Assessing the suitability of H.E.L’s BTC-500 for small battery testing
Alexander Gregory Philpotts, Dr. Mario Toubes-Rodrigo
H.E.L Group, Unit 2 Centro, Boundary Way, Hemel Hempstead, HP2 7SU, UK
Table of Contents
Abstract
The constant pressure from the market to create more powerful batteries can result in unsafe situations. As a consequence, battery testing is crucial to obtain better batteries that can be operated safely. Adiabatic calorimetry is an incredibly powerful tool for identifying the temperature values at which a battery can be operated. The characterization of events, such as thermal runaways, can help identify the risks and establish mitigation strategies. However, choosing the right calorimeters can prove challenging because they are not sensitive enough for small batteries or cannot withstand battery failures. In this application note, we tested a very small battery (LP103035) in a large calorimeter (BTC-500). The exotherm was detected using a ramp test (not adiabatic) starting at 77 °C, followed by another two thermal events. Using adiabatic conditions, in a Heat-Wait-Search mode, we detected that the thermal runaway started at 139.2°C and finished at 195.9 °C, representing an adiabatic temperature rise of 56.7 °C and covering all the exotherms detected in the ramp mode. The results from this study proved the suitability and sensitivity of BTC-500, even in very small batteries. However, for those conditions, using small and more sensitive calorimetry, such as BTC-130, can offer better results.
Introduction
There is constant pressure to produce higher-capabilities batteries: larger storage, faster charging times, longer lifespans… However, as batteries become more and more powerful, so are the risks associated with them. Lithium-ion batteries (LIBs) dominate the market, taking over 90% of the total quota. However, a long stream of fire-related accidents have been linked to this type of storage device. As a result, safety testing remains paramount in the development phase.
One of the main risks associated with LIBs is the susceptibility of some of their components (electrodes and electrolytes) to decomposition reactions. Decomposition reactions are oftentimes exothermic and can result in a positive feedback loop, in which the reaction accelerates because of energy released by the reaction (thermal runaways).
Adiabatic calorimetry is an incredibly powerful tool for the detection of such events. Being able to insulate the reaction from the environment, avoiding heat exchange with their surroundings allows for in-depth characterization of the exotherm. Information such as the temperature at which the thermal runaway starts and the heat release are critical to determining the safe operational limits and creating mitigation strategies.
In this application note, we test the limits of a BTC-500, a large-scale battery testing adiabatic calorimeter, using small pouch batteries (LP103035).
Material and methods
LP103035 pouch batteries (LiPol Battery, China) were used in this study. They were stripped of protection circuit modules and cables/wires, leaving bare tabs. This battery had a nominal voltage of 3.7V (100% charge) and a rated capacity of 50 mAh (50 mAh min to 54 mAh type). The dimensions of the battery were 30 mm x 35 mm x 10 mm. Calibrations were performed in an aluminium plate, replicating the measurements of the pouch (30 mm x 35 mm x 10 mm)
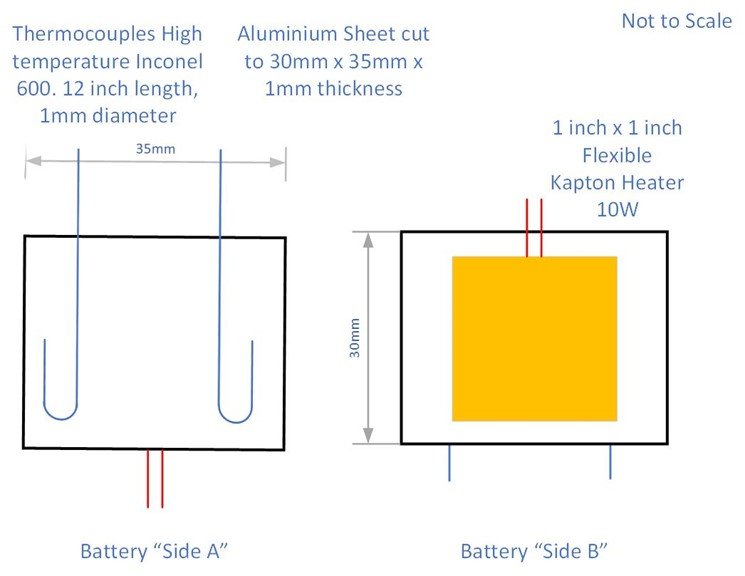
Figure 1. Diagram representing thermocouples and heater set up but the tests in this study.
Battery and calibration plate setup
Inconel 600 thermocouples (30.5 cm length, 1 mm diameter) were placed and secured with Kapton tape on the same side of the battery through all tests, as shown in Figure 2. Samples were covered in aluminium tape to ensure uniform heat losses. For the Heat-Wait-Search methodology and its calibration, a Kapton heater (2.54 cm x 2.54 cm) was secured using Kapton tape on the opposite side. (Figure 1).
Batteries were tested in a BTC-500, a floor-standing adiabatic calorimeter (H.E.L Group, Hemel Hempstead, UK). LP103035 and calibration dummies were placed at the very center of the calorimeter, suspended from the top using three stainless steel 2mm diameter ropes, an S-hook, and the thermocouples (Figure 2).
Ramp test
A temperature ramping test was performed. The temperature increased at a rate of 1 °C/min up to 400 °C guard heater (oven) temperature with a cut off of 300 °C can (sample) temperature. The conditions for the plan are shown in Fig 3.
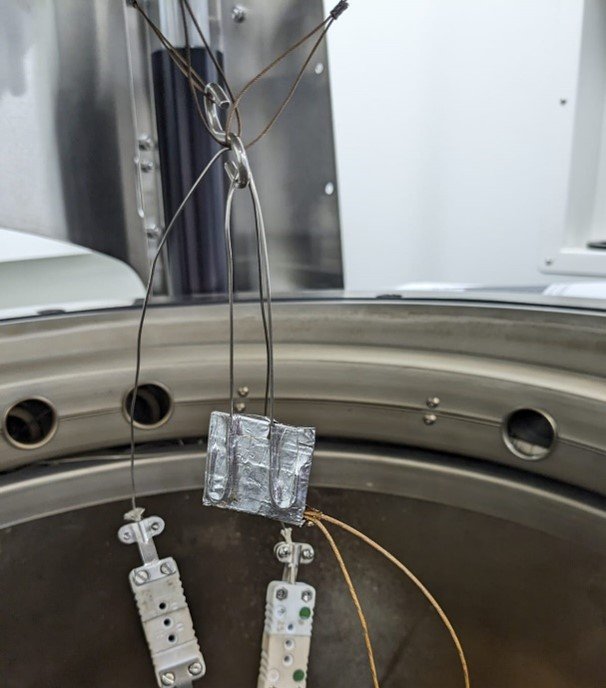
Figure 2. Battery suspended from the lid of a BTC-500 using an S-hook. The battery was covered with foil to ensure a thorough heat distribution from the heater. At the bottom, the thermocouples used for temperature tracking can be seen connected to the battery.
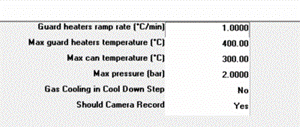
Figure 3. Screenshot from H.E.L WinISO showing ramp test parameters.
Heat-wait-search (HWS) test
A Heat Wait Search Test was run and the conditions for the plan are shown in Figure 4. In addition to this, the heat-up steps were time-limited to no less than 30 minutes to ensure the system reached a thermal equilibrium.
Results and Discussion
Ramp Test
The ramp test was used as a screening test for samples to get an onset temperature quickly and accurately. As this test is not an adiabatic test, the accuracy of the Heat Loss Compensation (HLC) did not affect this test, allowing it to be a good comparison (Figure 5).
The results showed three clear events occurring. All three appear exothermic, with each releasing more heat than the last. The first had a small but noticeable effect on the vessel pressure. Plotting the derivatives of sample temperature against sample temperature, the onset temperature was identified at 77 °C, 134 °C, and 168 °C, respectively. Plotting the pressure derivative against sample temperature revealed a clear change during the first and second exotherms. The third exotherm has less of a clear change in pressure. It should be noted that the system was reading pressure to the 3rd decimal place and is at the limits of detection, as seen from background noise (Figure 6).
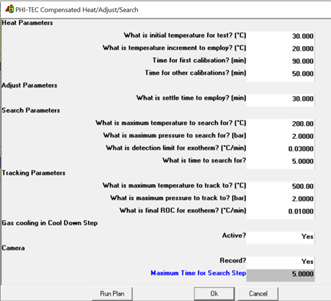
Figure 4. Screenshot from H.E.L WinISO showing ramp test parameters.
Calibration for HWS
Characterization of the heat loss mechanism of the battery across the temperature range used in the test is necessary in order to run an adiabatic test.
Table 1. Heat Loss Compensation terms
Quality Factor | 1.03 |
Convection Factor | 0.00018 |
Convection Exponent | 0.7 |
Conduction Factor | 0.412 |
Radiation factor | 0.57 |
Fixed Offset correction | -0.3 |
(unitless) used in the calibration test.
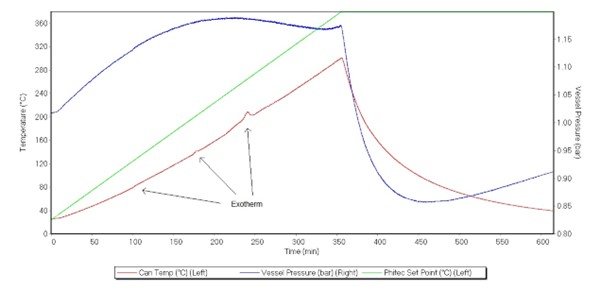
Figure 5. Ramp test of LP103035 battery, displaying the vessel pressure (blue, right axis), can temperature (red, left axis), and oven temperature (green, left axis). Exotherms were labelled.
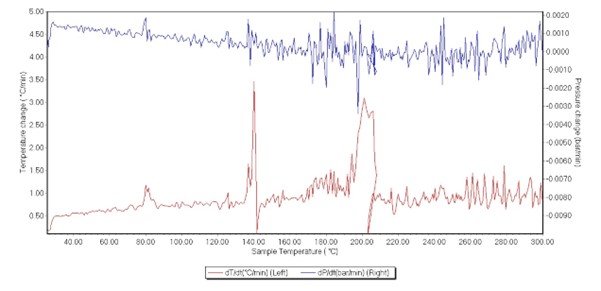
Figure 6. Temperature derivative (dT/dt) (red) and pressure derivative (dP/dt) (blue)
For more understanding on the use of these HLC terms, and the equation that is used to calculate the “guard heater advance”, please refer to the Phi-TEC I “HLComp” Manual.i
Longer heat up steps and longer calibration times were used than is standard. This was to allow the system to reach thermal equilibrium. The HLC terms were adopted for the HWS test.
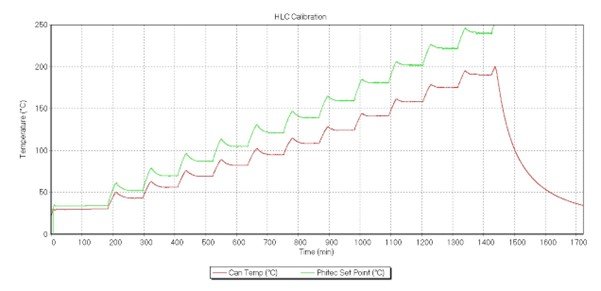
Figure 7. Heat Loss Compensation calibration using an aluminium sheet with the same geometry as the sample. In red, sample temperature, and in green oven temperature, both in °C.
Heat Wait Search (HWS)
The HWS is a adiabatic test used to measure exothermic activity in an adiabatic environment. The results for the HWS are shown in Figure 8.
An exothermic event was detected at 139.2 °C and ended at 195.9 °C, representing an adiabatic temperature rise of 56.7 °C (Figure 8). When comparing it against the ramp data, this includes the second and third exotherms (Figure 5). The exotherm likely produced enough heat to trigger the second exotherm; the resulting data represents both. This was representative of how the battery would behave in a real-life situation where it is not able to release its heat effectively.
The onset temperature of the exotherm is 139.2 °C (Figure 8), compared to the onset temperature in the ramp test of 134 °C (Figure 5). The preceding “heat up” skipped this temperature slightly as the system was set to 20 °C increments. The HWS could be repeated with smaller increments, or another test, the “HWS single exotherm” test, can be run at 134 °C. This is an adiabatic test that is only at one temperature rather than a range of temperatures in the HWS. Nevertheless, this would have an insignificant impact on the adiabatic temperature rise, as the amount of heat released by the battery would be constant, only the start and end temperatures would be altered.
The exotherm at 77 °C detected during the ramp is likely so small that this is obscured during a heat-up. Again, an HWS with smaller increments or an HWS single exotherm test can be performed at this temperature.
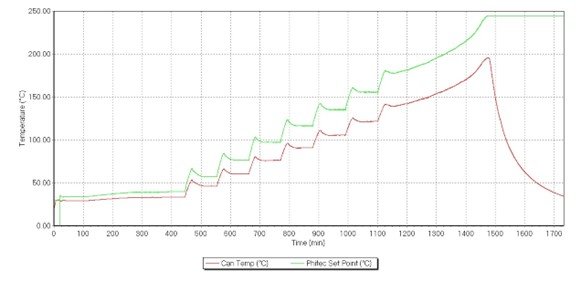
Figure 8. Heat-wait-search (HWS) test of a LP103035, showing the sample temperature (in red, °C, and the oven temperature (in green, °C)
Conclusion
In this study, we assessed the suitability of the BTC-500 for testing small battery samples; despite BTC-500 being designed for larger batteries, our study demonstrated its adaptability to effectively control and evaluate smaller cells.
The ramp test served as an initial screening method. This gave us an initial insight into the exothermic behavior of the battery. The calibration enabled us to characterize the heat losses required for performing an HWS. The HWS enabled us to test the battery in a real-life setting, getting the adiabatic temperature rise of the sample.
In conclusion, this study underscores the importance of adiabatic calorimetry in battery safety testing and demonstrates the adaptability of the BTC-500 for evaluating small battery cells. Future research could focus on refining environmental control to further enhance accuracy and reproducibility, as well as evaluating the battery’s thermal mass and performing electrical and mechanical stress tests.
References
- H.E.L. Heat Loss Compensation Software Manual. Borehamwood : H.E.L Group, 04/09/2013. Vol. 1, 1.