Creating Process Safety Data Sheets for Safe Scale-Up in Pharma/API Production
Mario Toubes-Rodrigo1
1 H.E.L Group, Unit 2 Centro, Boundary Way, Hemel Hempstead, HP2 7SU, UK
Table of Contents
Introduction
The pharmaceutical industry faces unique challenges as it progresses from R&D bench-scale to plant production, moving from milligram quantities to tons. High-quality active pharmaceutical ingredients (APIs) must be produced in a cost-effective fashion while complying with regulatory requirements for safety and consistency. As such, process safety remains a fundamental pillar to meet these demands and mitigate potential hazards linked to industrial production. In this article, we explore best practices and state-of-the-art tools that can be used to produce Process Safety Date Sheets (PSDS).
Why Process Safety Testing is Critical?
Identifying and managing hazards that might occur at all stages of the industrial process is essential. A proactive approach to Process Safety avoids potential incidents with potentially catastrophic consequences, as we have witnessed in well-known industrial accidents. Among the causes that resulted in this type of accident, thermal runaway-derived explosions, dust explosions, or unanticipated chemical reactivity are common. Comprehensive safety testing is a powerful tool that helps companies understand the behavior of their material under different conditions. The compiled results will, in turn, guide safe production practices and ensure regulatory compliance. In practice, this process involves applying a combination of assessments at various stages, starting with basic tests, like thermal screening, using instruments such as H.E.L’s TSu. As the process moves from the R&D lab and bench-top scale towards the kilo lab, pilot plant, and full-scale manufacturing, more advanced techniques, such as isothermal calorimetry, are required. Each step adds layers of insight, from initial thermal stability to explosivity and reaction calorimetry, providing scientists with the data required to guarantee process integrity and safety.
Process Safety Testing Techniques
Companies need to use a combination of techniques to support safer scale-up. Each tool provides different information and perspectives required to gather critical safety data.
- Thermal screening: This technique evaluates changes in the thermal behavior and pressure of materials, using minuscule amounts of material. Thermal screening provides onset temperatures, thermal rise rates, and safe temperature thresholds critical for scaling reactions and material storage safely.
- Adiabatic calorimetry: This type of analysis tracks the accumulation of heat linked to a reaction, preventing heat loss to the surroundings. It allows for precisely recording temperature changes, which can lead to explosions. Adiabatic calorimetry helps to characterize materials and reactions accurately and efficiently.
- Isothermal calorimetry: Understanding the kinetics of reactions enables researchers and engineers to acquire critical safety parameters, such as the adiabatic temperature rise, maximum temperature of a synthesis reaction (MTSR), and time to the maximum rate (TMR). The accurate characterization of these values remains essential for preventing thermal runaway incidents during scale-up.
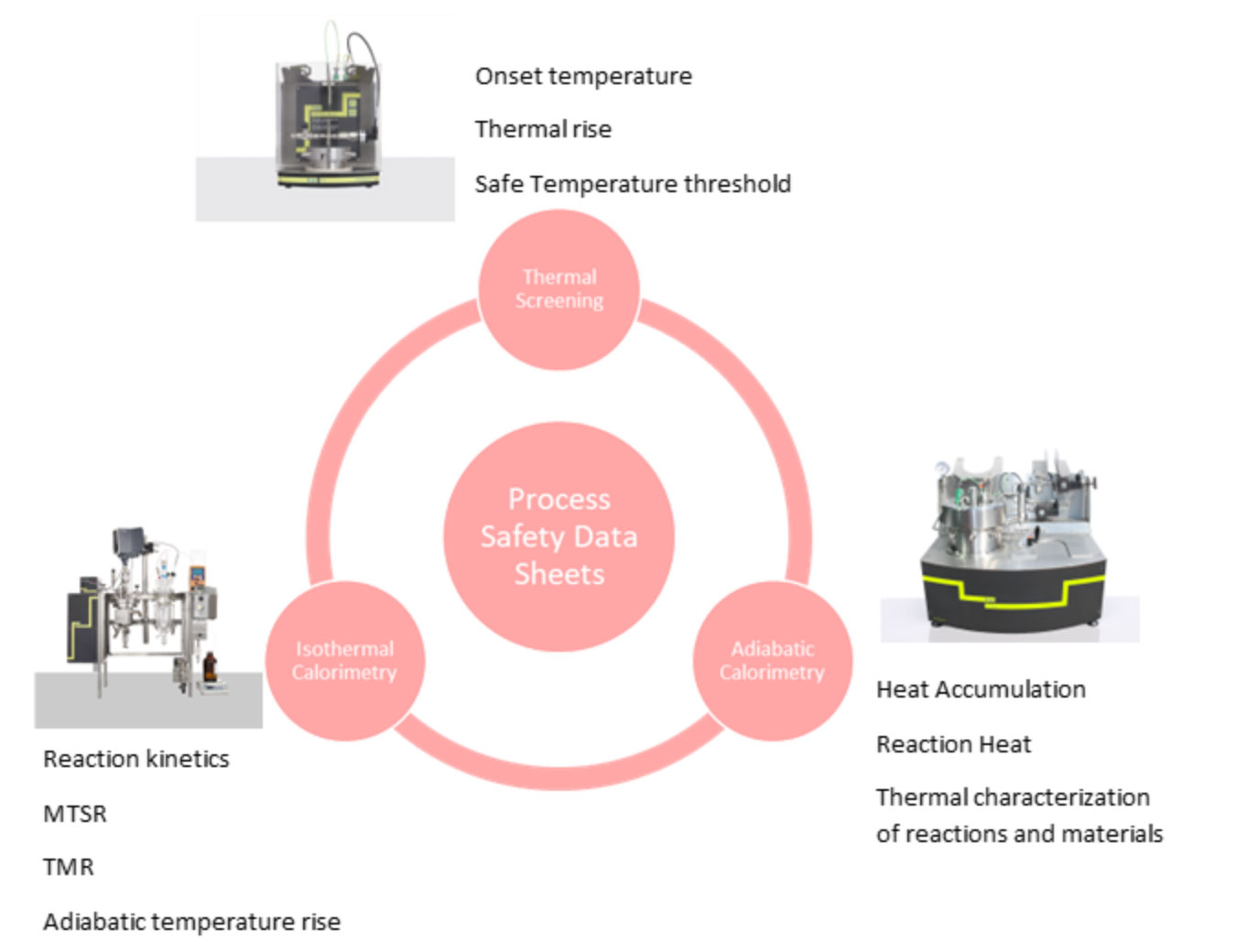
Data Utilization of Process Safety
The combination of these techniques can be summarized and written up into a Process Safety Data Sheet (PSDS), a compilation of testing data into a comprehensive safety profile for each project. A reliable PSDS will include all critical parameters for each stage of the process and outlines safe temperature ranges, potential hazards, and control requirements. This allows for categorizing the process safety, from safest to the riskiest, and provides a straightforward way to identify necessary safety measures and implement mitigation strategies when required. When processes are predicted to be in the higher categories of the classification, further analysis needs to be undertaken. These might include process hazard assessments and layers of protection analysis, with the aim to ensure that potential risks are controlled before moving into larger scales. The combination of different calorimetric analyses with other possible techniques, ensures the production of robust PSDS which enables companies to make informed decisions on process adjustments and safety protocols.
Practical Implications for API Manufacturing
The implementation of robust safety protocols remains paramount for API manufacturers. Accurate calorimetry data contributes to the design of efficient cooling and agitation measures, plans for waste management, and minimization of safety hazards. For example, the characterization of adiabatic temperature rise can help predict the cooling capacity necessary to control a reaction safely. Similarly, the detection and measurement of gas evolution is critical for assessing the ventilation and gas handling needs. The utilization of advanced thermal analysis and calorimetry techniques and tools, such as H.E.L’s TSu, Phi-TEC I and II, and Simular, allow API and Pharma manufacturers to streamline safety evaluations, enhancing data accuracy, and with the aim of bringing safe and effective products to market faster and more efficiently.
Conclusion
Process safety is more than a regulatory requirement—at its core, it safeguards people, facilities, products, and reputation. Companies can elaborate their comprehensive safety portfolios by employing tools such as TSu, Phi-TEC I and II, and Simular, helping to prevent incidents, even at the largest scale. As pharmaceutical manufacturing grows in complexity, ongoing safety testing and automation innovation will remain pivotal for advancing industry standards in API production.