Scale-Up
Why Adiabatic Calorimetry?
Large-scale reactors, like those found in manufacturing and pilot plants, behave pseudo-adiabatically – i.e., very little heat is lost to the surroundings. This contrasts with the smaller vessels used in laboratories, where heat loss is much more significant. This poses a hazard on scale-up, as heat generated from a reaction will be retained within the system – at best, requiring more plant cooling and, at worst, triggering a thermal runaway. This is due to the decrease in surface area to volume ratio in larger vessels, which provides less area for heat dispersal.
Adiabatic calorimeters mimic these large-scale vessels in small-scale systems. An adiabatic calorimeter will eliminate increasing heat losses with the application of carefully modeled and controlled system temperature increases.
Broadly speaking, there are two types of adiabatic calorimeters that find use at different stages of scale-up. The more common, classic acceleration rate calorimetry or “ARC”-style adiabatic calorimeter, such as the Phi-TEC I, can be used earlier in the scale-up process as an additional reaction screening tool. The test cells used normally have a larger thermal mass than the reactants they contain and are described as having a high Phi (Φ) factor. A Phi factor is defined as [1]:
As a result, the data from these high Phi-factor test cells must be recalculated before the results can be scaled up.
However, the second type, such as the Phi-TEC II, uses low thermal mass test cells. This allows the Phi-TEC II to more closely simulate plant-scale adiabatic runaways and generate data that can be used to define the safety measures that will need to be put in place on a manufacturing scale. As such, it tends to be used at the final stages of scale-up, when all other safety bases have been explored, but the only possible route is to allow the runaway to progress.
The classic “ARC”-style adiabatic calorimeter sits between the basic screening tools used earlier in process development and the advanced, low Phi-factor adiabatic calorimeter used in the final scale-up. Accordingly, experiments undertaken with the Phi-TEC I deliver additional information on thermal hazards to that obtained from the TSu. Likewise, the Phi-TEC II provides even richer process information. The Phi-TEC I is often used when the initial screening tests identify that a reaction is highly exothermic and/or carries a significant risk of over-pressurization. A more detailed characterization of the potential thermal runaways is required in these cases.
The Phi-TEC I allows the process safety chemist to carry out a detailed sample evaluation by studying the exotherm under adiabatic conditions, thus delivering an accurate determination of the:
- The onset temperature of any decompositions or side reactions (Td)
- The adiabatic temperature rise of any secondary thermal runaways (ΔTad,d)
- Time to Maximum Rate of the secondary thermal runaway (TMRd).
- The pressure increase during the decomposition or side reactions
Some of these parameters are illustrated schematically in Figure 10.
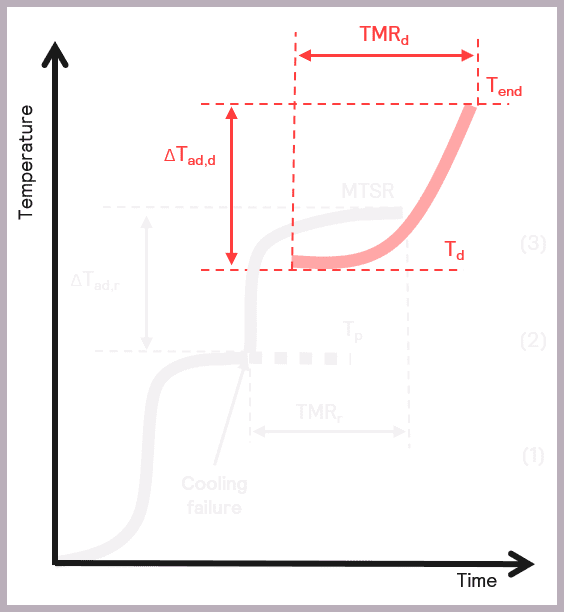
The Phi-TEC I ensures that exothermic events are fully tracked and pseudo-adiabatic conditions are maintained by providing a direct measurement of the sample temperature, coupled with a rapid guard heater response time to thermal changes,
However, it is important to realize that the rate of pressure change and maximum temperature determined are unlikely to represent anything that happens at the process scale, particularly if the reaction is gas-generating and volume becomes important. Representative values for these parameters can be obtained using low Phi factor test cells for adiabatic testing.
Solutions
When scaling up a process, accurate knowledge of an exothermic event is
vital to ensure the magnitude of the thermal runaway risk is fully understood. The Phi-TEC I provides a direct measurement of the sample temperature with a rapid response to thermal changes. It accurately tracks exothermic events and maintains the required adiabatic conditions.
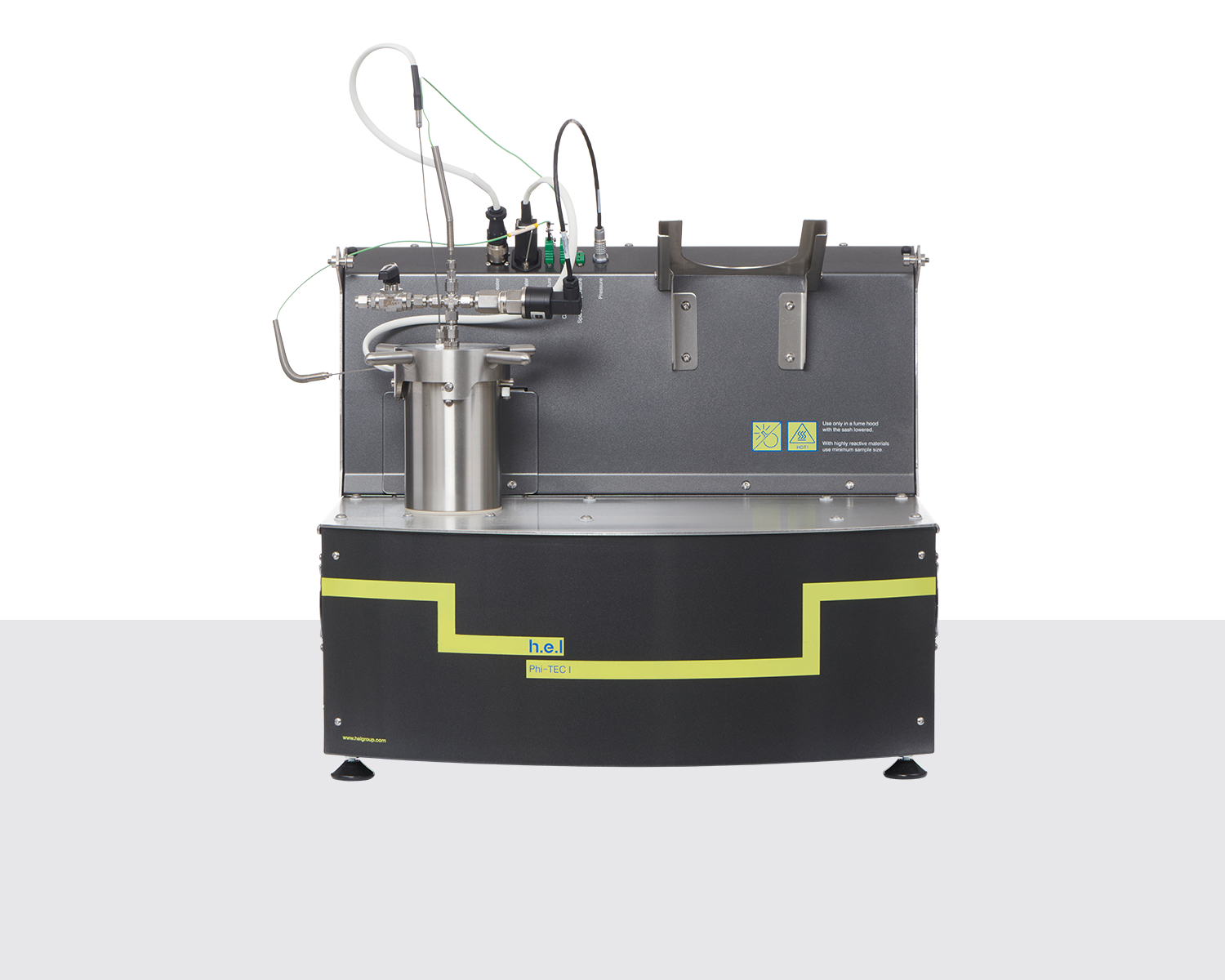
Phi-TEC I | Bench-top, adiabatic calorimeter
The Phi-TEC I is an adiabatic calorimeter that enables the characterization of thermal run...
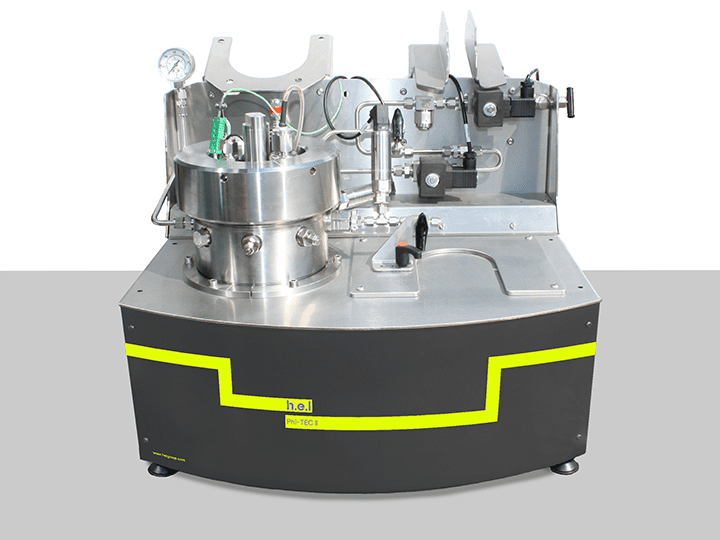
Phi-TEC II | Bench-top, low phi-factor, adiabatic calorimeter
The Phi-TEC II is an adiabatic calorimeter, which supports the use of low Phi-factor test ...