Process Development
How Can The Operating Conditions Be Modified To Reduce The Risks Identified?
Stoessel diagrams can help us understand how risky chemical processes are, including desired reactions and secondary reactions (such as decomposition reactions). Stoessel classification identifies 5 possible scenarios, ranked from least dangerous to most dangerous. The commonality that the three first categories have, is that the maximum temperature of synthesis reaction (MTSR – the maximum temperature the reactor would reach if a failure in cooling occurs) stays under the temperature of decomposition (Td, temperature at which some of the reactants or products start to break down at a detectable rate).In the case of scenarios (D) & (E), it is necessary to consider if the MTSR can be reduced by altering the conditions of the reaction to reduce the levels of accumulated reagent.
There are several ways this could be addressed, such as [1]:
- Increasing the temperature of the reaction
- Increasing the pressure of the reaction
- Increasing the agitation of the reaction mix
- Adding a catalyst
- Reducing the feed rate of the reactant
The first four methods will increase the reaction rate and thus increase the reagent’s consumption rate. However, it must be balanced against the subsequent increase in the rate of heat evolved, and so an assessment on whether the plant’s cooling capacity can contain this increase in heat.
Reducing the reactants’ feed rate will reduce the reagent accumulation rate as it effectively allows more time for the reaction to occur and the rate-limiting reagent to be consumed before it accumulates to hazardous levels.
Exploring the impact of varying these different factors on the reaction is desirable. The Simular enables users to experiment in this way by creating experiments that facilitate the identification of optimum operating conditions for reducing thermal risk. For example, an esterification reaction in which acetic anhydride is fed into a reactor containing methanol can be kept at different temperatures. So let us analyze how different feed rates can affect the power needed to keep the conditions isothermal and accumulated reagent.
Reducing The Feed Rate
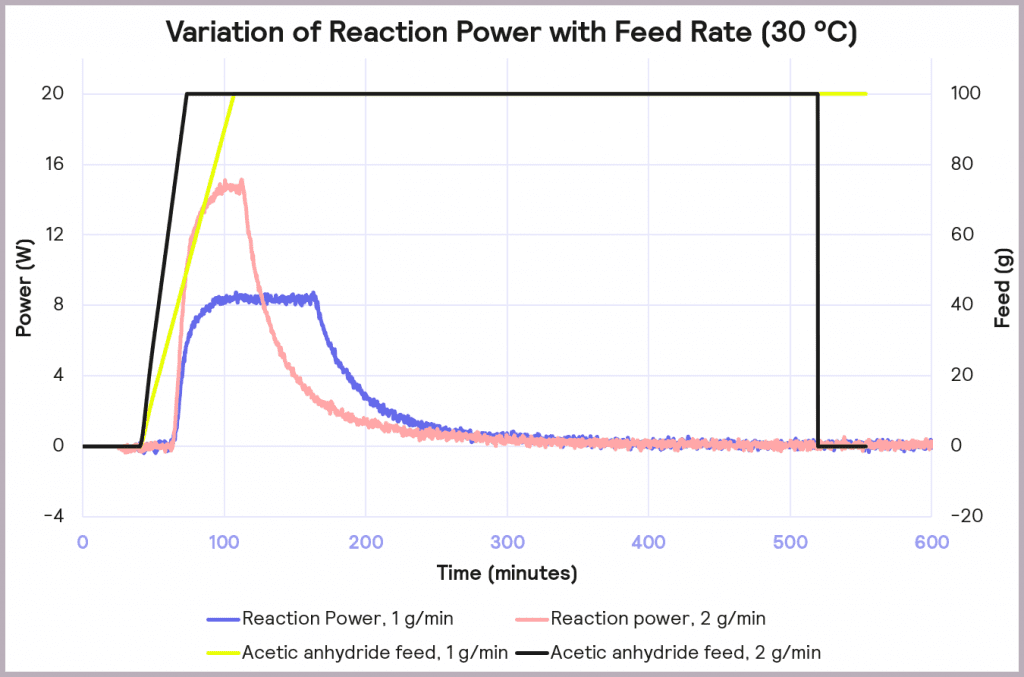
The effect of reducing the feed rate from 2 g/min to 1 g/min, while keeping the temperature of the process at 30 ⁰C, is illustrated in Figure 8. It reduces the accumulation of reagent to 32% at the point at which the feed stops, and it reduces the maximum reaction power from 15 W to 8 W. This reduction in maximum reaction power significantly reduces the cooling capacity required to keep the reaction isothermal and under thermal control.
Increasing the Temperature
The accumulated reagent level can be further reduced by increasing the temperature from 30 ⁰C to 40 ⁰C while maintaining the slower feed rate of 1 g/min. The impact of this is depicted in Figure 11. This reduces the level of reagent accumulated to 22% at the point at which the feed is stopped, but it does increase the maximum reaction power from 8 W to 10 W.
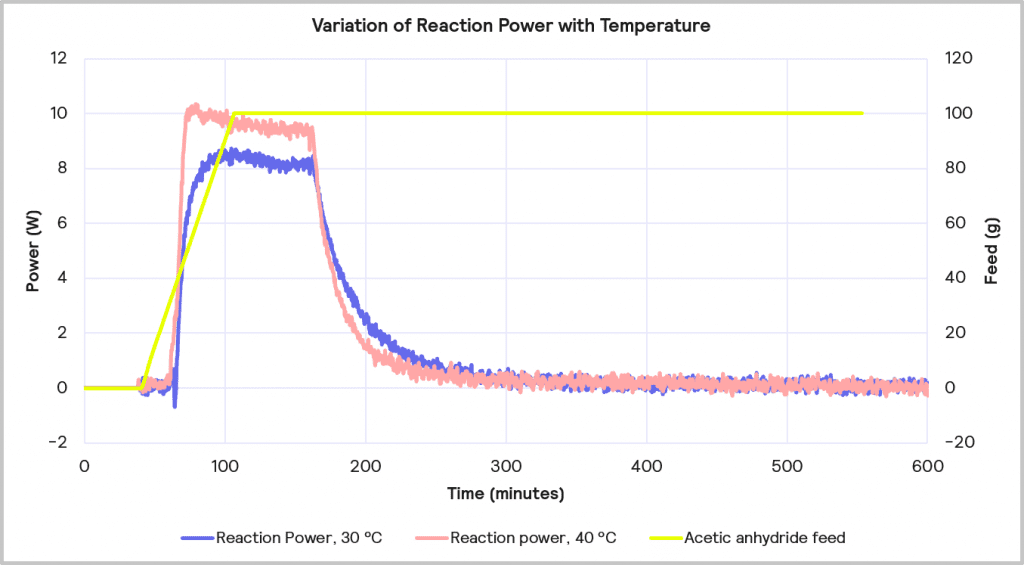
Cooling Capacity Considerations
Increasing the reaction temperature poses an interesting question: while the increase in temperature will result in less accumulated reagent and thus a lower MTSR, should cooling fail, and a thermal runaway occurs, it does require a larger cooling capacity to deal with the faster rate of heat evolved. As before, if it is assumed that the 1 L lab-based reactor is initially scaling up to a 2000 L reactor, the 10W reaction power for the reaction run at 40⁰C equates to a 20 kW cooling capacity requirement on scale-up versus the 16 kW required for the same reaction run at 30⁰C. Therefore, although the 1g/min feed rate with 40⁰C process temperature is the desired combination from a safety point of view in terms of reagent accumulation, it may be that a lower temperature is required if the cooling capacity of the pilot plant is <20 kW.
Another vital consideration is the efficiency of the cooling. As the scale of the reaction increases, the thermal transfer efficiency from the temperature-controlling system will likely decrease. Because of this, the cooling capacity will probably have to increase. A suitable safety factor must also be applied to the cooling capacity to ensure the system can handle unexpected thermal events.
Ideally, a process should be as close to a dose-controlled reaction as possible. In this scenario, the reactant is consumed as rapidly as it is added. Therefore, in the event of a cooling or agitation failure, it is usually sufficient to switch off the feed to prevent a thermal runaway.
However, in cases where accumulation can’t be avoided, it is necessary to undertake a more detailed analysis of the risk.
Solutions
The Simular measures the energy evolved in the reaction. Subsequently, this enables you to calculate the plant cooling capacity required to keep the reaction isothermal (Tp). It also allows for the Maximum Temperature of Synthesis Reaction (MTSR) to be calculated from the reaction data. For this reason, the Simular can be used to explore and design safer reaction conditions, thereby facilitating the optimization of safe operations and minimizing process risk.
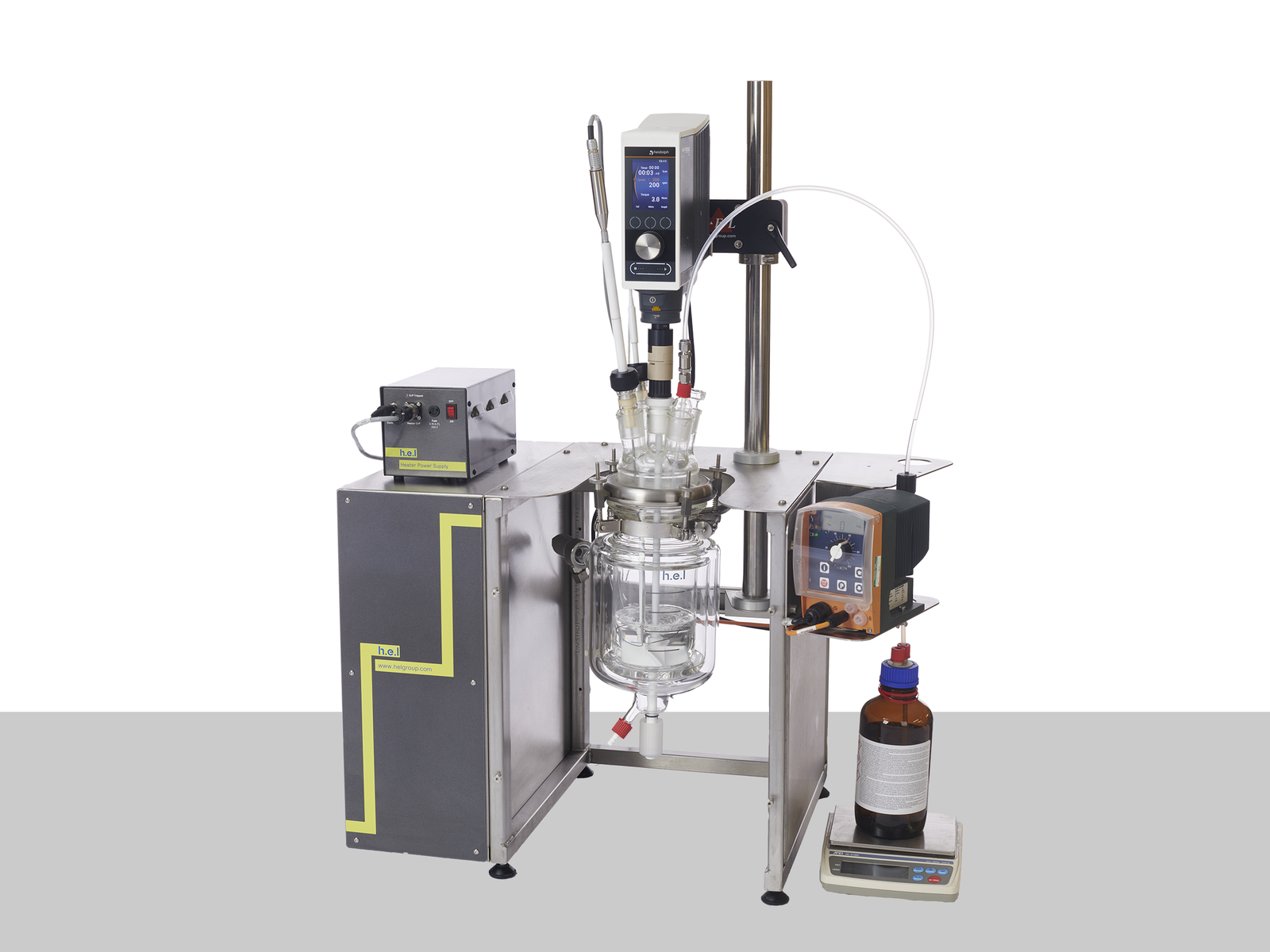
Simular | Process Development Reaction Calorimeter
This highly configurable system from the H.E.L product family excels in optimizing process...