In the race to try to meet market demands, industries are pressured to increase their production. To achieve this, scale-up phases are fundamental. However, the path from lab-scale research to full-blown industrial is replete with challenges. This journey involves a series of steps, starting with the identification of suitable reactants that will produce the molecules of interest and understanding the process by which the desired chemical reaction occurs. The second stage of the scale-up process involves acquiring in-depth knowledge of the impact that physicochemical parameters have on the reaction itself. Temperature, pH, pressure, and agitation are some of the variables that need optimization at this stage, aiming to increase the process’ productivity. Safety is another aspect that requires plenty of attention. Understanding the chemical reaction is not limited by the parameters at which the reaction happens optimally but also the potential side products or secondary reactions. These undesired effects can result in hazardous conditions, such as sudden temperature or pressure increases.
The scale-up process can be described as the transition from small laboratory-scale experiments to large-scale industrial manufacturing. The main objective of this process is to facilitate the efficient and safe production of desired products at a scale high enough to meet the market demand. However, small benchtop reactors provide fundamental benefits for this process. This blog post aims to show how.
1. Thermodynamics and Kinetics characterization
As mentioned in the previous section, the deep characterization of the reaction is fundamental, helping us to understand the optimal and safe conditions for the process. One of the parameters that is likely to change the most during the scale-up process is mixing. Effective and efficient mixing allows for homogeneous conditions and avoids the formation of pockets in the reactor of high concentrations of reactants or products, which can result in precipitation events. Additionally, effective mixing avoids the formation of temperature gradients that would reduce the yield of the reaction and potentially generate hazardous situations.
Small benchtop reactors can be finely controlled and monitored. As a result, they are perfectly capable of simulating suboptimal mixing conditions that are likely to occur in large reactors. The results of this kind of analysis will throw light on the impact on productivity and the potential formation of by-products.
2. Increasing Process Reproducibility
Consistency is one of the critical considerations when designing an industrial process. A degree of variability can always appear due to several factors (e.g. raw material). This can result in anomalies in the results, leading to wrong assumptions. To avoid such situations, it is fundamental that the design of industrial processes is built upon robust statistical data. The only way to obtain statistically significant data is by repeating the experiment.
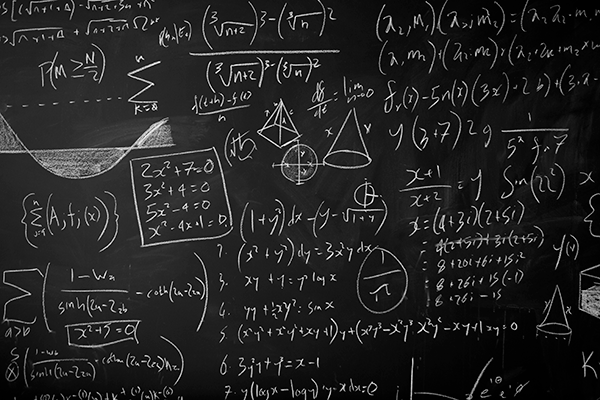
Small benchtop reactors are a very powerful tool at this stage. On the one hand, their small footprint means that various reactors can be operated in smaller spaces, diminishing potential variation. Additionally, their smaller size means that smaller quantities of chemicals are needed, decreasing the costs of this phase. Automated parallel reactors reduce the potential for human error, thus increasing the reliability of the data obtained.
3. Raw material and product handling
During the first stages of the process development pipeline, high-purity reactants are routinely used. This allows for the characterization of the chemical reaction and the mechanisms that control it. However, high-purity reactants are costly and not viable at a larger scale. Using lower purity reactants can bring some issues into the pipeline, first and foremost, the reduction of the efficiency of the process. Additionally, some of the potential substances that the raw material contains can result in additional reactions. This can be a particular issue when storing either raw materials or by-products. These chemicals might be susceptible to decomposition reactions, which can have some intrinsic risks.
Different raw materials can be tested using lab-bench reactors, allowing for the interpolation and extrapolation of yields after a thorough characterization of the material used in the reaction. Secondly, using smaller quantities can reduce potential risks, as the heat released during decomposition scales up with the amount of material.
4. Safety considerations
The majority of chemical reactions used in industry are exothermic. This means that heat is released into the system as the chemical reaction progresses. The main consequence is the increase of the temperature inside the vessel. Thermal runaway processes can occur if the chemical reaction rate increases as the temperature rises. These are characterized by their positive feedback loop behavior: the higher the temperature, the more energy is released, and so on. As mentioned in the previous section, the amount of heat generated by reactions is proportional to the amount of mass.
Testing for safety in smaller vessels has a number of advantages, some of them mentioned in this blog post (e.g. cost reduction). Additionally, small volumes have a larger exchange surface, which allows for quicker heat exchange with the surroundings, and thus, the temperature inside of the vessel does not reach dangerous levels. However, this might be a downfall, as it would not replicate the conditions that could occur at larger scales, as larger vessels are not as efficient at dissipating heat. This is when the phi factor is fundamental, allowing for the correction of this value.
5. Pilot testing
Transitioning to industrial scale is always a giant step that can come with great benefits. Nevertheless, if the scale-up process is not performed appropriately, it can create significant costs and delays. One of the main issues that larger vessels have is that the control capacities inside reactors containing thousands of liters are not as efficient as in small volumes.
Small and medium size pilot testing experiments offer better controlled environments, allowing for fine-tuning of the process parameters and a better understanding of the process. This information is fundamental for the effective design of the reactor and optimization of the operation methodologies.
Bridging the benchtop to industrial transition
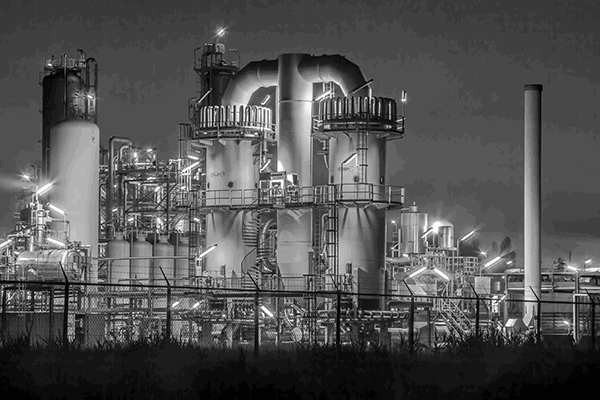
Scale-up processing is a complex multi-step journey that will take chemical reactions from benchtop small vessels in a laboratory to large reactors inside industrial plants. This process involves optimizing different parameters to increase productivity while maintaining safe operational conditions. A seamless transition characterizes a successful scale-up phase, but it is fundamental to acquire a deep understanding of the reaction dynamics to achieve this objective.
The only way to attain such knowledge is through robust statistical data obtained through replication, the appropriate handling of materials, and the development of adequate safety measures while maintaining the economic feasibility of the process. The fine-tuning capabilities of small benchtop reactors pose as a fundamental tool for this purpose, shedding light on potential challenges that might arise during scale-up, bridging the benchtop and industrial scales.
With the pressure to meet the market demand, industries cannot afford costly mistakes during the scale-up phase. Therefore, ensuring a smooth transition is not exclusively about meeting the production target but making it sustainable, safe, and economically viable. By leveraging the insights gained from small-scale reactors, industries can confidently transition to industrial processes, ensuring that their processes reach the market efficiently and adhere to the highest safety standards.
Watch our video on this here:
Resources:
https://www.sciencedirect.com/science/article/pii/S2590140021000101
https://helgroup.com/applications/customizable-solutions-for-chemical-synthesis/
https://helgroup.com/applications/critical-considerations-in-process-safety/
https://helgroup.com/blog/process-safety-blog/the-unsung-hero-how-the-phi-factor-shapes-calorimetry/