible physical damage of the cell, such as perforation, simulating these processes.
Solutions
Superior attributes could refer to either better performing batteries at safer conditions or the capacity of batteries to withstand harsher conditions.
There are some critical points when developing new batteries: larger amounts of energy storage, charge stability overtime, and efficient discharge processes H.E.L’s iso-BTC is an isothermal calorimeter designed to characterize battery cells under normal and extended use conditions. The iso-BTC supports the integration of a charge/discharge unit, allowing for automated, repeated cycling of the battery cells while recording both electrical performance and heat evolved.
The BTC-130 and BTC-500 are powerful tools to test the behavior of the battery outside of its safe limits. Both BTC systems fully integrate with charge-discharge units to support electrical stress tests, including external short-circuits. Using adiabatic calorimetry, BTC-130 and BTC-500 can help assess the battery’s thermal stability and characterize thermal events. Furthermore, BTC-500 can be equipped with a range of puncture tools and a camera to characterize physical damage events.
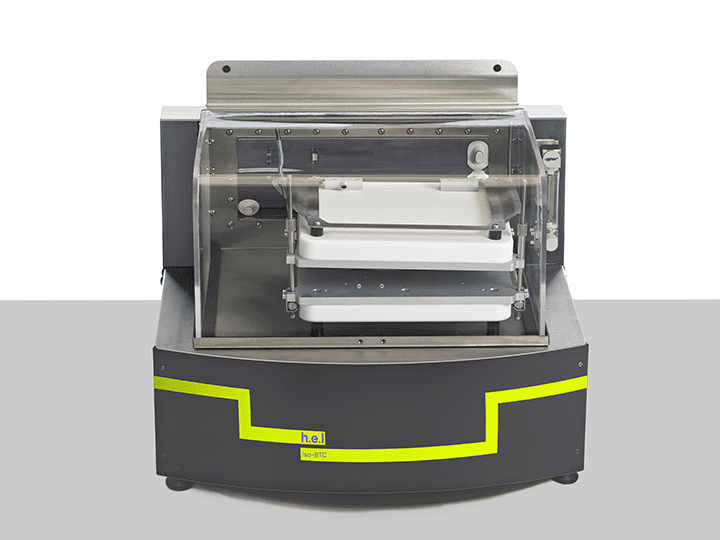
iso-BTC | Bench-top, battery performance testing, isothermal calorimeter
The iso-BTC (Battery Testing Calorimeter) is an isothermal calorimeter designed for the ch...
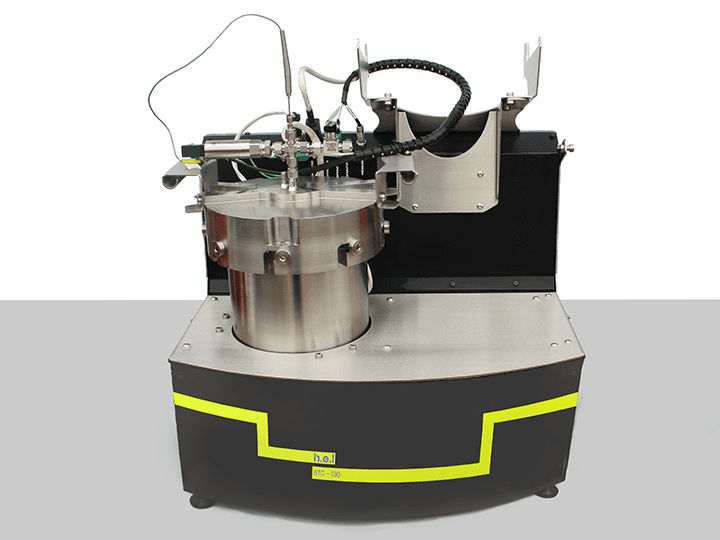
BTC-130 | Bench-Top, Battery Safety Testing, Adiabatic Calorimeter
The BTC-130 (Battery Testing Calorimeter) is a bench-scale adiabatic calorimeter designed ...
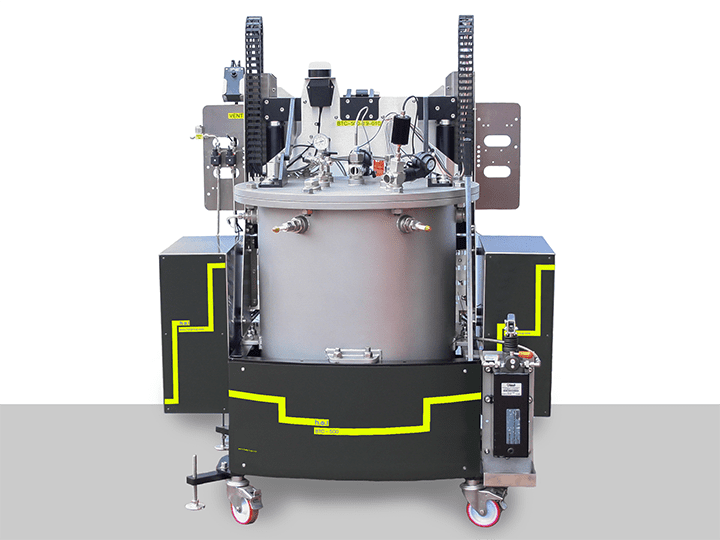
BTC-500 | Large-scale, battery testing, adiabatic calorimeter
The BTC-500 (Battery Testing Calorimeter) is a floor-standing adiabatic calorimeter for th...
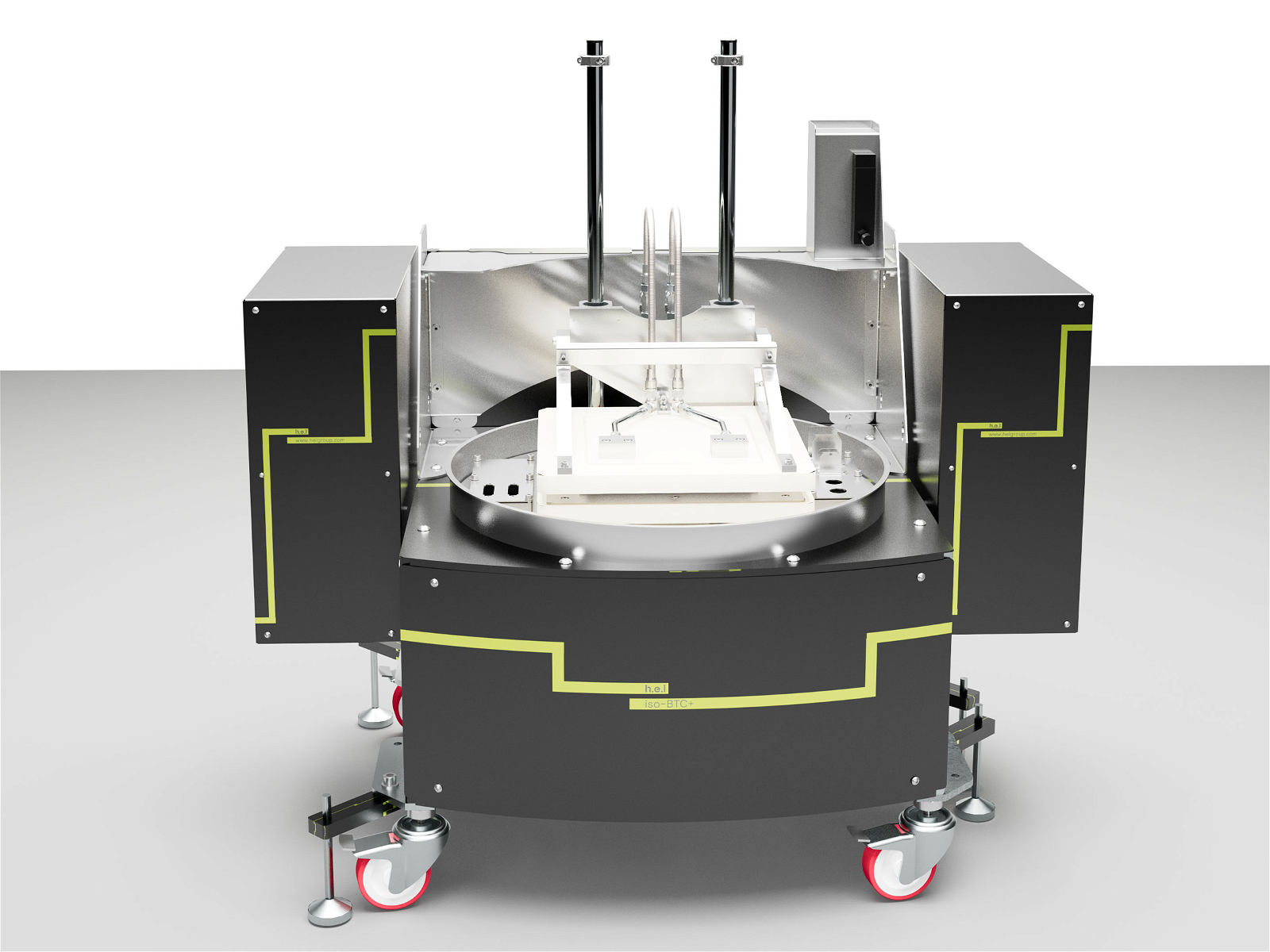
iso-BTC+ | Floor standing, battery performance testing, isothermal calorimeter
Faster product development, testing, and launch through scientifically robust data: R...
Quality Control
How can calorimetry help that cells pass quality control?
As the use of lithium-ion batteries continues to grow in popularity and importance, both in industry, in transport, and in day-to-day activities, it is important that these battery are safe and reliable. In the months running to this post, an increase number of accidents involving Lithium-ion batteries have been reported in the press. This highlights the importance of robust testing and strong legislation to ensure the safety of users.
The United Nations (UN) established the Manual of Tests and Criteria (UN 38.3) to set standards for the safe transportation of batteries. This manual outlines the tests and requirements that batteries must meet in order to be considered safe for transportation. The International Electrotechnical Commision (IEC), through the IEC 62133 also established what that the safety standards are for batteries in consumer electronics. Amongst these standards, it outlines what the requirements are to cover electrical, mechanical, and environmental terms. Similarly, the Underwriters Laboratories (UL) published UL2054, establishing the safety standards in various applications, including consumer electronics, energy storage, and automotive.
Other regulatory bodies that have published safety guidelines on battery safety include the International Organization for Standardization (ISO), which published the ISO 12405, covering the requirements for batteries for electric vehicles regarding electrical, mechanical, and environmental safety. The Japanese Industrial Standards (JIS) through JIS C 8714 and the Chinese National Standard (GB/T) also cover the same aspects of batteries. In the US, the UL 1642, although not legally binding, contains the recommendations for lithium-containing batteries and focuses on their thermal, mechanical, and electrical characteristics and fire and shock resistance.
So, we can see a growing body of internal legislation that aims to produce safer batteries.
Commonalities
Legislation, directives, and battery recommendations aim to produce safer batteries, but what is considered safe?
On the electrical side, batteries must withstand potential stress, including overcharging and over-discharging, without the potential of a fire or explosion hazard. Overcharging occurs due to excessive voltage, causing current to flow into the battery after reaching full charge. Overdischarging, on the other hand, is the discharging of the battery beyond the lower safe voltage or discharging a battery at an unsuitable current. The result of both processes is the overheating of batteries, which can result in the generation of thermal runaways.
Mechanically, batteries should be able to endure various mechanical stresses, such as impact, vibration, or crush tests, without rupturing, leaking, or short circuits (both internal and external).
Battery operation sometimes includes transient conditions that can affect batteries. These include high temperatures (which can result in thermal runaways), low temperatures (reduce the ion transmission capacity of the electrolyte), humidity, or different atmospheric pressures.
As we can see, batteries can result in temperature anomalies due to their own functioning or environmental conditions. Batteries need to be able to dissipate heat to maintain safe operation temperatures, therefore preventing hazardous scenarios.
Battery testing
Batteries will behave differently when operating at different temperatures, and three main thermal regions can be defined:
- Optimum zone: batteries operating within optimal conditions will behave normally, and aging processes will be as slow as possible.
- Safe zone: the battery will function in this zone, but performance can be compromised, especially charging/discharging speed and aging. Higher temperatures can result in accelerated degradation of the electrolyte. Lower temperatures can result in a reduction in the conductivity of the electrolyte, as well as the deposition of lithium-organic compounds onto the SEI.
- Dangerous zone: conditions are likely to result in hazardous scenarios.
Calorimetry is an invaluable tool for the testing of batteries.
Isothermal calorimeters maintain the battery at a constant temperature and measures its thermal energy changes. It is possible to monitor the electrical output of the battery, thus delivering both thermal and electrical behaviour information. Integrating the instrument with a charge-discharge unit enables the automation of repeated cycling of battery cells under various charge and discharge rates. This type of testing allows for determining the battery’s performance within the Optimum Zone and Safe Zone.
On the other hand, Adiabatic calorimeters maintain batteries under adiabatic conditions, where there is no heat exchange with the surroundings. This calorimeter allows us to subject the battery to extreme conditions within a safe environment to evaluate the consequences. These conditions include higher temperatures, voltages, and discharge currents outside the Safe Zone. Some adiabatic calorimeters can be equipped with means to test for mechanical stress, such as crushing or perforation. Adiabatic calorimetry enables the battery response within the Dangerous Zone to be explored.
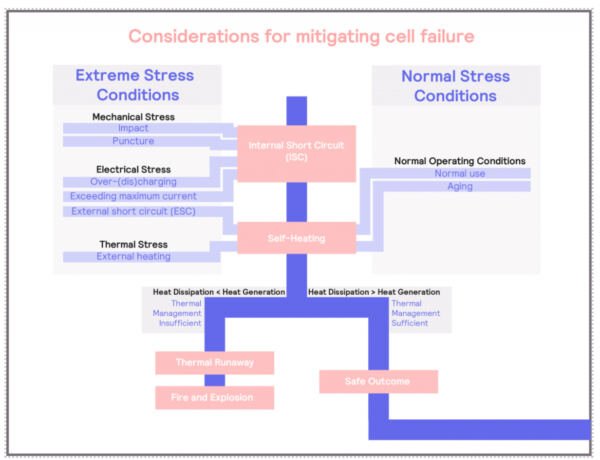
Considerations for Mitigating Cell Failure
Solutions
The iso-BTC is designed as an isothermal calorimeter, allowing battery performance testing. Battery efficiency and heat evolved at specific temperatures, and charge-discharge rates are fundamental parameters that must be tested for cell manufacturers and integrators. Moreover, identifying safe operating limits to avert the risk of thermal runaway is fundamental. Batteries must be tested to obtain a safe working temperature, maximum safe voltage, and maximum safe current. These values can be obtained using BTC-130 and BTC-500. These battery operational parameters need to be appropriate and comply with the current legislation in order for the batteries and battery-powered devices to be commercialized.
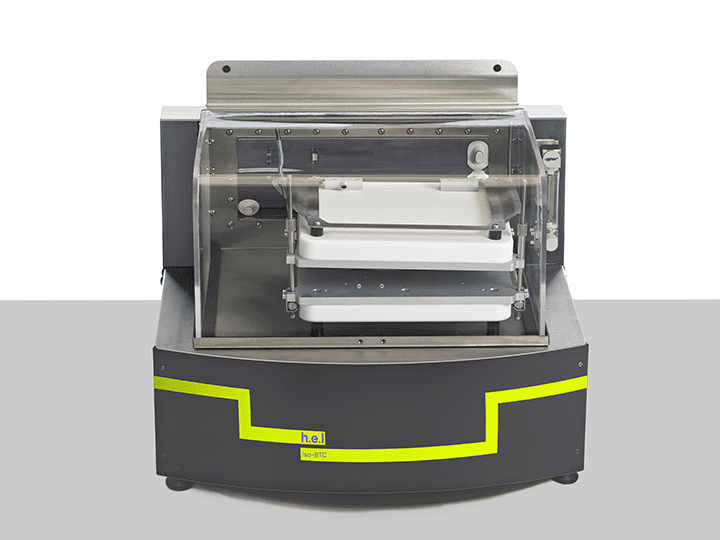
iso-BTC | Bench-top, battery performance testing, isothermal calorimeter
The iso-BTC (Battery Testing Calorimeter) is an isothermal calorimeter designed for the ch...
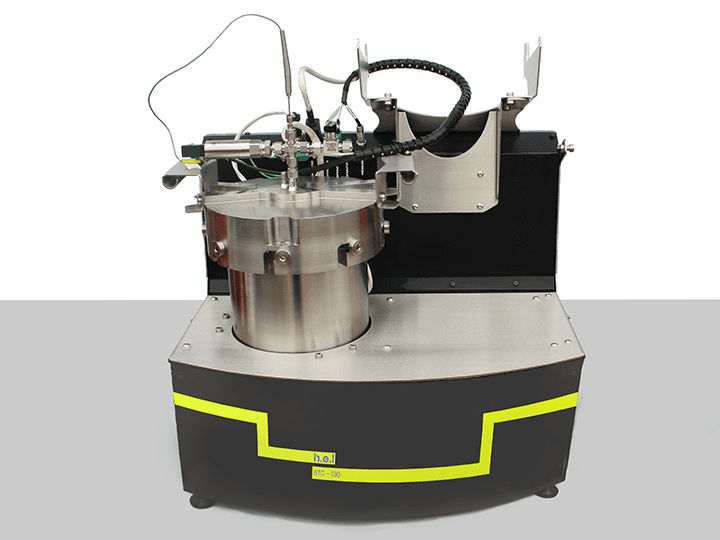
BTC-130 | Bench-Top, Battery Safety Testing, Adiabatic Calorimeter
The BTC-130 (Battery Testing Calorimeter) is a bench-scale adiabatic calorimeter designed ...
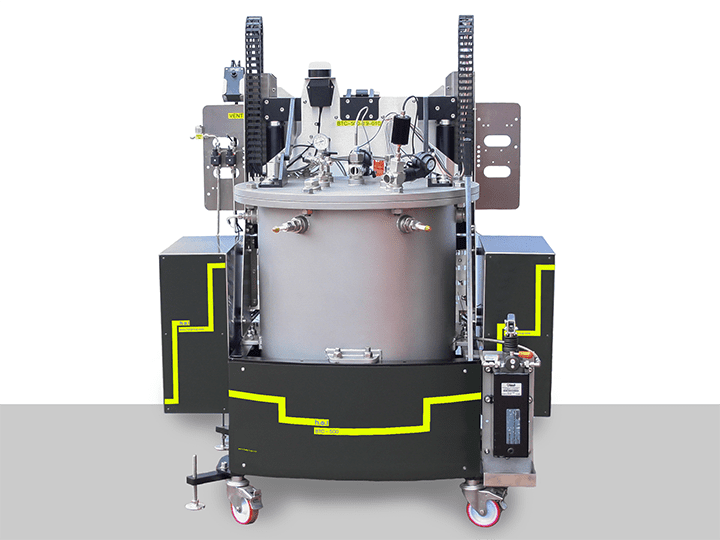
BTC-500 | Large-scale, battery testing, adiabatic calorimeter
The BTC-500 (Battery Testing Calorimeter) is a floor-standing adiabatic calorimeter for th...
Mitigate Thermal Runaways
How can we mitigate the risks of thermal runaways?
Thermal runaways, once initiated, can lead to the rapid release of stored energy in the form of heat, potentially resulting in a fire or an explosion. Although prevention of such a process should always be a priority, under certain conditions, thermal runaways will occur, and it is imperative to mitigate the risks associated with it.
In previous sections we have extensively discussed how we can understand the process: understanding the conditions that will result in thermal runaways, such as the chemical components (anode and electrolyte), possibility of internal short-circuits (for example, dendritic growth at low temperatures), and external factors (such a high temperature, or mechanical damage).
Adiabatic calorimeters can help to understand what the consequences of thermal runaways are. Adiabatic calorimetry can help to determine what the temperature at which the thermal runaways might occur (exotherm) and the temperature that the battery can reach. Propagation tests allow us to characterize how the thermal runaway can affect the neighboring cells and understand the risks of cascading failures.
However, assuming that the worst could happen can help to design methods to mitigate the potential damage that thermal runaways can inflict.
Mitigation strategies
Thermal Management Systems: this strategy is based on removing heat, avoiding reaching high temperatures in hot spots that initiate the thermal runaway. In order to achieve temperature uniformity, strategies such as active systems (e.g., liquid or air cooling) and passive (phase changing material, heat spreaders) may be used.
Cell Design and Separators: as mentioned in previous sections, separators act as physical barriers between the electrodes. These structures activate at high temperatures, shutting down the ionic flow and stopping the battery from functioning. One of the strategies used in the separator is using structures that physically change under thermal runaway risk, closing down the pores.
Battery Management Systems (BMS). A BMS monitors and manages the battery’s operation, ensuring it remains within the limits of the Safe Zone. If dangerous conditions are met, BMS can disconnect the battery from the load or source.
Physical Barriers: in multi-cell batteries, physical barriers or fire-retardant materials can be placed between cells to prevent or slow thermal propagation.
Solutions
The iso-BTC and iso-BTC + allow for thermal mapping during testing, highlighting the regions of the battery that are more susceptible to generating heat. This information can be used to design and implement efficient thermal management strategies. Additionally, using the information supplied by BTC-130 and BTC-500 can help predict the battery’s thermal behavior. Detecting decomposition temperatures and the resultant heat released can help understand the thermal runaway from the process. BTC-500 can be further used to initiate physically-induced thermal runaways and capture the event unfolding using its integrated camera.
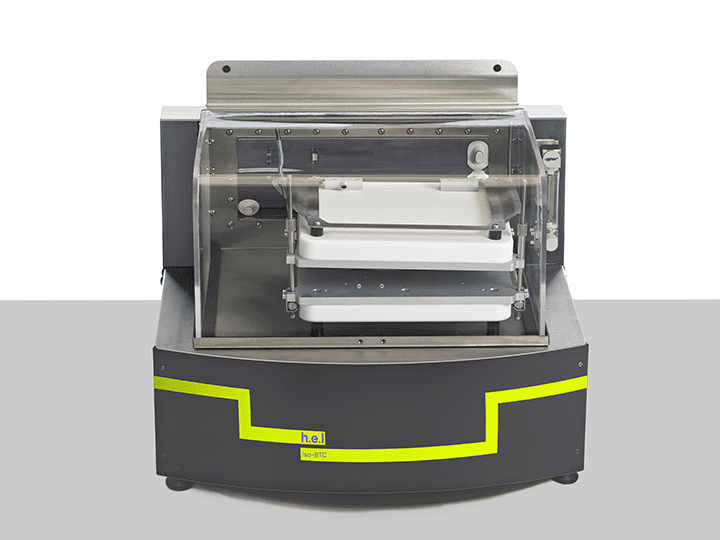
iso-BTC | Bench-top, battery performance testing, isothermal calorimeter
The iso-BTC (Battery Testing Calorimeter) is an isothermal calorimeter designed for the ch...
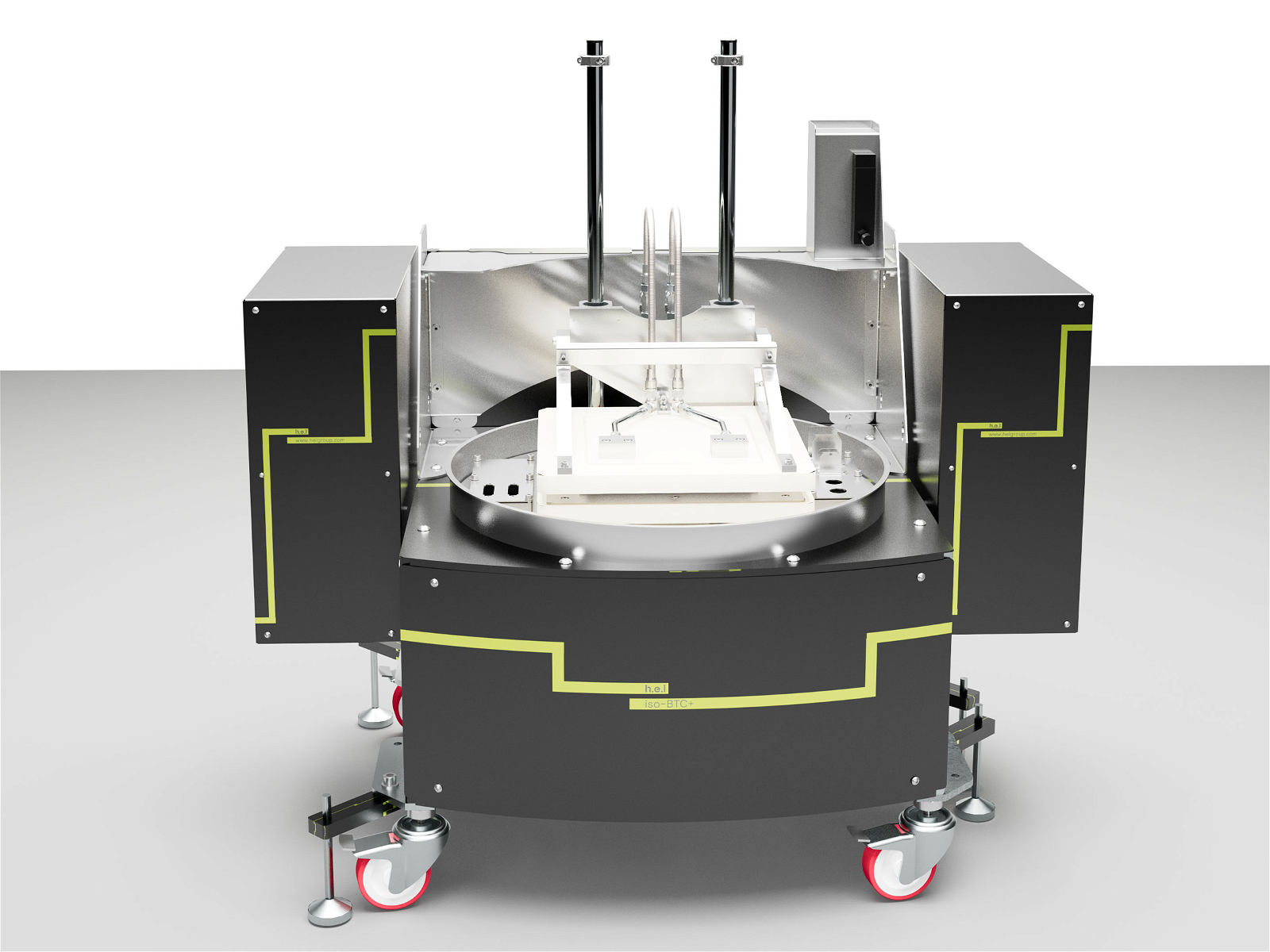
iso-BTC+ | Floor standing, battery performance testing, isothermal calorimeter
Faster product development, testing, and launch through scientifically robust data: R...
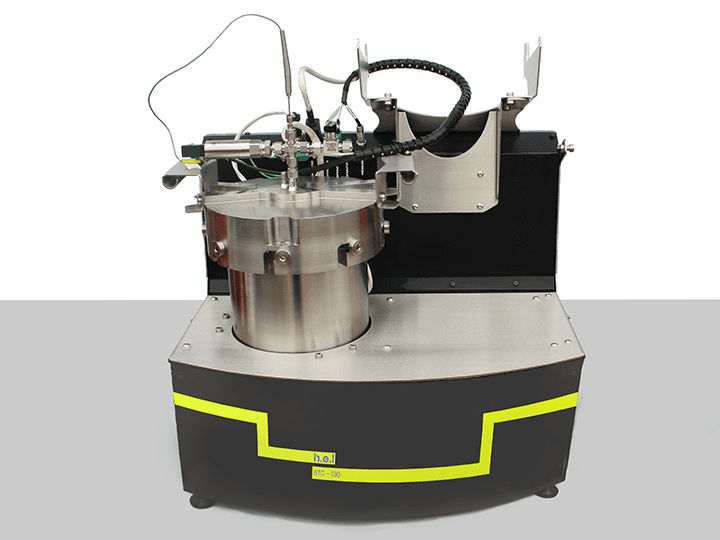
BTC-130 | Bench-Top, Battery Safety Testing, Adiabatic Calorimeter
The BTC-130 (Battery Testing Calorimeter) is a bench-scale adiabatic calorimeter designed ...
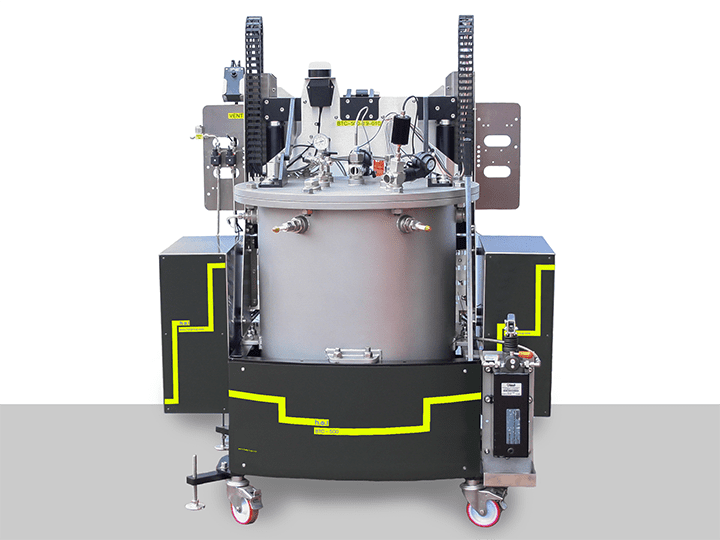
BTC-500 | Large-scale, battery testing, adiabatic calorimeter
The BTC-500 (Battery Testing Calorimeter) is a floor-standing adiabatic calorimeter for th...