AutoLAB | Bench-Top Automated Reactor System
H.E.L’s fully customizable AutoLAB reactor platforms are designed, configured, and tailored to meet your specific process and application requirements. The modular and highly adaptable nature of the system enables the platform to evolve with your research and development interests.
Controlled by H.E.L’s powerful control software platform, the AutoLAB supports a diverse range of applications, such as:
- Polymerization
- Crystallization
- Synthesis
- High- and low-pressure reactions
- Process optimization
- Kilo-pilot/production plant scale-up
H.E.L Group has been developing bespoke reactor solutions for the chemical R&D community for more than three decades, so if your work requires functionality that is not listed, please contact us.
Publications
The following are a list of some technical publications which highlight the use of the equipment.
The role of adsorption in decomposition of dyes on TiO2 and N-modified TiO2 photocatalysts under UV and visible light irradiations
Kamila Bubacz, Beata Tryba, Antoni W. Morawski
11-Jun-2023
https://www.sciencedirect.com/science/article/abs/pii/S0025540812004771(Subscription or purchase maybe required for full access)
Measuring the Particle Packing of l-Glutamic Acid Crystals through X-ray Computed Tomography for Understanding Powder Flow and Consolidation Behavior
T. D. Turner*, P. Gajjar, I. S. Fragkopoulos, J. Carr, T. T. H. Nguyen, D. Hooper, F. Clarke, N. Dawson, P. J. Withers, and K. J. Roberts
12-May-2020
https://pubs.acs.org/doi/full/10.1021/acs.cgd.9b01515(Subscription or purchase maybe required for full access)
Measuring the Particle Packing of L-Glutamic Acid Crystals through X-ray Computed Tomography for Understanding Powder Flow and Consolidation Behavior
T. D. Turner,* P. Gajjar, I. S. Fragkopoulos, J. Carr, T. T. H. Nguyen, D. Hooper, F. Clarke, N. Dawson, P. J. Withers, and K. J. Roberts
12-May-2020
https://doi.org/10.1021/acs.cgd.9b01515(Subscription or purchase maybe required for full access)
Concentration and Separation of Heavy Rare-Earth Metals at Stripping Stage
Olga Cheremisina, Vasiliy Sergeev , Alexander Fedorov * and Daria Alferova
01-Dec-2019
https://doi.org/10.3390/met9121317(Subscription or purchase maybe required for full access)
Fast Method for Testing the Photocatalytic Performance of Modified Gypsum
Magdalena Janus, Kamila Zając, Clemens Ehm and Dietmar Stephan
15-Aug-2019
https://www.mdpi.com/2073-4344/9/8/693(Subscription or purchase maybe required for full access)
Improved Self-Cleaning Properties of Photocatalytic Gypsum Plaster Enriched with Glass Fiber
Kamila Zając, Magdalena Janus, and Antoni W. Morawski
22-Jan-2019
https://www.mdpi.com/1996-1944/12/3/357(Subscription or purchase maybe required for full access)
Empirical Kinetics Equation of the Synthesis of NTO in Nitric Acid
Yun Zhao, Shusen Chen, Shaohua Jin, Lijie Li, Xiaoyan Dong, Ruoting Xing, Zhiyan Lu, Qiaoe Liu, Wei Li, Bo Zhang
22-Jul-2016
https://onlinelibrary.wiley.com/doi/abs/10.1002/prep.201500334(Subscription or purchase maybe required for full access)
Methyl tetra-O-acetyl-α-d-glucopyranuronate: crystal structure and influence on the crystallisation of the β anomer
John A. Hayes, Kevin S. Eccles, Simon E. Lawrence, Humphrey A. Moynihan
01-Mar-2016
https://doi.org/10.1016/j.carres.2016.01.012(Subscription or purchase maybe required for full access)
Demonstrating the Influence of Solvent Choice and Crystallization Conditions on Phenacetin Crystal Habit and Particle Size Distribution
Denise M. Croker,*,† Dawn M. Kelly,‡ Danielle E. Horgan,‡ B. Kieran Hodnett,† Simon E. Lawrence,‡ Humphrey A. Moynihan,‡ and Åke C. Rasmuson†
30-Jan-2015
https://doi.org/10.1021/op500308x(Subscription or purchase maybe required for full access)
Reduction of CO2 by adsorption and reaction on surface of TiO2-nitrogen modified photocatalyst
B. Michalkiewicz, J. Majewska, G. Ka̧dziołka, K. Bubacz, S. Mozia and A. W. Morawski
01-Jan-2014
https://doi.org/10.1016/j.jcou.2013.12.004(Subscription or purchase maybe required for full access)
Cellulose-TiO2 nanocomposite with enhanced UV–Vis light absorption
Antoni W. Morawski, Ewelina Kusiak-Nejman, Jacek Przepio ́rski, Roksana Kordala, Juliusz Pernak
01-Mar-2013
https://doi.org/10.1007/s10570-013-9906-6(Subscription or purchase maybe required for full access)
Decomposition of 3-chlorophenol on nitrogen modified TiO2 photocatalysts
Sylwia Mozia, Kamila Bubacz, Magdalena Janus and Antoni W. Morawski
28-Nov-2011
https://www.sciencedirect.com/science/article/abs/pii/S0304389411014683(Subscription or purchase maybe required for full access)
ReactNMR and ReactIR as Reaction Monitoring and Mechanistic Elucidation Tools: The NCS Mediated Cascade Reaction of α-Thioamides to α-Thio-β-chloroacrylamides
David A. Foley, Christopher W. Doecke, Jonas Y. Buser, Jeremy M. Merritt, Linda Murphy, Marie Kissane, Stuart G. Collins, Anita R. Maguire, and Andreas Kaerner
26-Oct-2011
https://pubs.acs.org/doi/full/10.1021/jo201212p(Subscription or purchase maybe required for full access)
Crystal Polymorphs and Transformations of 2-Iodo-4-nitroaniline
Dawn M. Kelly, Kevin S. Eccles, Curtis J. Elcoate, Simon E. Lawrence, and Humphrey A. Moynihan*
01-Sep-2010
https://doi.org/10.1021/cg1001418(Subscription or purchase maybe required for full access)
In Situ Measurement of Solution Concentration during the Batch Cooling Crystallization of l-Glutamic Acid using ATR-FTIR Spectroscopy Coupled with Chemometrics
Antonia Borissova,† Shahid Khan,† Tariq Mahmud,*,† Kevin J. Roberts,† John Andrews,‡ Paul Dallin,‡ Zeng-Ping Chen,§ and Julian Morris
01-Dec-2008
https://doi.org/10.1021/cg7010265(Subscription or purchase maybe required for full access)
On-line monitoring of batch cooling crystallization of organic compounds using ATR-FTIR spectroscopy coupled with an advanced calibration method
Zeng-Ping Chen, Julian Morris, Antonia Borissova, Shahid Khan, Tariq Mahmud, Rado Penchev and Kevin J. Roberts
25-Nov-2008
https://www.sciencedirect.com/science/article/abs/pii/S0169743908002050(Subscription or purchase maybe required for full access)
Particle Shape Characterisation via Image Analysis: from Laboratory Studies to In-process Measurements Using an in Situ Particle Viewer System
Rui Fa Li Radoslav Penchev Vasuki Ramachandran Kevin J. Roberts* Xue Z. Wang Richard J. Tweedie, Andy Prior Jan W. Gerritsen, Fred M. Hugen
01-Jul-2008
https://doi.org/10.1021/op800011v(Subscription or purchase maybe required for full access)
Real-Time Measurement of the Growth Rates of Individual Crystal Facets Using Imaging and Image Analysis: A Feasibility Study on Needle-shaped Crystals of L-Glutamic Acid
X. Z. WangJ. Calderon De AndaK. J. Robert
01-Mar-2008
https://doi.org/10.1205/cherd06203(Subscription or purchase maybe required for full access)
Monitoring and Feedback Control of Supersaturation Using ATR-FTIR to Produce an Active Pharmaceutical Ingredient of a Desired Crystal Size
Vincenzo Liotta* and Vijay Sabesan
01-May-2004
https://doi.org/10.1021/op049959n(Subscription or purchase maybe required for full access)
Automated Measurement of Metastable Zones for Pharmaceutical Compounds
A.R. Parsons, S.N. Black and R. Colling
11-Mar-2003
https://www.sciencedirect.com/science/article/abs/pii/S0263876203723570(Subscription or purchase maybe required for full access)
Testimonials
AutoLAB
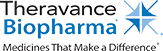
My experience with HEL dates since 2005. During these years HEL was the provider of the most important lab equipment with the help of which I developed many different API pharmaceutical processes in the companies l worked for including Merck, Pfizer, and Theravance. The versatility of the automated lab reactors (AutoLAB), the ease of use of and the accuracy of the TSu and Simular systems, as well as the flexibility of the PolyBLOCK made my work much easier and accurate. I would like to mention the great relationship I established with the service engineers and the sales people at HEL. With their help I was able to customize the software and the hardware of the equipment to our specific needs. This readiness to accommodate each customer’s specific needs gives HEL the edge over their competitors and makes them the preferred vendor for pharmaceutical lab equipment.
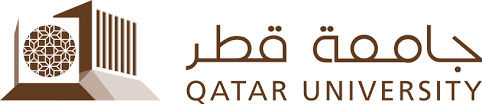
As a research active faculty member at Qatar University in chemical engineering with research fund that has a limited lifetime, I searched for specialist reactor suppliers around the world who would not only sell but also advise customers on their specific needs for the budget available. I was fortunate to select HEL in the UK and it started with an email query on a glass reactor for a tricky reaction system. That email was followed by a series of phone conversations to identify accurately my needs within my budget. I was particularly impressed by the speed of response and honest, impartial advice. I got what I wanted and when my research assistant encountered issues with the equipment during the warranty period, the spare parts were shipped very quickly, thus saving my research team precious time. HEL staff are professionals and trustworthy. As a research professor, I definitely recommend HEL for queries and purchases for intricate glass reactors for serious research work
Qatar University - Doha, Qatar