Biomanufacturing is a complex process that requires balanced conditions for success—from selecting the right organism to determining the appropriate scale for development. Each step sets the stage for how you will maximize yield, volumetric productivity, and economic efficiency.
Gas Fermentation serves as a powerful tool in the energy sector. As industry leaders and startups focus on decarbonizing our planet through greener fuels like ethanol, biodiesel, and sustainable aviation fuel (SAF). Gas fermentation represents an emerging technology that promises to revolutionize decarbonization efforts.
By harnessing microorganisms, next-generation biofuels are produced from sustainable and more cost-effective feedstocks:
- Industrial waste
- Cellulosic biomass
- Syngas (synthetic gas)
- Algae-based resources
- Gases – H2, CO2, CO
Gas fermentation offers the ability to transform waste and greenhouse gases into high value fuels. However, gases are notoriously difficult to dissolve in fermentation media where microorganisms grow, resulting in:
- Low yields
- Limited gas transfer
- Poor reproducibility
- High production costs
- Low volumetric productivity
These 5 key gas fermentation considerations will help you maximize yield and volumetric productivity to achieve economic efficiency.
1. Select the Right Organism
Choosing the right organism to produce your desired biochemical is challenging. Bacteria, yeast, or algae are preferred over more complex cells since they offer shorter expression times, easier large-scale production, and more consistent batches. Today, manufacturers face one major challenge: “How do we make our microbes consume gas more efficiently?”
Genetic modification of microbial metabolic pathways can improve an organism’s productivity and molar yield by directing carbon and other elements toward desired bioproducts instead of biomass. This approach can also address viability risks posed by certain fermentation byproducts through targeted genetic modifications.
2. Consider the Feedstock Source
Manufacturers must weigh their feedstock costs against their bioproduct’s market value. Carbon dioxide from steel mills and cement production is becoming increasingly affordable for biomanufacturers. Hydrogen, syngas, and other gaseous carbon feedstocks are becoming—or will soon become—cheaper than traditional cultivated feedstocks like fructose. Today’s process design should consider these long-term outlooks to take advantage of tomorrow’s more affordable feedstocks.
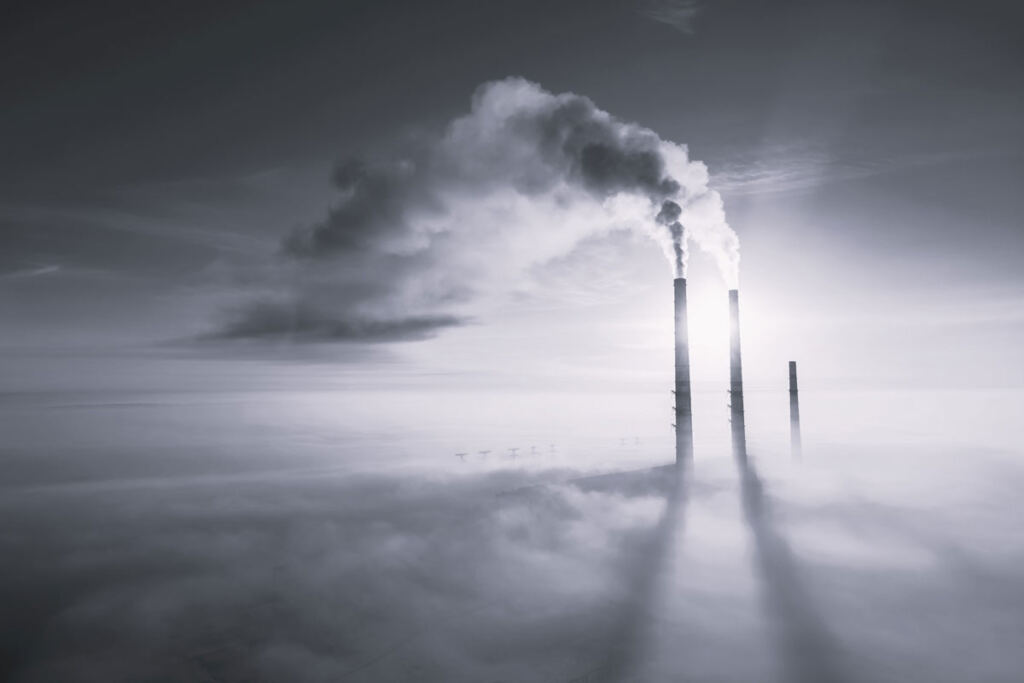
3. Design Scalable Processes
Small-scale experiments in parallel bioreactors with low volumes help establish rapid process characterization, but these conditions do not always translate directly to larger scales and often need adjustments. Exhaustive analysis, simulation, and modelling are essential to prevent plant-scale issues.
The operation mode is another crucial consideration. Fed-batch processing can extend the log phase, leading to increased biomass and primary metabolite production. While continuous fermentation runs more slowly, it reduces the need for frequent setup and cleaning—ultimately optimizing molar yield and overall efficiency.
4. Create Ideal Conditions
Overlooking bioreactor design often leads to increased costs and missed opportunities to improve process parameters. Critical parameters include temperature, pH, and dissolved oxygen. As the biofuel/SAF industry has begun utilizing gas fermentation. Gas transfer—the movement of gas into liquid—has emerged as a key bottleneck limiting substrate availability and volumetric productivity.
Pressurized reactor conditions address this challenge, as described by Henry’s law. Higher pressures in the bioreactor vessel enhance mass transfer from the gaseous to liquid phase, further promoting microbial growth and increasing volumetric productivity by increasing substrate availability. High-pressure, automated, parallel bioreactors represent an emerging technology enabling manufacturers to achieve greater gas transfer rates in their fermentation development.
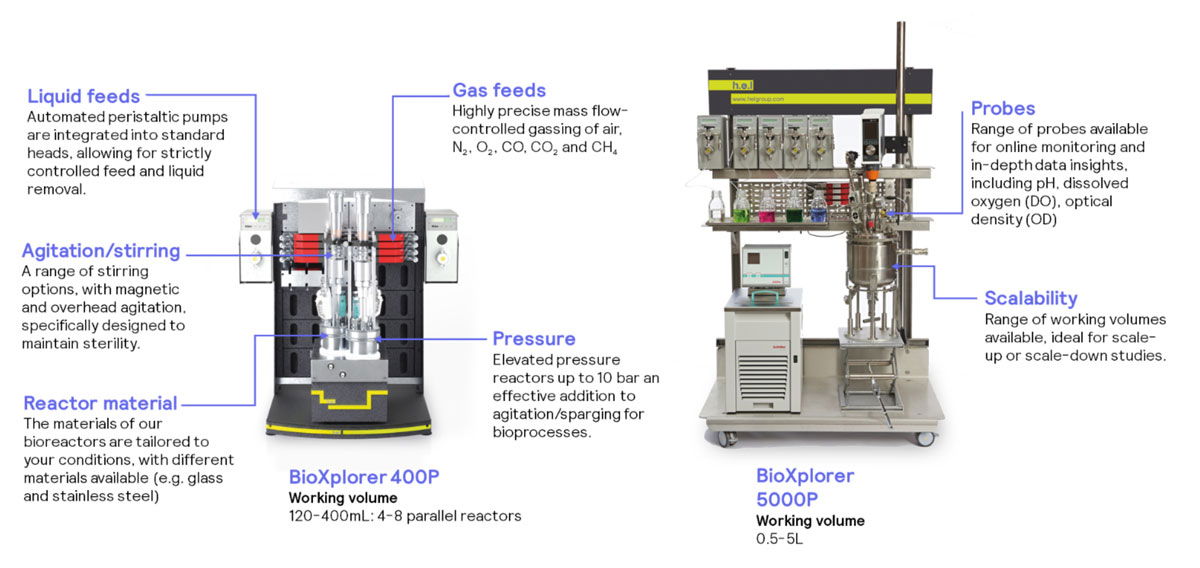
5. Automate Process Controls
Maintaining appropriate oxygen and feedstock gas levels is fundamental throughout the process. Automation and strict control ensure conditions remain ideal for the fermentation of biofuels/SAF, ensuring higher yields and increased productivity while avoiding costly human error.
Powerful software with recipe design, extensive parameter controls, and built-in safety shutdowns enables scientists to automate and run short—to long-term fermentations while maintaining the fine balance of biological reactions.
With these strategies in place, researchers and manufacturers can overcome the challenges of fermentation and achieve cost effective production, producing high value products from sources such as Syngas and CO2