AutoMATE | Linear, Automated Parallel Synthesis Platform
The AutoMATE is a highly versatile, linear, automated parallel synthesis platform, for use in general chemical synthesis within R&D and process development, as well as more bespoke applications. As with the PolyBLOCK, the independently controlled reaction zones make AutoMATE especially well-suited for DoE campaigns and the platform’s modular design allows for an easy expansion of capabilities. In particular, the linear reactor design of the AutoMATE makes it ideal for more demanding applications, such as where multiple inputs and outputs are required.
Application modules that can be added include:
- Solubility/crystallization monitoring
- Online calorimetry option
- Catalyst screening
The platform supports reactor volumes of up to 500 ml per reactor and is equipped with adaptors to support a range of reactor types and sizes, including integration with H.E.L’s catalyst screening CAT reactor blocks. Additional functionality modules include:
- Liquid dosing and Sampling
- Gas feed
- Quick-connect refluxing option
- Quick-connect inerting solution
- pH monitoring
Publications
The following are a list of some technical publications which highlight the use of the equipment.
Understanding the agglomerate crystallisation of hexamine through X-ray microscopy and crystallographic modelling
Thai T.H. Nguyen, Parmesh Gajjar, Jun Sun, Robert B. Hammond, Darragh Murnane, Benjamin Tordoff, Erik Lauridsen, Philip J. Withers and Kevin J. Roberts
01-Feb-2023
https://www.sciencedirect.com/science/article/pii/S0022024822004687(Subscription or purchase maybe required for full access)
Economical and scalable synthesis of 6-amino-2-cyanobenzothiazole
Jacob R. Hauser1,2, Hester A. Beard1,2, Mary E. Bayana1,3, Katherine E. Jolley1,3, Stuart L. Warriner1,2 and Robin S. Bon*2,4
01-Sep-2021
https://doi.org/10.3762/bjoc.12.189(Subscription or purchase maybe required for full access)
Concentration and Separation of Heavy Rare-Earth Metals at Stripping Stage
Olga Cheremisina, Vasiliy Sergeev , Alexander Fedorov * and Daria Alferova
01-Dec-2019
https://doi.org/10.3390/met9121317(Subscription or purchase maybe required for full access)
Continuous formation of N-chloro-N,N-dialkylamine solutions in well-mixed meso-scale flow reactors
A. John Blacker and Katherine E. Jolley
01-Dec-2015
https://doi.org/10.3762/bjoc.11.262(Subscription or purchase maybe required for full access)
Comprehensive kinetic model for the dissolution, reaction, and crystallization processes involved in the synthesis of aspirin
David E. Joiner, Julien Billeter, Mary Ellen P. McNally, Ron M. Hoffman and Paul J. Gemperline
01-Feb-2014
https://doi.org/10.1002/cem.2605(Subscription or purchase maybe required for full access)
Rheological and Hydrogenation Study using a Flow Modified Sponge Ni Catalyst
J. Matt Farmer1*, Norman Marin-Astorga1, Bruce Lacey1, Steve McMahon1, and Chandresh Malde2
01-Jul-2013
https://www.researchgate.net/profile/Matt_Farmer3/publication/293653558_Rheological_and_Hydrogenation_Study_using_a_Flow_Modified_Sponge_Ni_Catalyst/links/56ba4bc608ae6a0040adeb24/Rheological-and-Hydrogenation-Study-using-a-Flow-Modified-Sponge-Ni-Catalyst.pdf(Subscription or purchase maybe required for full access)
Mixed-level supersaturated design application to a robustness study on an organic synthesis
Alice Croguennoc, Marc Frédéric, Magalie Claeys-Bruno, Roger Phan-Tan-Luu, Michelle Sergent
01-Apr-2012
https://doi.org/10.1016/j.chemolab.2012.01.005(Subscription or purchase maybe required for full access)
A novel technique combining high-resolution synchrotron x-ray microtomography and x-ray diffraction for characterization of micro particulates
David R Merrifield1, Vasuki Ramachandran1, Kevin J Roberts1, Wesley Armour2, Danny Axford2, Mark Basham2, Thomas Connolley2, Gwyndaf Evans2, Katherine E McAuley2, Robin L Owen
01-Sep-2011
http://dx.doi.org/10.1088/0957-0233/22/11/115703(Subscription or purchase maybe required for full access)
Crystal Product Engineering in the Seeded Cooling Crystallization of Adipic Acid from Aqueous Solution
O. Narducci,† A. G. Jones,*,† and E. Kougoulos‡
01-Jul-2011
https://doi.org/10.1021/op200029h(Subscription or purchase maybe required for full access)
Oligomerisation of linear 1-olefins using a chlorogallate(III) ionic liquid
Martin P. Atkins 1 , Kenneth R. Seddon 2 , and Małgorzata Swadźba-Kwaśny 2
01-Jun-2011
https://doi.org/10.1351/PAC-CON-10-12-03(Subscription or purchase maybe required for full access)
The influence of reaction temperature on the oscillatory behaviour in the palladium-catalysed phenylacetylene oxidative carbonylation reaction
Katarina Novakovic,* Ankur Mukherjee, Mark Willis, Allen Wright and Steve Scott
01-Aug-2009
https://doi.org/10.1039/b905444h(Subscription or purchase maybe required for full access)
Investigation of pH Effect on Hydrogenation Reaction of Dextrose to Sorbitol using a Mo promoted Sponge Ni catalyst
J. Matt Farmer*, Steven L. McMahon, and Bruce M. Lacey
01-Jun-2009
http://nacatsoc.org/21nam/data/papers/Paper2250.pdf(Subscription or purchase maybe required for full access)
Deactivation and regeneration of ruthenium on silica in the liquid-phase hydrogenation of butan-2-one
Haresh G. Manyar Daniel Weber Helen Daly Jillian M. Thompson David W. Rooney Lynn F. Gladden E. Hugh Stitt J. Jose Delgado Serafin Bernal Christopher Hardacre
01-May-2009
https://doi.org/10.1016/j.jcat.2009.04.013(Subscription or purchase maybe required for full access)
Study of System Thermodynamics and the Feasibility of Chiral Resolution of the Polymorphic System of Malic Acid Enantiomers and Its Partial Solid Solutions
Henning Kaemmerer,*,† Heike Lorenz,‡ Simon N. Black,§ and Andreas Seidel-Morgenstern
01-Feb-2009
https://doi.org/10.1021/cg8010508(Subscription or purchase maybe required for full access)
Development of Scaffold Synthesis for the Preparation of New Insulin-Like Growth Factor 1 Receptor Inhibitors
Ilaria Candiani, Germano D’Arasmo,* Franco Heidempergher, and Attilio Tomasi
01-Jan-2009
https://doi.org/10.1021/op8002536(Subscription or purchase maybe required for full access)
Polymorph and Particle Size Control of PPAR Compounds PF00287586 and AG035029
Billie J. Kline,* James Saenz, Nebojsˇa Stankovic ́, and Mark B. Mitchell
01-Mar-2006
https://doi.org/10.1021/op050176r(Subscription or purchase maybe required for full access)
Thermal Hazards of the Vilsmeier−Haack Reaction on N,N-Dimethylaniline
Marcus Bollyn
03-Nov-2005
https://doi.org/10.1021/op0580116(Subscription or purchase maybe required for full access)
Scale-Up of a Vilsmeier Formylation Reaction: Use of HEL Auto-MATE and Simulation Techniques for Rapid and Safe Transfer to Pilot Plant from Laboratory
Ulrich C. Dyer, David A. Henderson, Mark B. Mitchell, and Peter D. Tiffin
24-Apr-2002
https://pubs.acs.org/doi/abs/10.1021/op0155211(Subscription or purchase maybe required for full access)
Scale-Up of a Vilsmeier Formylation Reaction: Use of HEL Auto-MATE and Simulation Techniques for Rapid and Safe Transfer to Pilot Plant from Laboratory
Ulrich C. Dyer, David A. Henderson, Mark B. Mitchell, and Peter D. Tiffin
01-Apr-2002
https://doi.org/10.1021/op0155211(Subscription or purchase maybe required for full access)
Determination of the onset of crystallization of N1-2-(thiazolyl) sulfanilamide (sulfathiazole) by UV-Vis and calorimetry using an automated reaction platform
Joanne E. Anderson, Shane Moore, Frank Tarczynski and Dwight Walker
01-Aug-2001
https://www.sciencedirect.com/science/article/abs/pii/S1386142501004073(Subscription or purchase maybe required for full access)
Downloads
The following are a list of available downloads.
H.E.L has supplied us with high pressure reactors with automation which are working well and on the basis of this we are willing to recommend H.E.L for such systems.
Watson Pharma – PVT
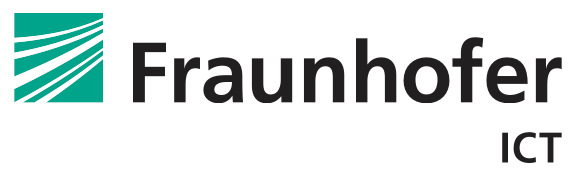
We received the ordered parallel high pressure system, everything is working well. Training and instructions were good and we are very satisfied.
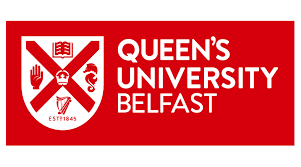
Three years ago we were developing a new catalytic process in collaboration with an industrial partner. It was essential to commission a reliable battery of glass reactors, built to our exact specification. We have decided to choose H.E.L’s AutoMATE II batch reactors array. We received professional advice, reactors built to specification, and a very thorough on-site training. The associated software is very intuitive and user-friendly. All issues occurring during the intensive use of the equipment were resolved quickly by the very helpful team at H.E.L. Last year, we have successfully progressed to a scale-up phase, for which we commissioned a custom-build AutoLAB reactor, with two exchangeable reaction vessels. Again, on all stages of ordering, manufacture and operation of the new reactor, the H.E.L staff were very helpful and made sure that their product was best suited to our needs.
Belfast, Northern Ireland - Queen’s University