Scale-Up
From pilot plant to manufacture: Simulating plant conditions to inform safety control factors
Before the final scale-up to manufacturing, it is necessary to fully understand what safety control factors are required to mitigate the worst-case scenarios. The ability to fully simulate thermal runaway hazards under manufacturing conditions in the lab is a valuable way of understanding the process and ensuring the appropriate safety measures are planned and implemented prior to manufacturing.
Using an adiabatic calorimeter that utilizes low thermal mass (i.e., low Phi factor) test cells, such as the Phi-TEC II, means that very little of the heat produced during the reaction and runaway is consumed in warming up the test cell. This enables the conditions of a large-scale plant reaction to be emulated, with the maximum temperature attained (Tend) and the rate of pressure increase representative of what would be expected to occur during a plant-scale incident. The kinetic data obtained can be used to calculate the adiabatic temperature rise of the runaway (ΔTad,d) and the time to maximum rate of decomposition (TMRd). Unlike adiabatic calorimeters with a high Phi factor, the reaction rate is not suppressed by the high thermal mass of the test cell. So little to no data manipulation is required to compensate for heat losses to the test cell.
Comparing Reaction Scenarios
The Phi-TEC II also enables different reaction scenarios to be simulated and compared. In the example introduced earlier, the worst-case scenario that would release the most energy is the reaction of equimolar amounts of the alcohol and anhydride.
Temperature
Comparing the temperature results, it can be seen from the plot in Figure 11a that halving the amount of anhydride reduces the maximum temperature from over 200⁰C to 170⁰C and the time taken to reach that point. This change is further highlighted by considering the plot of the rate of temperature against temperature (the plot in Figure 11b), where the maximum rate reached drops from 4000⁰C/min to just over 1600⁰C/min when the amount of anhydride is halved.
These reactions were carried out using a Phi-TEC II on a low Phi-factor test cell and under adiabatic conditions. The parameters describing the exothermic event (MTSR, TMR, ΔTad, Tend) are highly representative of what would be expected to be observed in a plant-scale incident.
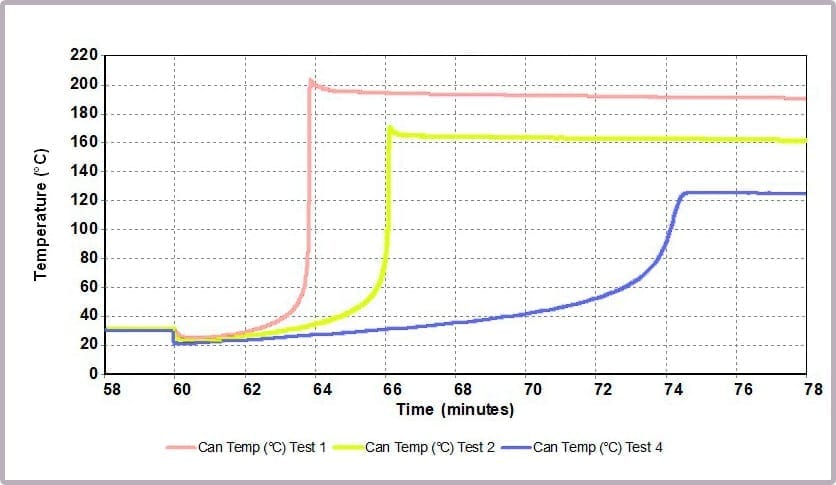
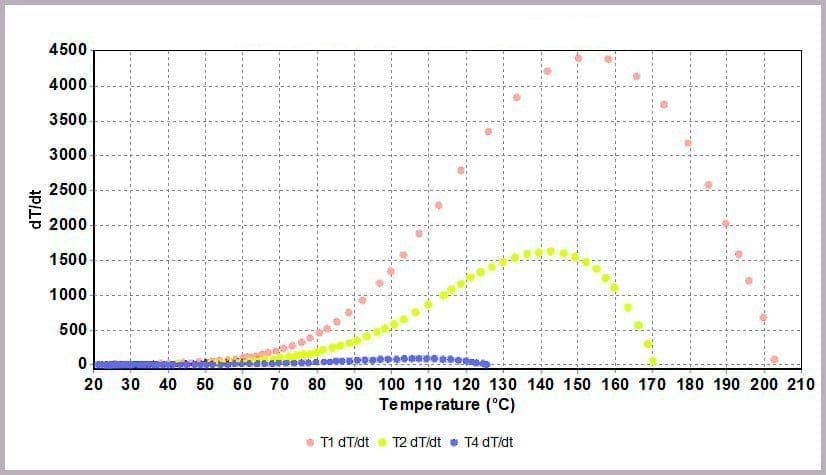
Pressure
As Figure 12 illustrates, a similar effect can be seen with the pressure data: when the level of anhydride is reduced, the maximum pressure reached is reduced, and the rate of pressure increase is slowed. In this example, the lower pressure rise directly results from the lower temperature.
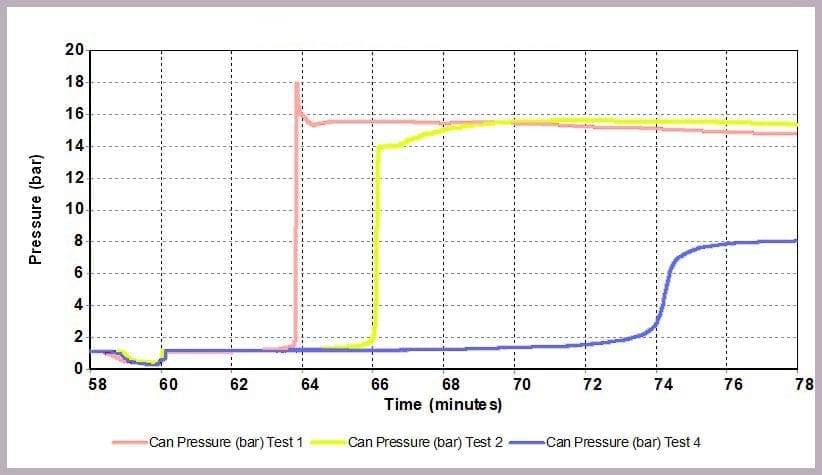
Safety Considerations
The data illustrates that for the worst-case scenario, it barely takes 3 minutes (after the chemicals come together) for the reaction to runaway to completion, and in the process:
- reaching a temperature of approximately 200⁰C
- a pressure of 16 bar
- with the rate of temperature increase peaking at 4000⁰C/min.
In contrast, by reducing the anhydride amount to a quarter that of the alcohol, the incident takes 12 minutes to reach the worst conditions, which are now reduced to:
- a maximum temperature of 125⁰C
- a maximum pressure of 8 bar
- a peak rate of temperature change of 150⁰C/min.
This is because the higher proportional levels of alcohol act as a thermal diluent, leading to the lower final temperature, lower final pressure, and a lower rate of increase in temperature and pressure observed.
Subsequently, this information enables the correct combination of reactor type and protection features to be selected, which could include the following:
- Emergency & evaporative cooling
- Quenching
- Controlled depressurization
- Vent sizing
Thus, directly comparing the impact of different operating scenarios enables the necessary safety controls to be selected upfront for the manufacturing plant.
Solutions
The Phi-TEC II is a more advanced type of adiabatic calorimeter, which supports using low Phi factor test cells. This capability means that very little of the heat produced during a reaction or thermal runaway is consumed in warming the test cell. As a result, the runaway rate is not tempered.
The measured rate of pressure increase and final temperature (Tend), along with the calculated Time to Maximum Rate (TMR) and adiabatic temperature rise (ΔTad), are representative of what would be expected to occur during a manufacturing scale incident. Thus, the Phi-TEC II enables the hazards to be thoroughly evaluated and explored, facilitating their mitigation before scale-up.
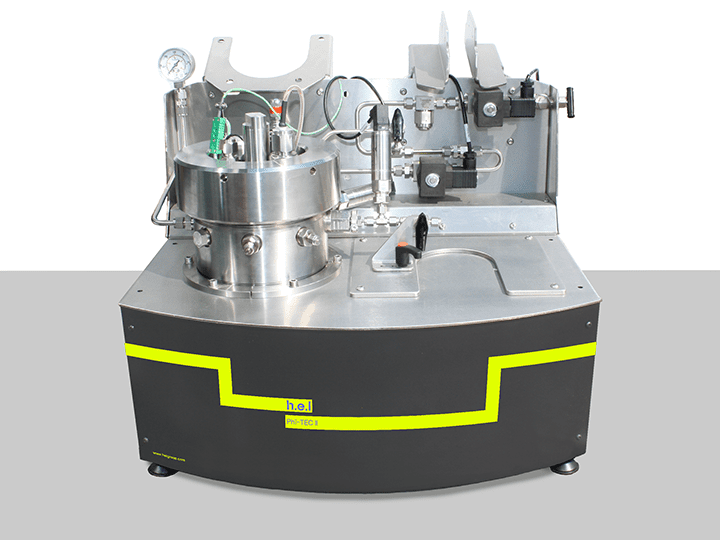
Phi-TEC II | Bench-top, low phi-factor, adiabatic calorimeter
The Phi-TEC II is an adiabatic calorimeter, which supports the use of low Phi-factor test ...