Simular | Process Development Reaction Calorimeter
This highly configurable system from the H.E.L product family excels in optimizing process conditions and determining safer reaction conditions. With dual reactor options available, offering more flexibility for applications.
In addition to traditional heat flow calorimetry, the Simular offers power compensation calorimetry allowing operators to skip time-consuming calibration steps and get more conditions screened. The Simular is ideally suited for process safety and scale-up of the most varied and demanding reactions.
Chemical Synthesis Specifications
Process Safety and Scale Up Specifications
Overview
Highly Configurable & Flexible System
The Simular Process Development Reaction Calorimeter is a highly configurable and flexible system, designed as part of the H.E.L product family for process safety and chemical synthesis, featuring dual reactor options. Its unique capabilities as a calorimeter and an automated jacketed reactor allow for exceptional versatility in various applications, including adiabatic calorimetry, autocatalysis, and batch and semi-batch reactors.
Optimize Process Conditions
Leveraging the derived thermodynamic and kinetic information of the reaction, the system aims to optimize process conditions, achieving the dual goals of maximizing product yield while minimizing safety hazards. It enables efficient and effective adjustments to key operating parameters by precisely monitoring and controlling the heat flow.
Determine Safer Reaction Conditions
Determining the safer reaction conditions is crucial to ensuring safety during scale-up operations. The system facilitates this by calculating the plant cooling capacity required for maintaining isothermal conditions (Tp) and accurately predicting the maximum temperature the main reaction may reach during a thermal runaway. These calculations are vital in determining the emergency cooling capacity needed for robust scale-up.
Calibration-Free Power Compensation Calorimetry
The Simular Process, Development Reaction Calorimeter, supports both classic heat flow calorimetry and advanced calibration-free power compensation calorimetry. This advanced feature allows users to choose the most appropriate method for their specific reaction requirements, ensuring accurate and reliable measurements for precise process control and optimization.
Applications
Reaction Calorimetry
Thermal properties of the desired reaction (1)
The Simular measures the energy evolved in the reaction. Subsequently, this enables you to calculate the plant cooling capacity required to keep the reaction isothermal (Tp).
Thermal runaway of the reaction (2)
In the event of plant failure, it is critical to understand the maximum temperature the main reaction will reach during any subsequent thermal runaway.
The Simular enables the Maximum Temperature of Synthesis Reaction (MTSR) to be calculated from the data of the reaction. Multiple reaction conditions can also be screened to help understand the kinetics of the reaction. From this, it can be assessed whether there will be sufficient time and emergency cooling capacity to deal with the temperature increase.
Minimizing the risk
Hazard assessments may highlight insufficient plant emergency capacity to avert the risk of thermal runaway. The Simular can be used to explore and design safer reaction conditions, thereby facilitating the optimization of safe operations and minimizing process risk.
Technical Literature
The following is a list of supporting Technical Literature.
Calorimetric analysis of CO2 absorption in an aqueous N-methyldiethanolamine solution using H.E.L.’s Simular
Comparison of different calorimetry methodologies using Simular reaction calorimeter
Publications
The following are a list of some technical publications which highlight the use of the equipment.
On the Breakage of High Aspect Ratio Crystals in Filter Beds under Continuous Percolation
F. M. Mahdi, A. P. Shier, I. S. Fragkopoulos, J. Carr, P. Gajjar and F. L. Muller
29-Oct-2022
https://link.springer.com/article/10.1007/s11095-020-02958-x(Subscription or purchase maybe required for full access)
Use of isoperibolic reaction calorimeter for the study of reaction kinetics of acetic anhydride hydrolysis reaction: Effect of acetic anhydride and water ratio
Rajendra Kumar and Anurag Kumar Tiwari
06-Apr-2022
https://journals.pan.pl/Content/124706/PDF/art17_int.pdf(Subscription or purchase maybe required for full access)
Thermal Hazards of Synthesizing a Grignard Reagent under Different Dosing Rates
Wei Wang , Jiancun Gao , Chenguang Shi, Shengnan Wang, Yujing Li, Xiong Dai, and Tianmeng Jiang
01-Mar-2022
https://doi.org/10.1155/2022/6776179(Subscription or purchase maybe required for full access)
Thermal hazards evaluation of the synthesis of N-methylmorpholine-N-oxide
Jiancun Gao, Chenguang Shi, Sisi Liu, Shengnan Wang and Wei Wang
18-Sep-2021
https://link.springer.com/article/10.1007/s10973-021-11052-2(Subscription or purchase maybe required for full access)
A study on the scale-up of acyl azide synthesis in various continuous flow reactors in homogeneous and biphasic systems
Cloudius R. Sagandira and Paul Watts
18-May-2018
https://doi.org/10.1007/s41981-018-0010-9(Subscription or purchase maybe required for full access)
The effect of using a methanol–water solvent mixture on pH oscillations in the palladium-catalyzed phenylacetylene oxidative carbonylation reaction
Julie Parker and Katarina Novakovic
30-Sep-2017
https://link.springer.com/article/10.1007/s11144-017-1282-z(Subscription or purchase maybe required for full access)
Autonomous reorganization of the oscillatory phase in the PdI2 catalyzed phenylacetylene carbonylation reaction
Julie Parker & Katarina Novakovic
11-Feb-2016
https://doi.org/10.1007/s11144-016-0979-8(Subscription or purchase maybe required for full access)
Oscillatory carbonylation of phenylacetylene in the absence of externally supplied oxidant
Lynn Donlon, Julie Parker and Katarina Novakovic
19-Feb-2014
https://doi.org/10.1007/s11144-014-0685-3(Subscription or purchase maybe required for full access)
Inherently safer reactors: Improved efficiency of 3-picoline N-oxidation in the temperature range 110–125 °C
Alba Pineda-Solano, Lina Saenz-Noval, Subramanya Nayak, Simon Waldram, Maria Papadakic and M. Sam Mannan
05-Nov-2012
https://www.sciencedirect.com/science/article/pii/S0957582012000456(Subscription or purchase maybe required for full access)
Toward an inherently safer design and operation of batch and semi-batch processes: The N-oxidation of alkylpyridines
Alba Pineda-Solanoa, Lina R.Saenza, Victor Carreto, Maria Papadaki and M. Sam Mannan
05-Sep-2012
https://www.sciencedirect.com/science/article/pii/S0950423012000435(Subscription or purchase maybe required for full access)
Reaction calorimetric analysis of batch cooling crystallization processes: studies of urea in supersaturated water–methanol solutions
Xiaojun Lai, Kevin J. Roberts, Joakim Svensson and Graeme White
03-Feb-2011
https://pubs.rsc.org/en/content/articlelanding/2011/ce/c0ce00786b/(Subscription or purchase maybe required for full access)
The influence of reaction temperature on the oscillatory behaviour in the palladium-catalysed phenylacetylene oxidative carbonylation reaction
Katarina Novakovic,* Ankur Mukherjee, Mark Willis, Allen Wright and Steve Scott
01-Aug-2009
https://doi.org/10.1039/b905444h(Subscription or purchase maybe required for full access)
Isothermal decomposition of hydroxylamine and hydroxylamine nitrate in aqueous solutions in the temperature range 80–160 ◦C
LijunLiua, Maria Papadaki, Eleni Pontiki, Panagiota Stathi, William J. Rogers and M. Sam Mannan
15-Jun-2009
https://www.sciencedirect.com/science/article/abs/pii/S0304389408015112(Subscription or purchase maybe required for full access)
A New Autocatalytic Thioacetate-Enal Addition Reaction: A Michael Addition or Not?
Lijun Liu, Maria Papadaki, Elen Pontiki, Panagiota Stathi, William J.Rogers and M. Sam Mannan
15-Jun-2009
https://doi.org/10.1016/j.jhazmat.2008.10.023(Subscription or purchase maybe required for full access)
Thermal Behavior of Aqueous Solutions of Hydroxylamine During Isothermal and Isoperibolic Decomposition in a Closed System
Maria I. Papadaki, Eleni Pontiki, Lijun Liu, William J. Rogers, and M. Sam Mannan
19-May-2009
https://pubs.acs.org/doi/abs/10.1021/je9001366#(Subscription or purchase maybe required for full access)
A Practical Method For Stabilizing Lithiated Halogenated Aromatic Compounds
Thimma Rawalpally, Yaohui Ji, Ashish Shankar, William Edwards, Joshua Allen, Yong Jiang, Thomas P. Cleary, and Michael E. Pierce
15-Oct-2008
https://pubs.acs.org/doi/10.1021/op8001596(Subscription or purchase maybe required for full access)
Adaptive MIMO neuro-fuzzy logic control of a seeded and an unseeded anti-solvent semi-batch crystallizer
M. Sheikhzadeh, M. Trifkovic and S.Rohani
01-Mar-2008
https://www.sciencedirect.com/science/article/pii/S0009250907005179(Subscription or purchase maybe required for full access)
Kinetics Estimation and Single and Multi-Objective Optimization of a Seeded, Anti-Solvent, Isothermal Batch Crystallizer
M. Trifkovic, M. Sheikhzadeh, and S. Rohani
01-Feb-2008
https://doi.org/10.1021/ie071125g(Subscription or purchase maybe required for full access)
Fuzzy logic and rigid control of a seeded semi-batch, anti-solvent, isothermal crystallizer
M. Sheikhzadeh M. Trifkovic and S. Rohani
01-Feb-2008
https://www.sciencedirect.com/science/article/pii/S0009250907007993(Subscription or purchase maybe required for full access)
Utilising high throughput technologies for the determination of the reaction network of the L-proline catalysed aldol reaction
Katarina Novakovic, Mark J. Willis and Allen R. Wright
23-Jan-2008
https://doi.org/10.1007/s10098-007-0136-1(Subscription or purchase maybe required for full access)
Downloads
The following are a list of available downloads.
Chemical Synthesis Specifications
Process Safety and Scale Up Specifications
Testimonials
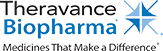
My experience with H.E.L dates since 2005. During these years H.E.L was the provider of the most important lab equipment with the help of which I developed many different API pharmaceutical processes in the companies l worked for including Merck, Pfizer, and Theravance. The versatility of the automated lab reactors (AutoLAB), the ease of use of and the accuracy of the TSu and Simular systems, as well as the flexibility of the PolyBLOCK made my work much easier and accurate. I would like to mention the great relationship I established with the service engineers and the sales people at H.E.L. With their help I was able to customize the software and the hardware of the equipment to our specific needs. This readiness to accommodate each customer’s specific needs gives H.E.L the edge over their competitors and makes them the preferred vendor for pharmaceutical lab equipment.